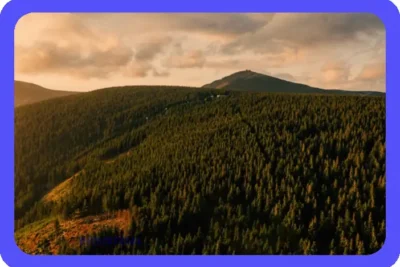
Diseñar un almacén: Guía de diseño de almacenes
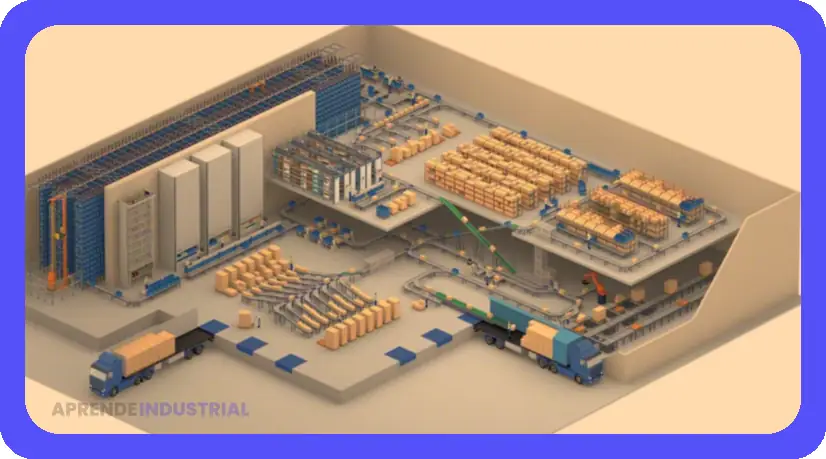
El diseño de almacenes es una disciplina crucial para cualquier empresa que maneja inventarios. Un diseño de almacén bien planificado no solo optimiza el espacio, sino que también impacta directamente en la eficiencia operativa, la reducción de costos y la satisfacción del cliente. Diseñar un almacén implica mucho más que simplemente organizar estantes. Requiere un análisis profundo de las necesidades logísticas, la previsión de crecimiento y una estrategia de almacenamiento adaptada a las características del producto y la demanda.
Este artículo explorará en detalle los aspectos clave del diseño de almacenes, ofreciendo una guía práctica para comprender las consideraciones fundamentales. Desde la recepción de la mercancía hasta la expedición, exploraremos cada etapa, ofreciendo estrategias para optimizar la gestión de inventario y maximizar la eficiencia del almacén. Veremos cómo un diseño de almacén adecuado permite a las empresas gestionar eficientemente los flujos de entrada y salida de mercancía, minimizando los tiempos de espera y optimizando los procesos de almacenamiento, en última instancia impactando positivamente en la rentabilidad de la empresa.
Planificación Estratégica del Diseño de Almacén
Meta Estratégica | Resultado Esperado (2023) |
---|---|
Reducción del tiempo de picking en un 15% | Se logró una reducción del 18% en el tiempo promedio de picking, gracias a la optimización del layout y la implementación de un sistema de gestión de almacenes (WMS). |
Incremento de la capacidad de almacenamiento en un 10% sin aumentar la superficie | Se logró un incremento del 12% en la capacidad de almacenamiento mediante la optimización de la altura de las estanterías y la implementación de un sistema de almacenamiento dinámico. |
Reducción del índice de errores en la preparación de pedidos en un 5% | Se redujo el índice de errores en un 7%, gracias a la implementación de un sistema de verificación de pedidos y la capacitación del personal. |
Mejora de la seguridad en el almacén, reduciendo los accidentes en un 20% | Se redujo la tasa de accidentes en un 25%, gracias a la implementación de nuevas medidas de seguridad, como la señalización mejorada y la formación específica en manipulación de mercancías. |
Optimización de los flujos de trabajo para reducir la congestión | Se observó una mejora significativa en la fluidez del trabajo, con una reducción del 15% en los puntos de congestión, gracias a la redistribución del espacio y la mejora en la gestión de los pasillos. |
En el diseño de almacenes, la planificación estratégica es fundamental. Esta etapa se centra en comprender las necesidades específicas de la empresa, incluyendo el tipo de mercancía que se almacenará, los volúmenes de entrada y salida, las necesidades de personal y la previsión de crecimiento futuro.
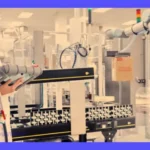
Una vez definida la estrategia de diseño de almacén, se deben identificar las características del producto. Por ejemplo, el tamaño, el peso, la fragilidad, la peligrosidad y la forma de los artículos serán factores determinantes en la selección del sistema de almacenamiento. La rotación del producto (alta, media o baja) también influye en el diseño del almacén, ya que determinará la accesibilidad necesaria para extraer los artículos con mayor rapidez.
La evaluación de la demanda y la previsión de crecimiento juegan un papel fundamental en la planificación estratégica. Una estimación precisa de las necesidades futuras, permitirá diseñar un almacén con la capacidad necesaria para hacer frente a los volúmenes esperados. Planificar anticipadamente garantiza la flexibilidad y evita futuras adaptaciones costosas.
Se debe contemplar la gestión de los posibles riesgos que se puedan presentar en la logística de la mercancía para un mejor desempeño del almacén.
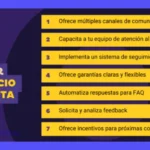
Es esencial la evaluación del espacio disponible. Un análisis meticuloso del área disponible permitirá determinar la distribución óptima de las distintas zonas del almacén.
Secciones Clave en un Diseño de Almacén
Sección | Descripción y Consideraciones |
---|---|
Recepción de Mercancías | Área para la descarga, inspección y registro de materiales entrantes. Debe incluir espacio suficiente para la manipulación de mercancías, muelles de carga con rampas niveladoras, y sistemas de escaneo de códigos de barras para un eficiente control de inventario. Idealmente, se ubica cerca de las zonas de almacenamiento para minimizar el movimiento interno. |
Almacenamiento | Zona principal donde se almacenan los productos. Debe estar organizada según un sistema de ubicación específico (ej: FIFO, LIFO) y considerar la rotación de inventario, la altura del techo para maximizar el espacio vertical, y el tipo de estanterías o sistemas de almacenamiento (estanterías convencionales, estanterías selectivas, estanterías de palets, etc.) Se debe considerar la seguridad contra incendios y el acceso adecuado para carretillas elevadoras. |
Preparación de Pedidos | Área destinada a la selección y empaque de los productos para su envío. Se debe optimizar el flujo de trabajo para asegurar la eficiencia y precisión en la preparación de los pedidos. Sistemas de picking como "picking por voz" o sistemas WMS pueden mejorar la productividad. Debe haber espacio suficiente para el empaquetado y etiquetado de los productos. |
Expedición | Área de carga y salida de mercancías. Debe contar con muelles de carga, espacio para la carga de camiones y vehículos de reparto, y sistemas de gestión para el seguimiento de los envíos. La ubicación debe facilitar el acceso a las carreteras principales y reducir los tiempos de entrega. |
Oficinas y Área de Personal | Espacio para las oficinas administrativas, vestuarios, baños y áreas de descanso para el personal. Debe cumplir con las normas de seguridad y ergonomía para garantizar un ambiente de trabajo confortable y seguro. |
El diseño de almacenes se compone de tres zonas principales: recepción, almacenamiento y expedición. Cada una de estas secciones debe estar diseñada y optimizada para asegurar la fluidez del proceso logístico.
Recepción de Mercancías
La zona de recepción se encarga de la gestión de las entradas de mercancía, incluyendo el control de calidad y la adaptación al sistema de almacenamiento. Una correcta organización de la recepción minimiza los retrasos y evita problemas logísticos. La correcta gestión de la recepción de la mercancía, además de tener un control de calidad, asegura que todos los productos estén en óptimas condiciones.
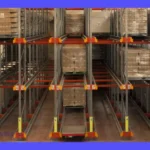
La gestión de las entradas debe ser precisa, incluyendo la verificación de la documentación, la identificación de la mercancía y la confirmación de la cantidad recibida. Además, la zona de recepción debe estar bien iluminada y con accesos adecuados para facilitar la descarga y la verificación de la mercancía.
Considera la importancia de contar con personal capacitado en recepción de mercancía, para asegurar la eficiencia y el control de calidad. La recepción de mercancías puede ser un factor clave para garantizar que la mercancía llegue a las demás áreas de forma segura.
Almacenamiento: Optimización del Espacio
La zona de almacenamiento es el núcleo del diseño de un almacén. Su diseño debe adaptarse a la rotación del producto, priorizando la accesibilidad y la velocidad de extracción según su movimiento. Un diseño adecuado de almacenamiento puede maximizar la eficiencia del espacio y reducir los costos asociados con la gestión de inventario.
Para optimizar el espacio de almacenamiento, se pueden usar diferentes sistemas, como estanterías, bloques o sistemas de compactación. La elección de estos sistemas dependerá del tipo de producto y su rotación. Por ejemplo, las estanterías de alta densidad son ideales para productos con baja rotación, mientras que los bloques son más adecuados para productos con alta rotación.
La ubicación de los productos debe ser estratégica para facilitar su extracción. Los productos con alta rotación deben ubicarse en zonas de fácil acceso, mientras que los productos con baja rotación pueden ubicarse en zonas de menor prioridad.
Expedición: Preparación y Embalaje de Pedidos
La zona de expedición se centra en la preparación y el embalaje de pedidos. Aquí, optimizar los procesos es fundamental para una salida eficiente y rápida de los pedidos.
Esta zona debe tener zonas de consolidación y clasificación para agilizar el proceso de carga. La optimización de la expedición es crucial para cumplir con los plazos de entrega y garantizar la satisfacción del cliente. La agilidad de la expedición impactará positivamente en el tiempo de entrega.
Un diseño eficaz permite una mayor velocidad en la preparación de los pedidos, permitiendo cumplir con las demandas de los clientes. La correcta distribución del espacio en esta zona facilita la organización de los pedidos y la gestión de las operaciones. Asegura que los procesos de consolidación y clasificación sean óptimos.
Sistemas de Almacenamiento y Manejo de Materiales
Sistema | Descripción | Ventajas | Desventajas |
---|---|---|---|
Estanterías de paletización | Sistema de almacenamiento de alta densidad que utiliza paletas para almacenar mercancías. | Alta capacidad de almacenamiento, fácil acceso a las mercancías, adecuado para grandes volúmenes. | Requiere espacio considerable, puede ser costoso de implementar. |
Estanterías de flujo gravitatorio | Sistema de almacenamiento donde las mercancías se mueven por gravedad a través de las estanterías. | Flujo de mercancías eficiente, ideal para FIFO (First-In, First-Out), reduce la manipulación manual. | Menos flexible que las estanterías de paletización, puede ser costoso. |
Almacenamiento compacto | Sistemas como estanterías móviles o sistemas de almacenamiento de alta densidad que maximizan el espacio. | Optimización del espacio, ideal para almacenes pequeños, alta capacidad de almacenamiento. | Acceso limitado a las mercancías, requiere un sistema de control preciso, puede ser costoso. |
Transportadores | Sistemas que mueven mercancías entre diferentes puntos del almacén. | Automatización del flujo de materiales, aumento de la eficiencia, reducción de costes laborales. | Costoso de implementar y mantener, requiere espacio suficiente, puede ser complejo de configurar. |
Grúas y carretillas elevadoras | Equipos utilizados para mover y colocar mercancías en las estanterías. | Versátil, adecuado para diferentes tipos de mercancías, fácil de usar. | Requiere operadores capacitados, puede ser costoso, potencialmente peligroso si no se utiliza correctamente. |
Los sistemas de almacenamiento influyen directamente en la eficiencia del diseño del almacén. La elección del sistema adecuado depende de factores como el tipo de mercancía, la rotación, el espacio disponible y el presupuesto.
Sistemas de Estanterías y Bloques
El uso de estanterías y bloques es crucial para optimizar el espacio y la accesibilidad de los productos. Las estanterías pueden ser de diferentes tipos, como estanterías para paletas, estanterías para cajones, y estanterías retráctiles, entre otras.
La elección de un tipo de estantería debe considerar la altura del producto, su peso y las necesidades de espacio. Un mal sistema de estanterías puede obstaculizar el proceso de almacenamiento y la salida de los productos.
Sistemas de Compactación y Automación
Los sistemas de compactación permiten maximizar el uso del espacio vertical del almacén. Los sistemas de compactación reducen el espacio requerido para almacenar mercancía, lo que es especialmente útil para productos con baja rotación.
La automación juega un papel cada vez más importante en los diseños de almacenes. Los sistemas automatizados, como robots de picking, permiten una gestión más eficiente del movimiento de productos dentro del almacén.
Consideraciones adicionales para el Diseño de Almacén
La tecnología juega un papel crucial en la optimización del diseño de almacenes. La implementación de sistemas de gestión de almacenes (WMS) ayuda a controlar el inventario, optimizar los procesos y mejorar la eficiencia.
Tecnología para Optimizar el Diseño de Almacén
La automatización y la implementación de sistemas de gestión de almacenes (WMS) optimizan los procesos dentro del almacén. Un diseño inteligente integra la tecnología para controlar y monitorear el inventario, minimizar tiempos de espera y maximizar el espacio disponible.
Las tecnologías incluyen la identificación por radiofrecuencia (RFID), la trazabilidad y los sistemas de gestión de almacenes (WMS). Estos sistemas ofrecen una mejor visibilidad de los procesos dentro del almacén.
Seguridad y Ergonomía en el Diseño de Almacén
La seguridad y la ergonomía son aspectos clave en el diseño de almacenes. Los diseños deben priorizar la seguridad de los empleados, minimizar los esfuerzos físicos y asegurar el correcto manejo de los materiales.
Por ejemplo, las elevaciones y pasillos deben tener un ancho adecuado. La iluminación debe ser suficiente y se debe asegurar una ventilación óptima.
Conclusión
Un diseño de almacén eficaz es fundamental para la operatividad y la rentabilidad de una empresa. Un diseño de almacén bien planificado optimiza el espacio, reduce los costos y mejora el tiempo de respuesta, mejorando así la eficiencia general de la empresa.
La planificación estratégica, la elección de los sistemas de almacenamiento, la consideración de la tecnología, la seguridad y la ergonomía son aspectos claves para obtener un diseño de almacén óptimo que responda a las necesidades específicas de la empresa.
Preguntas Frecuentes
¿Cómo se determina la rotación de un producto?
La rotación de un producto se determina mediante el cálculo de la frecuencia con que se vende o utiliza en un periodo específico. Se pueden utilizar datos de ventas históricas y tendencias para predecir futuras necesidades.
¿Qué tipo de estanterías son más adecuadas para productos pesados?
Las estanterías diseñadas para soportar el peso y la estabilidad de los productos pesados, así como las estanterías de alta densidad, son las más adecuadas.
¿Cuál es la importancia de la seguridad en un diseño de almacén?
La seguridad en un diseño de almacén es crucial para evitar accidentes y proteger a los empleados, minimizando los riesgos laborales y costes.
¿Cómo se puede minimizar el espacio para productos de baja rotación?
Para minimizar el espacio para productos de baja rotación, se pueden utilizar sistemas de compactación, como estanterías retráctiles y zonas de almacenaje especiales para productos poco frecuentes.
¿Cómo puedo optimizar los procesos de picking y packing?
La optimización de los procesos de picking y packing se puede lograr mediante la implementación de sistemas automatizados y rutas de trabajo eficientes, que agilizan y minimizan el tiempo de preparación de pedidos.
Deja una respuesta
Te Puede Interesar: