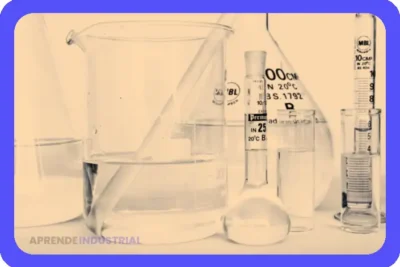
Identificación de riesgos específicos de seguridad en fábricas
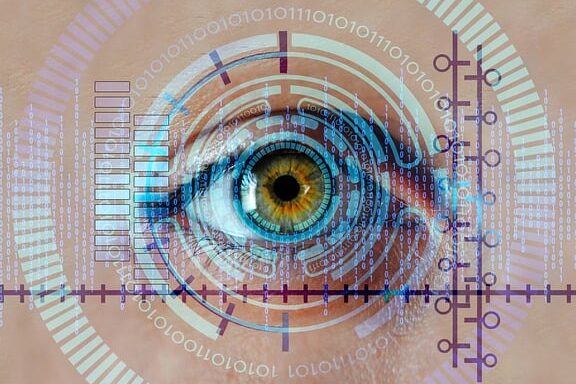
Introducción
La identificación de riesgos específicos de seguridad en fábricas es un aspecto fundamental en la gestión de la seguridad industrial. Cada área de producción presenta un conjunto único de peligros que pueden afectar tanto a los trabajadores como a la operación general de la planta. Desde la manipulación de maquinaria pesada hasta el manejo de sustancias químicas, los riesgos son variados y requieren una atención meticulosa. La falta de una identificación adecuada puede resultar en accidentes laborales, lesiones graves e incluso en la paralización de la producción, lo que puede tener un impacto significativo en la rentabilidad de la empresa.
Este artículo tiene como objetivo proporcionar una guía completa sobre la identificación de riesgos en fábricas, abordando las metodologías más efectivas para llevar a cabo este proceso. A lo largo del texto, se explorarán diferentes áreas de una fábrica, los riesgos asociados a cada una, y se ofrecerán pasos prácticos para implementar un sistema de identificación de riesgos. Además, se discutirán los beneficios y desafíos de esta práctica, así como los requisitos previos necesarios para su implementación. Al final, se espera que los lectores tengan una comprensión clara de cómo gestionar la seguridad en sus entornos laborales.
Importancia de la identificación de riesgos
La identificación de riesgos es un proceso crítico en la ingeniería industrial que no solo protege a los trabajadores, sino que también mejora la eficiencia operativa. Cuando se identifican y gestionan adecuadamente los riesgos, se pueden prevenir accidentes y lesiones, lo que a su vez reduce los costos asociados con la atención médica, las indemnizaciones y la pérdida de productividad. Además, un ambiente de trabajo seguro fomenta la moral de los empleados y puede aumentar la retención del personal.
Cálculo del Tiempo Estimado de Evacuación (TEE) en EmergenciasOtro aspecto importante es que la identificación de riesgos contribuye al cumplimiento de las normativas y regulaciones de seguridad laboral. Las empresas que no cumplen con estas regulaciones pueden enfrentar sanciones severas, además de dañar su reputación. Por lo tanto, implementar un sistema efectivo de identificación de riesgos no solo es una cuestión de ética, sino también de responsabilidad legal y económica.
Requisitos Previos
Antes de implementar una metodología de identificación de riesgos, es esencial contar con ciertos conocimientos y herramientas. En primer lugar, el personal involucrado debe tener una comprensión básica de los principios de seguridad industrial y de los tipos de riesgos que pueden presentarse en un entorno de fabricación. Esto incluye conocimientos sobre maquinaria, procesos de producción y materiales utilizados.
Además, es recomendable contar con herramientas de evaluación de riesgos, como listas de verificación, matrices de riesgos y software especializado. Estas herramientas facilitan la recopilación de datos y la evaluación de los riesgos identificados. También es útil tener acceso a normativas y estándares de seguridad, como los establecidos por la Organización Internacional de Normalización (ISO) y la Administración de Seguridad y Salud Ocupacional (OSHA).
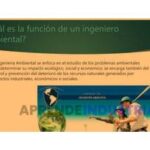
Por último, es fundamental que la alta dirección esté comprometida con la seguridad y la salud en el trabajo. Esto implica no solo proporcionar los recursos necesarios, sino también fomentar una cultura de seguridad en la que todos los empleados se sientan responsables de identificar y reportar riesgos.
Pasos de Implementación
La implementación de una metodología de identificación de riesgos puede dividirse en varios pasos clave. A continuación, se describen estos pasos de manera detallada:
1. Formación del equipo de trabajo
El primer paso es formar un equipo multidisciplinario que incluya representantes de diferentes áreas de la fábrica, como producción, mantenimiento, recursos humanos y seguridad. Este equipo será responsable de llevar a cabo la identificación de riesgos y debe contar con la experiencia y el conocimiento necesarios para abordar los peligros específicos de cada área.
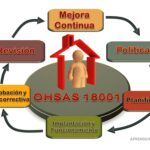
2. Recolección de información
Una vez formado el equipo, el siguiente paso es recopilar información sobre los procesos de producción y las condiciones de trabajo. Esto puede incluir la revisión de documentos existentes, como manuales de operación, informes de incidentes anteriores y auditorías de seguridad. También es útil realizar entrevistas con los trabajadores para obtener su perspectiva sobre los riesgos que enfrentan en su día a día.
3. Identificación de riesgos
Con la información recopilada, el equipo puede comenzar a identificar los riesgos específicos en cada área de la fábrica. Esto puede hacerse mediante la observación directa de los procesos, la realización de inspecciones de seguridad y el uso de listas de verificación. Es importante ser exhaustivo en esta etapa, ya que la identificación incompleta de riesgos puede llevar a la implementación de medidas de control inadecuadas.
4. Evaluación de riesgos
Una vez identificados los riesgos, el siguiente paso es evaluarlos en términos de probabilidad y severidad. Esto se puede hacer utilizando una matriz de riesgos, que permite clasificar los riesgos en función de su impacto potencial. Por ejemplo, un riesgo que tiene una alta probabilidad de ocurrir y una alta severidad debe ser tratado con mayor urgencia que uno con baja probabilidad y baja severidad.
```html
Probabilidad | Severidad | Clasificación |
---|---|---|
Alta | Alta | Crítico |
Alta | Baja | Moderado |
Baja | Alta | Moderado |
Baja | Baja | Bajo |
```
5. Desarrollo de medidas de control
Con la evaluación de riesgos completada, el equipo debe desarrollar medidas de control para mitigar los riesgos identificados. Esto puede incluir la implementación de procedimientos de trabajo seguros, la instalación de equipos de protección personal (EPP) y la mejora de la capacitación de los empleados. Es importante que estas medidas sean prácticas y factibles, y que se asignen responsabilidades claras para su implementación.
6. Monitoreo y revisión
Finalmente, es crucial establecer un sistema de monitoreo y revisión para evaluar la efectividad de las medidas de control implementadas. Esto puede incluir auditorías regulares, revisiones de incidentes y encuestas de satisfacción de los empleados. La retroalimentación continua permitirá realizar ajustes y mejoras en el sistema de identificación de riesgos.
Ejemplos prácticos de identificación de riesgos
Para ilustrar el proceso de identificación de riesgos, consideremos dos áreas comunes en una fábrica: la inyección de moldes y el área de ensamblaje.
Inyección de moldes
En el área de inyección de moldes, los riesgos pueden incluir:
Tropiezos por gránulos en el suelo: La acumulación de gránulos de plástico en el suelo puede causar caídas. Para mitigar este riesgo, se deben establecer procedimientos de limpieza regular y utilizar alfombrillas antideslizantes.
Quemaduras por barriles calientes: Los barriles que contienen material caliente pueden causar quemaduras. Se deben implementar barreras de seguridad y proporcionar EPP adecuado, como guantes resistentes al calor.
Lesiones por maquinaria: La maquinaria utilizada en el proceso de inyección puede causar atrapamientos. Es fundamental que se realicen mantenimientos regulares y que se instalen dispositivos de seguridad en las máquinas.
Área de ensamblaje
En el área de ensamblaje, los riesgos pueden incluir:
Tropiezos por alfombrillas: Las alfombrillas en el suelo pueden causar tropiezos. Se deben fijar adecuadamente y realizar inspecciones regulares para asegurarse de que estén en buen estado.
Atrapamientos de dedos: Las partes móviles de las máquinas pueden atrapar los dedos de los trabajadores. Se deben instalar resguardos y proporcionar capacitación sobre el uso seguro de las máquinas.
Fatiga por posturas inadecuadas: Los trabajadores pueden sufrir lesiones por adoptar posturas inadecuadas durante el ensamblaje. Se deben proporcionar herramientas ergonómicas y fomentar pausas regulares para evitar la fatiga.
Beneficios y Desafíos
Implementar una metodología de identificación de riesgos en fábricas conlleva numerosos beneficios, pero también presenta desafíos que deben ser abordados.
Beneficios
Reducción de accidentes: La identificación y gestión de riesgos contribuyen a la disminución de accidentes laborales, lo que se traduce en un ambiente de trabajo más seguro.
Mejora de la productividad: Un entorno seguro y saludable permite a los trabajadores desempeñarse mejor, lo que puede resultar en un aumento de la productividad.
Cumplimiento normativo: La identificación de riesgos ayuda a las empresas a cumplir con las regulaciones de seguridad, evitando sanciones y mejorando su reputación.
Desafíos
Resistencia al cambio: La implementación de nuevas medidas de seguridad puede encontrar resistencia por parte de los empleados. Es fundamental involucrarlos en el proceso y explicarles los beneficios de las nuevas prácticas.
Falta de recursos: Algunas empresas pueden enfrentar limitaciones en términos de tiempo y recursos para llevar a cabo una identificación de riesgos exhaustiva. Es importante priorizar las áreas de mayor riesgo y buscar soluciones creativas.
Mantenimiento del sistema: Una vez implementado, el sistema de identificación de riesgos debe ser monitoreado y actualizado regularmente. Esto requiere un compromiso continuo por parte de la dirección y el personal.
Conclusión
La identificación de riesgos específicos de seguridad en fábricas es un proceso esencial que no solo protege a los trabajadores, sino que también mejora la eficiencia y la rentabilidad de la empresa. A través de una metodología bien estructurada, es posible identificar, evaluar y mitigar los riesgos asociados a cada área de producción.
Es fundamental que las empresas se comprometan a implementar estas prácticas y a fomentar una cultura de seguridad en el trabajo. Al hacerlo, no solo se cumplen las normativas y se evitan sanciones, sino que también se crea un ambiente laboral más seguro y productivo. La seguridad en el trabajo no debe ser vista como un gasto, sino como una inversión en el bienestar de los empleados y en el éxito a largo plazo de la organización.
Referencias
Deja una respuesta
Te Puede Interesar: