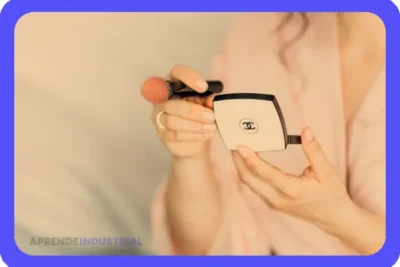
7 Herramientas de Ingeniería Industrial: Guía para Ingenieros
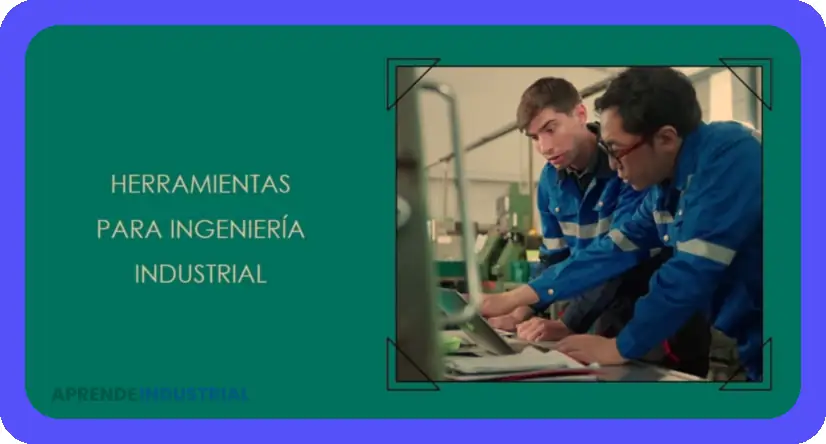
Las 7 herramientas de la calidad son fundamentales para cualquier ingeniero o profesional dedicado a la mejora continua. Estas herramientas, que incluyen el Diagrama de Pareto, el Diagrama de Ishikawa, histogramas, diagramas de dispersión, gráficos de control, hojas de recogida de datos y estratificación de datos, permiten identificar, analizar y resolver problemas de calidad de manera eficiente. Ingenieros industriales, ingenieros de procesos, y otros profesionales de la industria se benefician enormemente al emplear estas técnicas, pues optimizan los recursos y mejoran la toma de decisiones. Este artículo explorará en detalle cada una de estas herramientas de calidad, incluyendo ejemplos prácticos, consejos útiles y aplicaciones reales, para proporcionar a los lectores una comprensión completa de su uso en contextos industriales y de ingeniería. El artículo busca equipar a los lectores con el conocimiento práctico necesario para aplicar estas herramientas efectivamente en la resolución de problemas.
Este artículo tiene el propósito de profundizar en el tema de las 7 herramientas de la calidad para ingenieros. Exploraremos cada una de las herramientas, proporcionando ejemplos concretos y explicaciones detalladas para facilitar la comprensión y la aplicación práctica en un entorno de ingeniería. Aprenderás cómo utilizar cada herramienta para identificar problemas, analizar sus causas y proponer soluciones efectivas para la mejora continua en los procesos de producción. Se busca proporcionar un conocimiento profundo de cada herramienta, incluyendo su utilidad, funcionamiento y aplicación práctica, para ayudar a los ingenieros a tomar mejores decisiones y mejorar los resultados de sus proyectos.
- Comprendiendo el Diagrama de Pareto: Priorizando las Causas Principales
- Desentrañando el Diagrama de Ishikawa (Espina de Pescado): Explorando Causas Raíz
- Visualizando la Distribución de Datos: Análisis con Histogramas
- Desentrañando Relaciones entre Variables: Diagramas de Dispersión
- Monitoreando Variaciones de Procesos: La Importancia de los Gráficos de Control
- Registrando Datos Relevantes: Hojas de Recogida de Datos
- Agrupando Datos para Análisis: La Estratificación
- Conclusión
- Preguntas Frecuentes
Comprendiendo el Diagrama de Pareto: Priorizando las Causas Principales
Causa | Porcentaje de Defectos |
---|---|
Contaminación en la sala limpia | 45% |
Fallo en el proceso de litografía | 28% |
Defectos en el material base | 15% |
Errores de ensamblaje | 7% |
Fluctuaciones de voltaje | 5% |
El Diagrama de Pareto, también conocido como el principio 80/20, es una herramienta visual que ayuda a identificar las causas principales de un problema, centrando los esfuerzos en las que generan el mayor impacto. Los ingenieros utilizan esta herramienta para concentrarse en los pocos factores que causan la mayor parte del problema. Esto permite optimizar el uso de recursos y tiempo, enfocando las estrategias de mejora en las áreas de mayor impacto.
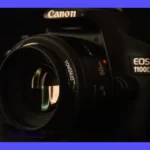
Para construir un Diagrama de Pareto, se recopilan datos sobre las causas del problema. Se ordenan las causas de mayor a menor impacto, y luego se grafican los resultados. Un gráfico típico muestra la cantidad de veces que ocurre cada causa y una línea que representa el porcentaje acumulado de ocurrencia. Los ingenieros industriales pueden ver claramente qué causas representan la mayor parte de los problemas y enfocar sus esfuerzos en ellas.
Ejemplo: Imagina que en una fábrica de autos se observan defectos en la pintura. Recopilando datos, se encuentra que el 80% de los defectos se debe a un problema con la presión de pulverización. Con este dato, los ingenieros pueden enfocarse en la presión de pulverización para mejorar la calidad de la pintura y reducir los defectos. Esto nos muestra la eficiencia del enfoque Pareto en la solución de problemas.
Otra aplicación de esta herramienta de calidad permite determinar las fallas más frecuentes en un proceso productivo, para así centrar las acciones de mejora en las fallas que más se repiten.
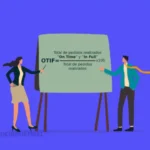
Un punto clave del Diagrama de Pareto es la concentración en las causas más importantes. Se busca priorizar la acción en las áreas que generan mayor impacto. Esto conlleva a una mejora en la eficiencia y eficacia, optimizando el tiempo y los recursos invertidos.
Desentrañando el Diagrama de Ishikawa (Espina de Pescado): Explorando Causas Raíz
Problema | Causa Raíz (Categoría y Ejemplo) |
---|---|
Baja productividad en la línea de ensamblaje | Maquinaria (Máquina X requiere mantenimiento frecuente, causando paradas imprevistas) |
Alta tasa de abandono de clientes | Servicio al Cliente (Respuestas lentas a las consultas, falta de empatía por parte del personal) |
Aumento de costos de producción | Materiales (Incremento del precio de la materia prima A debido a la escasez global) |
Retrasos en la entrega de proyectos | Recursos Humanos (Falta de personal capacitado para tareas específicas, sobrecarga de trabajo) |
Defectos en el producto final | Proceso (Falta de control de calidad en la etapa de ensamblaje, deficiencias en el entrenamiento del personal) |
Disminución en la satisfacción del empleado | Medio Ambiente Laboral (Falta de comunicación interna, ambiente de trabajo estresante) |
El Diagrama de Ishikawa, también conocido como diagrama de causa-efecto, es una herramienta gráfica que ayuda a identificar y analizar las causas raíz de un problema. Esta herramienta visual, en forma de espina de pescado, permite organizar y categorizar las posibles causas de un problema en diferentes ramas relacionadas con los factores que impactan un proceso específico. La herramienta es utilizada por los ingenieros industriales para comprender las causas subyacentes de un problema, en lugar de sólo focalizarse en los síntomas.
Los ingenieros utilizan el diagrama para identificar las diversas categorías de causas potenciales, como las materias primas, el proceso, la mano de obra y el ambiente. Para ello, recogen datos y evalúan cada una de las ramas para entender cómo cada factor puede afectar el resultado final.
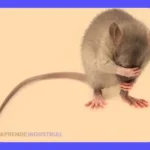
La aplicación práctica del Diagrama de Ishikawa en la industria es invaluable. Imagina una línea de producción con una tasa creciente de fallas. Un ingeniero industrial utilizaría esta herramienta para identificar posibles causas, como la calidad de las materias primas, los ajustes de la maquinaria, la formación del equipo de trabajo, o las condiciones ambientales.
La organización sistemática de causas permite una comprensión holística del problema, que facilita una mejor solución.
La construcción de un diagrama de Ishikawa involucra la participación de diferentes personas involucradas en el proceso, lo que puede ayudar a identificar perspectivas relevantes y a profundizar en la comprensión del problema.
Visualizando la Distribución de Datos: Análisis con Histogramas
Rango de Ingresos | Frecuencia |
---|---|
0 - 20 | 150 |
20 - 40 | 275 |
40 - 60 | 310 |
60 - 80 | 200 |
80 - 100 | 75 |
100+ | 40 |
Los histogramas son gráficos que muestran la distribución de datos. Permiten visualizar la frecuencia de ocurrencia de valores dentro de un rango determinado, permitiendo identificar patrones y variaciones. Los ingenieros utilizan los histogramas para comprender mejor la variación natural en los procesos y si hay algún desvío que requiera atención.
Imaginemos una máquina que produce tornillos. Usando un histograma, un ingeniero puede visualizar la longitud de cada tornillo y ver si la distribución de datos se concentra en el rango deseado, o si existe una tendencia a la producción de tornillos demasiado largos o cortos. Esto permite detectar posibles problemas en el proceso que deben corregirse.
Los ingenieros industriales también utilizan los histogramas para identificar patrones y tendencias en los datos. Si se observa un patrón consistente en los histogramas, se puede determinar si se requiere una mejora en el proceso o si se han introducido cambios que requieren un seguimiento continuo.
Una adecuada interpretación del histograma permite detectar anomalías o tendencias y así diagnosticar problemas en el proceso.
Desentrañando Relaciones entre Variables: Diagramas de Dispersión
Los diagramas de dispersión son gráficos que representan la relación entre dos variables. Los ingenieros los utilizan para ver si existe una relación entre dos características de un proceso y si son lineal o no lineal.
En un proceso de producción, un ingeniero puede analizar cómo la temperatura del horno afecta el color de la cerámica. Un diagrama de dispersión puede mostrar si hay una relación lineal entre estos dos factores, lo que permitirá saber qué temperatura produce un mejor color.
Por ejemplo, en un proceso de producción de bienes, es posible graficar y examinar la relación que existe entre dos variables clave para este, como la cantidad de personal y la eficiencia del mismo, permitiendo optimizar la combinación ideal para mejorar los resultados.
Identificando las posibles correlaciones entre las variables, los ingenieros pueden optimizar procesos y tomar decisiones con bases más sólidas.
Monitoreando Variaciones de Procesos: La Importancia de los Gráficos de Control
Los gráficos de control son herramientas visuales que monitorean la variabilidad de un proceso con el tiempo. Los ingenieros los usan para detectar cambios y anomalías que puedan indicar posibles problemas en el proceso. Se identifican con facilidad las variaciones en los procesos.
Imagine un proceso de llenado de botellas. Un ingeniero industrial utilizaría un gráfico de control para monitorear el volumen de llenado de las botellas con el tiempo. Así se detectan cualquier desviación de la norma en el volumen de llenado, lo que ayuda a entender si el proceso está dentro de los parámetros deseados.
Esta herramienta permite optimizar los procesos e identificar las causas que generan variabilidad en ellos. Un uso práctico es identificar si las causas de la variación son de carácter aleatorio o si existen causas especiales que deben ser corregidas.
Registrando Datos Relevantes: Hojas de Recogida de Datos
Las Hojas de Recogida de Datos (HRD) son formularios o plantillas específicas para registrar información relevante. Los ingenieros las utilizan para recoger información precisa, detallada y organizada. Esta metodología se vuelve crucial a la hora de monitorear y analizar un proceso de manera efectiva.
Imagina un ingeniero que quiere analizar la cantidad de piezas defectuosas en una línea de producción. Un ingeniero industrial diseñaría una hoja de recogida de datos específica para registrar la cantidad y el tipo de defecto en cada pieza producida.
Esto proporciona la información necesaria para analizar patrones y tendencias. Esta información de buena calidad se vuelve fundamental para determinar qué se debe mejorar.
Un diseño preciso de las HRD permite obtener datos completos y necesarios para llevar a cabo análisis detallados.
Agrupando Datos para Análisis: La Estratificación
La estratificación de datos es una técnica que separa los datos en categorías. Los ingenieros la usan para analizar los datos en distintos grupos y obtener conclusiones más precisas. Por ejemplo, en una fábrica de calzado, los datos de calidad se podrían estratificar por tipo de zapato, tamaño, o turno de trabajo.
Imaginen un ingeniero de procesos buscando la causa raíz de los retrasos en la entrega de pedidos. La estratificación de los datos por tipo de pedido, región de entrega, o método de transporte permite identificar patrones y determinar si hay problemas específicos en algunos grupos de pedidos.
Esta herramienta permite obtener una visión más precisa de los datos y tomar decisiones más informadas. Al agrupar los datos, es posible detectar patrones significativos que, de otra manera, pasarían desapercibidos.
Un enfoque estratificado ofrece la posibilidad de identificar las diferencias de desempeño entre diferentes grupos de datos, lo cual permite una comprensión más precisa de la situación general.
Conclusión
las 7 herramientas de la calidad son instrumentos esenciales para los ingenieros y profesionales de la industria dedicados a la mejora continua. Desde el Diagrama de Pareto, para priorizar las causas principales, hasta la Estratificación, para analizar datos en categorías, estas herramientas brindan una comprensión profunda del funcionamiento de los procesos y permiten la toma de decisiones informada para optimizar recursos y mejorar la eficiencia. Dominar estas herramientas de ingeniería industrial es crucial para contribuir a la mejora continua en cualquier empresa, desde la producción hasta la atención al cliente. Su uso sistemático y correcto permite la obtención de datos para la toma de decisiones con base en información objetiva y confiable.
La aplicación adecuada de estos instrumentos permite la identificación y el análisis de problemas y la priorización de soluciones. Estas herramientas de calidad son herramientas esenciales en el campo industrial, que resultan en el aumento de la productividad, la eficiencia, y la optimización de recursos. Además, ofrecen la posibilidad de comprender mejor el proceso para la toma de decisiones y llevar a cabo una mejora continua.
Preguntas Frecuentes
¿Cuál es la diferencia principal entre el Diagrama de Pareto y el Diagrama de Ishikawa?
El Diagrama de Pareto prioriza las causas más significativas, mientras que el Diagrama de Ishikawa busca las causas raíces de un problema. El primero se centra en la importancia y el segundo en la raíz del problema.
¿Cuándo es apropiado utilizar un histograma en lugar de un diagrama de dispersión?
Un histograma es útil para visualizar la distribución de una única variable, mientras que un diagrama de dispersión se usa para mostrar la relación entre dos variables.
¿Cómo se puede asegurar la precisión en la recolección de datos para las Hojas de Recogida de Datos?
Para asegurar la precisión, se deben definir claramente los parámetros y las variables a medir, y se debe instruir al personal en la forma correcta de registrar la información. Asegurarse de que el instrumento de medición esté calibrado y se eviten sesgos de observación.
¿En qué situaciones la estratificación de datos es más efectiva que un simple análisis de datos no estratificados?
La estratificación es más efectiva cuando se busca identificar diferencias en las características o patrones de las distintas categorías de datos. Esto permite analizar las causas diferenciales de un problema y encontrar soluciones específicas para cada categoría.
¿Qué herramienta de calidad es más adecuada para identificar correlaciones entre variables?
El Diagrama de Dispersión es la herramienta de calidad más adecuada para determinar la relación entre dos variables y descubrir si existe una correlación entre ellas.
Deja una respuesta
Te Puede Interesar: