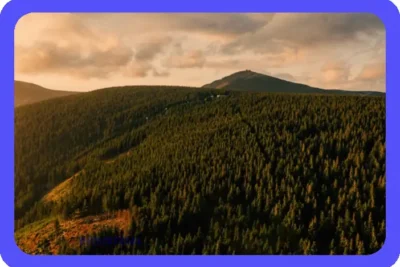
Ensayos de dureza Rockwell: Guía completa
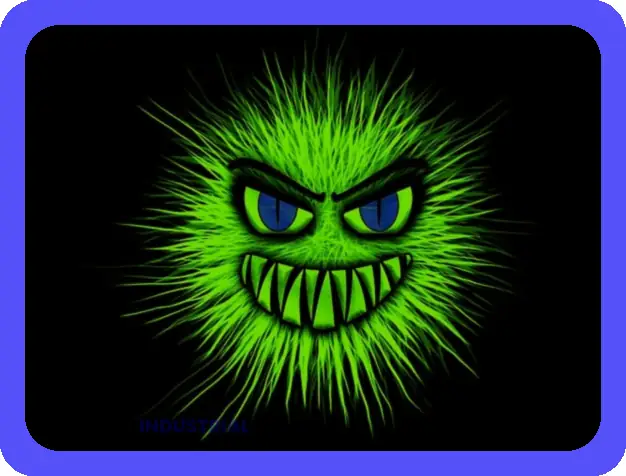
La dureza Rockwell es una propiedad fundamental de los materiales, especialmente metales, que indica su resistencia a la deformación plástica localizada. En el ámbito industrial, conocer la dureza Rockwell es esencial para el control de calidad y la selección adecuada de materiales para diferentes aplicaciones. Este parámetro nos proporciona información crucial sobre la resistencia, elasticidad, plasticidad y resistencia al desgaste del material.
Este artículo explorará en detalle los ensayos de dureza Rockwell, desentrañando sus fundamentos, procedimientos, escalas, ventajas, limitaciones y aplicaciones. Acompáñenos en este recorrido para comprender a fondo este método de ensayo crucial en la industria.
- ¿Qué es la Dureza Rockwell?
- Principios del Ensayo de Dureza Rockwell
- Escalas de Dureza Rockwell
- Procedimiento del Ensayo Rockwell
- Ventajas y Limitaciones del Ensayo Rockwell
- Aplicaciones del Ensayo de Dureza Rockwell
- Relación entre Dureza Rockwell y Otras Propiedades
- Mantenimiento y Calibración de los Equipos Rockwell
- Factores que Influyen en la Dureza Rockwell
- Interpretación de los Resultados Rockwell
- Comparación con Otros Métodos de Ensayo de Dureza
- Conclusión
- Preguntas Frecuentes
¿Qué es la Dureza Rockwell?
Escala Rockwell | Aplicación |
---|---|
Rockwell B (RB) | Metales blandos, como aluminio, latón y cobre. |
Rockwell C (RC) | Aceros endurecidos, metales duros y aleaciones de alta resistencia. |
Rockwell A (RA) | Materiales de dureza intermedia, como metales templados y endurecidos superficialmente. |
Rockwell E (RE) | Materiales de dureza intermedia, como fundición de acero. |
Rockwell F (RF) | Materiales de dureza intermedia, como aceros endurecidos. |
Rockwell G (RG) | Materiales de alta dureza, como carburo cementado. |
Rockwell H (RH) | Materiales de alta dureza, como aceros endurecidos. |
Rockwell K (RK) | Materiales de alta dureza, como aceros endurecidos. |
Rockwell 30N (30N) | Materiales de dureza intermedia, como plásticos y materiales blandos. |
Rockwell 45N (45N) | Materiales de dureza intermedia, como plásticos y materiales blandos. |
Rockwell 70N (70N) | Materiales de dureza intermedia, como plásticos y materiales blandos. |
Rockwell 85N (85N) | Materiales de dureza intermedia, como plásticos y materiales blandos. |
Rockwell 15T (15T) | Materiales muy blandos, como algunos plásticos. |
La dureza Rockwell no es una propiedad fundamental del material como lo es el módulo de Young, sino una medida de su resistencia a la indentación permanente. Es decir, cuantifica la oposición del material a ser deformado plásticamente por la penetración de un indentador. Un valor alto de dureza Rockwell implica una mayor resistencia a la deformación.
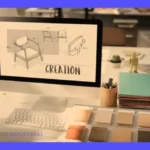
La dureza Rockwell se determina midiendo la profundidad de penetración de un indentador bajo una carga específica. A diferencia de otros métodos de ensayo de dureza, como Brinell o Vickers, el ensayo Rockwell ofrece una lectura directa de la dureza en la propia máquina, lo que simplifica el proceso y lo hace más rápido.
Este método es ampliamente utilizado en la industria debido a su simplicidad, rapidez y la pequeña huella que deja en la pieza, lo que lo convierte en un ensayo no destructivo en la mayoría de los casos. Esto permite su uso en piezas terminadas sin comprometer su funcionalidad.
Principios del Ensayo de Dureza Rockwell
Escala Rockwell | Penetrador | Fuerza Precarga (kgf) | Fuerza de Prueba (kgf) | Material Aplicable |
---|---|---|---|---|
Rockwell B (HRB) | Esfera de acero endurecido de 1/16" (1.58 mm) de diámetro | 10 | 100 | Metales blandos, aleaciones de cobre, metales no ferrosos |
Rockwell C (HRC) | Cono de diamante de 120 grados | 10 | 150 | Aceros endurecidos, metales duros, carburos cementados |
Rockwell A (HRA) | Cono de diamante de 120 grados | 10 | 60 | Materiales extremadamente duros, como carburos cementados y aceros endurecidos |
Rockwell E (HRE) | Esfera de acero endurecido de 1/8" (3.17 mm) de diámetro | 10 | 100 | Materiales más blandos que los probados con la escala B |
Rockwell F (HRF) | Esfera de acero endurecido de 1/16" (1.58 mm) de diámetro | 10 | 60 | Materiales con dureza intermedia entre las escalas B y E |
Rockwell 30N (HR30N) | Esfera de acero endurecido de 1/16" (1.58 mm) de diámetro | 10 | 15 | Materiales muy blandos, plásticos |
Rockwell 45N (HR45N) | Esfera de acero endurecido de 1/16" (1.58 mm) de diámetro | 10 | 45 | Materiales blandos, plásticos |
Rockwell 15N (HR15N) | Esfera de acero endurecido de 1/16" (1.58 mm) de diámetro | 10 | 15 | Materiales extremadamente blandos, plásticos |
El ensayo de dureza Rockwell se basa en la medición de la profundidad de penetración residual del indentador en el material. Primero, se aplica una precarga menor para asentar el indentador y eliminar cualquier irregularidad superficial. Luego, se aplica la carga principal, provocando una mayor penetración.
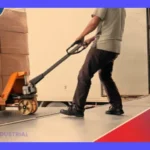
Finalmente, se retira la carga principal, dejando solo la precarga. La diferencia en la profundidad de penetración entre la precarga y la carga principal, una vez retirada esta ultima, es la que define la dureza Rockwell. Esta diferencia se mide directamente en la máquina de ensayo y se expresa en una escala específica, como Rockwell C (HRC) o Rockwell B (HRB).
El principio fundamental es que los materiales más duros presentarán una menor profundidad de penetración residual, resultando en un valor de dureza Rockwell más alto. Por el contrario, los materiales más blandos mostrarán una mayor penetración y un valor de dureza Rockwell más bajo.
Escalas de Dureza Rockwell
Escala | Descripción | Indentador | Fuerza Precarga (kgf) | Fuerza de Prueba (kgf) |
---|---|---|---|---|
Rockwell A (RA) | Para materiales muy duros, como aceros cementados, carburos cementados y materiales cerámicos duros. | Bola de diamante de 120° | 10 | 60 |
Rockwell B (RB) | Para materiales de dureza media, como aceros recocidos, latones y aluminio. | Bola de acero de 1/16" | 10 | 100 |
Rockwell C (RC) | Para materiales muy duros, como aceros templados y aleaciones de hierro. | Bola de diamante de 120° | 10 | 150 |
Rockwell D (RD) | Para materiales duros, como aceros templados y aleaciones de hierro. | Bola de diamante de 120° | 10 | 100 |
Rockwell E (RE) | Para materiales blandos, como aceros blandos, metales no ferrosos y plásticos duros. | Bola de acero de 1/8" | 10 | 100 |
Rockwell F (RF) | Para materiales blandos, como aleaciones de aluminio y magnesio. | Bola de acero de 1/16" | 10 | 60 |
Rockwell G (RG) | Para materiales muy duros, como carburos cementados. | Bola de diamante de 120° | 10 | 150 |
Rockwell H (RH) | Para materiales muy duros. | Bola de diamante de 120° | 10 | 60 |
Rockwell K (RK) | Para materiales blandos, como plásticos y metales blandos. | Bola de acero de 1/8" | 10 | 100 |
Rockwell 30N (30N) | Para materiales blandos, plásticos y materiales similares. | Bola de acero de 1/16" | 10 | 100 |
Rockwell 45N (45N) | Para materiales más duros que la escala 30N, plásticos, materiales elastoméricos. | Bola de acero de 1/16" | 10 | 100 |
Rockwell 85N (85N) | Para materiales duros que son más duros que las escalas 30N y 45N, plásticos, elastómeros. | Bola de acero de 1/16" | 10 | 100 |
Existen varias escalas de dureza Rockwell, cada una diseñada para diferentes rangos de dureza y tipos de materiales. La elección de la escala adecuada depende de la dureza estimada del material y del espesor de la pieza. Las escalas más comunes son:
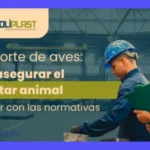
- Rockwell C (HRC): Utiliza un indentador cónico de diamante y una carga principal de 150 kgf. Se emplea para materiales muy duros, como aceros endurecidos.
- Rockwell B (HRB): Utiliza un indentador de bola de acero de 1/16" de diámetro y una carga principal de 100 kgf. Es adecuada para materiales de dureza media, como aceros blandos, aleaciones de aluminio y latón.
- Rockwell A (HRA): Utiliza un indentador cónico de diamante y una carga principal de 60 kgf. Se utiliza para materiales muy duros y frágiles, como carburos cementados.
Además de estas, existen otras escalas menos comunes, como las escalas D, E, F, G, K, L, M, P, R, S y V, cada una con un indentador y una carga principal específicos.
Procedimiento del Ensayo Rockwell
El procedimiento para realizar un ensayo de dureza Rockwell es relativamente sencillo:
- Preparación de la muestra: La superficie de la muestra debe estar limpia, lisa y libre de óxido u otros contaminantes.
- Selección de la escala: Se elige la escala Rockwell adecuada en función del material y su dureza estimada.
- Colocación de la muestra: La muestra se coloca firmemente sobre el yunque de la máquina de ensayo.
- Aplicación de la precarga: Se aplica una precarga para asentar el indentador.
- Aplicación de la carga principal: Se aplica la carga principal durante un tiempo determinado.
- Retiro de la carga principal: Se retira la carga principal, dejando solo la precarga.
- Lectura de la dureza: La máquina de ensayo muestra directamente el valor de dureza Rockwell en la escala seleccionada.
Ventajas y Limitaciones del Ensayo Rockwell
Ventajas:
- Rapidez y simplicidad: El ensayo de dureza Rockwell es rápido y fácil de realizar, lo que lo hace ideal para el control de calidad en producción.
- Lectura directa: La dureza se lee directamente en la máquina, sin necesidad de cálculos adicionales.
- Pequeña huella: La huella del indentador es pequeña, lo que permite realizar ensayos en piezas terminadas sin comprometer su funcionalidad.
Limitaciones:
- Sensibilidad a la preparación de la superficie: La superficie de la muestra debe estar bien preparada para obtener resultados precisos.
- Limitaciones para materiales muy delgados: En materiales muy delgados, la deformación puede afectar la medición.
- No apto para todos los materiales: Algunas escalas Rockwell son específicas para ciertos rangos de dureza y tipos de materiales.
Aplicaciones del Ensayo de Dureza Rockwell
El ensayo de dureza Rockwell se utiliza ampliamente en diversas industrias, incluyendo:
- Industria automotriz: Control de calidad de componentes, como engranajes, ejes y carrocerías.
- Industria aeroespacial: Verificación de la dureza de materiales críticos en aeronaves y naves espaciales.
- Industria metalúrgica: Caracterización de metales y aleaciones.
- Industria manufacturera: Control de calidad de productos fabricados con metales.
Relación entre Dureza Rockwell y Otras Propiedades
La dureza Rockwell está relacionada con otras propiedades mecánicas de los materiales, como la resistencia a la tracción y la resistencia al desgaste. Generalmente, un material con mayor dureza Rockwell también tendrá una mayor resistencia a la tracción y al desgaste. Sin embargo, esta relación no es siempre lineal y puede variar según el material y su microestructura.
Mantenimiento y Calibración de los Equipos Rockwell
Para asegurar la precisión y confiabilidad de los ensayos de dureza Rockwell, es esencial realizar un mantenimiento y calibración periódicos de los equipos. Esto incluye la verificación de la carga aplicada, la precisión del sistema de medición de la profundidad de penetración y la condición del indentador.
Factores que Influyen en la Dureza Rockwell
Diversos factores pueden influir en los resultados de un ensayo de dureza Rockwell, incluyendo:
- Composición química del material.
- Tratamientos térmicos.
- Deformación en frío.
- Tamaño de grano.
Interpretación de los Resultados Rockwell
La correcta interpretación de los resultados del ensayo de dureza Rockwell es crucial para tomar decisiones informadas sobre la calidad y el uso de los materiales. Es importante considerar la escala utilizada, las especificaciones del material y los posibles factores que puedan haber influido en la medición.
Comparación con Otros Métodos de Ensayo de Dureza
El ensayo de dureza Rockwell se compara a menudo con otros métodos de ensayo de dureza, como Brinell y Vickers. Cada método tiene sus propias ventajas y desventajas, y la elección del método más adecuado depende de la aplicación específica.
Conclusión
El ensayo de dureza Rockwell es una herramienta fundamental en la industria para evaluar la resistencia de los materiales metálicos. Su simplicidad, rapidez y precisión lo convierten en un método esencial para el control de calidad y la selección de materiales. Comprender los principios, procedimientos y aplicaciones del ensayo de dureza Rockwell es crucial para garantizar la calidad y el rendimiento de los productos en diversas industrias.
Preguntas Frecuentes
¿Cuál es la diferencia entre las escalas Rockwell B y C?
La escala Rockwell B utiliza un indentador de bola y es para materiales blandos, mientras que la C utiliza un indentador de diamante para materiales duros.
¿Qué precauciones se deben tomar al realizar un ensayo Rockwell?
Asegurar una superficie limpia y plana en la muestra, aplicar la carga correctamente y calibrar el equipo regularmente.
¿Cómo se relaciona la dureza Rockwell con la resistencia a la tracción?
Generalmente, una mayor dureza Rockwell indica una mayor resistencia a la tracción, pero la relación no es siempre lineal.
¿Es el ensayo Rockwell destructivo?
En la mayoría de los casos, no, ya que la huella del indentador es pequeña. Sin embargo, en piezas muy delgadas o frágiles, podría considerarse destructivo.
¿Qué factores pueden afectar la precisión del ensayo Rockwell?
La preparación de la superficie, la calibración del equipo y la elección correcta de la escala son factores cruciales para la precisión.
Deja una respuesta
Te Puede Interesar: