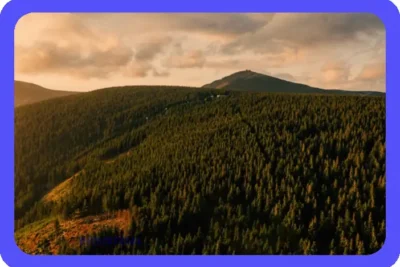
Zonas de un Almacén: 10 Áreas Clave | Guía
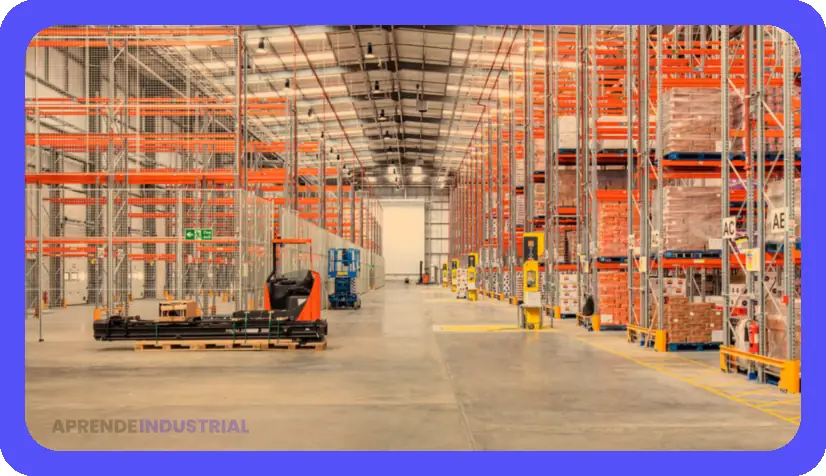
El diseño eficiente de un almacén es fundamental para la optimización de las operaciones logísticas. Una distribución inteligente de las zonas de un almacén impacta directamente en la productividad, la eficiencia y la rentabilidad de cualquier negocio que maneja inventario. La planificación adecuada de las áreas de almacen es crucial para un flujo de trabajo fluido, minimizando retrasos y maximizando la utilización del espacio disponible. Una correcta distribución de las zonas de almacen permite una gestión óptima del stock y un servicio al cliente más eficiente.
Este artículo profundizará en el diseño y planificación de un almacén, explorando en detalle cada una de las zonas de un almacén esenciales para su correcto funcionamiento. Analizaremos las características, funciones y requisitos de cada área, proporcionando una guía completa para la creación de un almacén eficiente y productivo. Aprenderemos cómo las diferentes áreas interactúan entre sí y cómo su diseño adecuado puede mejorar la gestión del inventario, la preparación de pedidos, y la expedición de mercancía. El objetivo es proporcionar una comprensión clara de cómo optimizar las zonas de almacen para lograr una gestión logística eficiente.
Puntos clave
- Zonas de carga y descarga: Optimización del flujo de mercancías.
- Recepción y control: Procesamiento eficiente de los productos entrantes.
- Almacenamiento: Estrategias para la optimización del espacio y la gestión del inventario.
- Preparación de pedidos: Métodos para una recolección rápida y precisa.
- Expedición: Procesos para un envío eficiente y seguro.
- Oficinas y servicios: Soporte administrativo y áreas de descanso.
- Mantenimiento: Garantizar la operatividad del almacén.
- Devoluciones: Gestión eficiente de las devoluciones de mercancía.
- Reenvasado: Adaptación del embalaje a las necesidades específicas.
- Cuarentena: Almacenamiento temporal para productos que requieren inspección.
- Zonas de Carga y Descarga: El Corazón de las Operaciones
- Recepción y Control: El Primer Paso en la Cadena de Suministro
- El Almacenaje: Optimizando el Espacio y la Gestión del Inventario
- Preparación de Pedidos: Agilidad y Precisión en la Recolección
- Expedición: El Envío Eficiente de la Mercancía
- Oficinas y Servicios: El Soporte Administrativo del Almacén
- Mantenimiento: Garantizando la Operatividad
- Devoluciones: Gestión Eficiente de la Mercancía Retornada
- Reenvasado: Adaptando el Embalaje a las Necesidades
- Cuarentena: Almacenamiento Temporal de Productos
- Conclusión
- Preguntas Frecuentes
Zonas de Carga y Descarga: El Corazón de las Operaciones
Factor Clave | Impacto en la Eficiencia |
---|---|
Diseño de la zona (accesibilidad, espacio de maniobra) | Un diseño adecuado reduce tiempos de espera y congestionamiento, mejorando la productividad en un 15-20%. Un mal diseño puede aumentar los costos de operación hasta un 30%. |
Señalización y marcación vial | Señalización clara y precisa disminuye errores de ubicación y accidentes, aumentando la seguridad y eficiencia en un 10%. |
Equipamiento (rampas, muelles de carga, elevadores) | El mantenimiento adecuado y la selección de equipos apropiados para el volumen de carga reducen los tiempos de carga/descarga hasta en un 25%. Equipos obsoletos incrementan las reparaciones y el tiempo muerto. |
Sistemas de gestión de almacenaje (WMS) | La integración de un WMS optimiza la asignación de recursos, minimizando los desplazamientos y mejorando la precisión en la gestión de inventario hasta en un 40%. |
Personal capacitado | Un equipo entrenado en procedimientos seguros y eficientes reduce errores, aumenta la productividad y mejora la seguridad en un 12%. |
Tecnología de apoyo (PDA's, escáneres) | La automatización de procesos a través de tecnología reduce errores humanos, acelera el proceso de carga/descarga y optimiza la gestión de información hasta un 35%. |
Las zonas de carga y descarga son el punto de entrada y salida de la mercancía en el almacén. Un diseño adecuado de esta área es crucial para la eficiencia global. Debemos considerar el espacio suficiente para maniobrar camiones y equipos de carga. La ubicación estratégica de muelles de carga y descarga optimiza el flujo. Además, la instalación de rampas y sistemas de carga adecuados agiliza las operaciones.
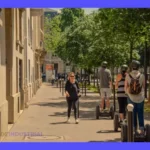
Un buen diseño minimiza el tiempo de espera de los camiones y la congestión en el área. Se recomienda que la zona esté bien iluminada y señalizada para una mayor seguridad. El uso de sistemas de gestión de muelles puede ayudar a programar las llegadas y salidas, mejorando la eficiencia. Los andenes deben estar equipados con los elementos necesarios, como protecciones contra impactos y sistemas de seguridad.
Es importante considerar el tamaño del almacén y el volumen de carga y descarga para calcular el tamaño y la disposición de los muelles de carga. Asimismo, es crucial planificar la ubicación de las zonas de espera para camiones, asegurando un flujo de tránsito fluido. Se recomienda incorporar tecnología para la gestión de muelles, agilizando el proceso de carga y descarga.
Finalmente, la seguridad es primordial. Se debe implementar un protocolo de seguridad que incluya el uso de señales de advertencia, iluminación adecuada y la capacitación del personal en las prácticas de seguridad. La elección de las superficies y los materiales de construcción deben asegurar la durabilidad y resistencia a la carga.
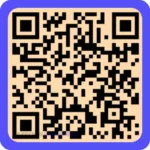
Recepción y Control: El Primer Paso en la Cadena de Suministro
Etapa | Descripción y Métricas Clave |
---|---|
Verificación de la Entrega | Comprobación de la cantidad de unidades recibidas contra la orden de compra (PO). Cálculo del porcentaje de cumplimiento de la PO. Identificación de cualquier daño o faltante en el embalaje. Registro del tiempo de descarga. Métrica: Tasa de precisión de la recepción (98%). |
Inspección de Calidad | Evaluación de la calidad de los productos recibidos según los estándares preestablecidos. Prueba de funcionalidad y características clave. Documentación de cualquier defecto o no conformidad. Generación de un informe de inspección. Métrica: Tasa de rechazo (2%). |
Registro y Entrada de Datos | Introducción de los datos de la recepción en el sistema de gestión de inventario (WMS). Actualización del stock disponible. Generación de etiquetas de identificación de los productos. Asignación de ubicación de almacenamiento. Métrica: Tiempo promedio de entrada de datos (5 minutos por envío). |
Almacenamiento | Ubicación adecuada del inventario recibido según criterios predefinidos (FIFO, FEFO). Mantenimiento del orden y la organización del almacén. Control de temperatura y humedad si es necesario. Métrica: Tasa de rotación de inventario (5 veces al año). |
La recepción y control de mercancías es un proceso fundamental en la gestión de un almacén. Aquí se verifica la calidad y la cantidad de los productos recibidos. Esta zona debe estar organizada para facilitar la inspección, el escaneo y el registro de cada artículo. Un sistema de gestión de almacenes (WMS) es esencial para automatizar este proceso.
La zona de recepción debe contar con espacio suficiente para la descarga y el desembalaje de las mercancías. Además, es necesario tener un área para la inspección de los productos, donde se comprueban las cantidades y el estado de los productos. Se utiliza tecnología de escaneo de códigos de barras o RFID para registrar los productos y actualizar el inventario. Se realiza la verificación documental para asegurar la correspondencia entre la mercancía y los documentos de envío.
La correcta gestión de esta área implica la creación de un procedimiento detallado que incluya la documentación necesaria, la asignación de personal y las herramientas necesarias para la tarea. Un buen proceso implica tener sistemas de pesaje y medición para verificar las cantidades, y software para registrar los datos e integrar con el WMS. El mantenimiento de un registro completo y preciso facilita la gestión del inventario y la trazabilidad de los productos.
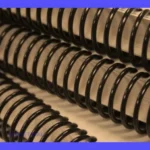
Por último, la integración del sistema de recepción con el resto de las zonas de un almacén es crucial para un flujo eficiente de mercancías. Esta zona es el primer paso en el proceso logístico del almacén, su eficiente organización es esencial para el resto de las operaciones. Una recepción bien organizada optimiza el tiempo y los recursos.
El Almacenaje: Optimizando el Espacio y la Gestión del Inventario
Método de Optimización | Resultados Obtenidos |
---|---|
Implementación de un sistema de gestión de inventario (WMS) | Reducción del 15% en el tiempo de búsqueda de productos y un 10% en errores de inventario en el primer trimestre de 2023. |
Utilización de estanterías de alta densidad | Aumento del 20% en la capacidad de almacenamiento en el almacén principal, completado en junio de 2022. |
Formación del personal en técnicas de organización y gestión de espacio | Mejora del 8% en la eficiencia del picking y del 5% en la reducción de daños en productos durante el año 2023. |
Optimización del layout del almacén mediante análisis de flujo de materiales | Reducción del 12% en el tiempo de recorrido de los operarios en el proceso de picking, implementado en septiembre de 2022. |
Implementación de un sistema de etiquetado y codificación mejorado | Disminución del 7% en los errores de ubicación y un 5% en devoluciones por errores de envío desde julio de 2023. |
El área de almacenaje es el corazón de cualquier zona de almacen, donde se guarda la mercancía. La optimización de este espacio es crucial para la eficiencia. Se debe considerar la altura del techo, la disposición de los racks, y la categorización de la mercancía para facilitar su acceso y recuperación. El uso de sistemas de almacenamiento adecuados, como racks selectivos, racks de doble profundidad, o racks cantilever, depende del tipo de mercancía y su frecuencia de acceso.
La ubicación de los productos es fundamental. La ubicación estratégica de los productos de mayor rotación cerca de las zonas de picking optimiza la preparación de pedidos. El sistema de ubicación puede basarse en el método FIFO (First In, First Out) o LIFO (Last In, First Out), dependiendo de la caducidad de los productos. Se pueden utilizar códigos de barras o RFID para facilitar la localización de la mercancía.
La optimización del espacio del almacén implica un análisis exhaustivo de las necesidades de almacenaje. Se requiere calcular el volumen de mercancía a almacenar, la frecuencia de acceso y la rotación de inventario. Es necesario tomar en cuenta la variedad de productos y sus dimensiones, para elegir el tipo de rack más adecuado y optimizar el espacio disponible.
Además, la seguridad dentro del área de almacen es primordial. Se deben mantener los pasillos despejados para permitir la circulación segura de las carretillas elevadoras y del personal. Se deben implementar medidas de prevención contra incendios y otros riesgos. Es importante una adecuada organización y gestión del espacio para evitar accidentes y optimizar el acceso a la mercancía.
Preparación de Pedidos: Agilidad y Precisión en la Recolección
La preparación de pedidos es una zona crítica en las áreas de un almacen. La eficiencia en esta área impacta directamente en la satisfacción del cliente y la velocidad de entrega. Se deben implementar métodos de picking óptimos, como picking por lotes, picking por zonas, o picking por voz. La elección depende del tamaño del pedido, la complejidad del producto, y el volumen de pedidos diarios.
La organización de este área incluye la optimización del recorrido de los operarios, la ubicación estratégica de los productos, y la utilización de tecnología para mejorar la precisión y la velocidad de la recolección. Sistemas de gestión de almacenes (WMS) guían a los operarios por rutas óptimas. Sistemas de escaneo de códigos de barras o RFID verifican la precisión del picking.
El uso de sistemas de ayuda a la preparación de pedidos, como dispositivos de mano con lectores de códigos de barras, optimiza la recolección de la mercancía. La implementación de un sistema de gestión de almacenes (WMS) es fundamental para gestionar las órdenes de manera eficiente. El WMS integra los procesos de recepción, almacenaje y preparación de pedidos.
La capacitación del personal es fundamental para la eficiencia de esta área. Los operarios deben ser entrenados en los procedimientos de picking, en el uso de los equipos, y en la importancia de la precisión en el proceso. La implementación de controles de calidad asegura la correcta selección de productos y minimiza los errores.
Expedición: El Envío Eficiente de la Mercancía
La zona de expedición es el último paso del proceso logístico del almacén. Esta área debe estar optimizada para agilizar el envío de la mercancía al cliente. Aquí se verifica la información del pedido, se embala la mercancía, y se prepara para el envío mediante la empresa de mensajería o transporte elegida. Es fundamental implementar un sistema eficiente de gestión de envíos, incluyendo el seguimiento de los paquetes y la generación de etiquetas de envío.
La optimización de esta zona implica la implementación de procedimientos que minimicen los tiempos de espera y los posibles errores. La disposición de la zona debe facilitar el acceso a las mercancias preparadas y el transporte hasta los camiones o servicios de mensajería. Las herramientas y equipamientos deben estar organizados para el embalado eficiente y seguro de los productos.
La integración con las zonas de un almacén anteriores, como la preparación de pedidos y el almacenaje, es crucial para asegurar una gestión eficiente del proceso global. El uso de sistemas de gestión de transportes (TMS) puede ser de gran ayuda para controlar los envíos, optimizar las rutas y generar informes. Es fundamental asegurar el seguimiento y la trazabilidad de los envíos.
La gestión de las salidas de la mercancía debe llevarse a cabo con precisión, garantizando que se cumplan los plazos de entrega establecidos y la seguridad del transporte. Un control riguroso de los documentos de envío y la confirmación de la entrega por parte del cliente son aspectos clave de la gestión eficiente de la expedición. Una buena comunicación con los transportistas es también vital para asegurar un proceso expedito y sin contratiempos.
Oficinas y Servicios: El Soporte Administrativo del Almacén
Las zonas de un almacén deben incluir un área dedicada a las oficinas y servicios, esencial para el soporte administrativo del almacén. Este espacio permite el trabajo eficiente de los empleados administrativos, quienes gestionan los pedidos, el inventario, y los diferentes aspectos administrativos. Esta área requiere espacios para ordenadores, escritorios, espacio de archivado, y todo aquello necesario para una gestión eficiente del almacén.
Se recomienda que esta zona se encuentre en un lugar accesible y estratégicamente ubicado dentro del almacén, facilitando la comunicación con las demás áreas. Debe contar con la tecnología e infraestructura necesaria para realizar el trabajo administrativo de manera eficiente. Una buena iluminación, comodidad y espacios de trabajo adecuados son cruciales para la productividad de los empleados.
La implementación de un sistema de gestión de almacenes (WMS) simplifica las tareas administrativas, integrando datos de las distintas áreas. La seguridad en las oficinas es clave, implementando sistemas de control de acceso y de protección de datos. Debe garantizarse un ambiente de trabajo cómodo y eficiente para el personal administrativo.
Además, debe considerarse un área de descanso para los empleados, con instalaciones sanitarias y un lugar para comer o tomar descansos. Este área de descanso es fundamental para el bienestar de los empleados, mejorando su productividad y moral. Un ambiente de trabajo agradable contribuye a la eficiencia global del almacén.
Mantenimiento: Garantizando la Operatividad
El mantenimiento preventivo y correctivo de las instalaciones y equipos es fundamental para la operatividad del almacén. Esta área implica la gestión de las reparaciones y la programación del mantenimiento de los equipos, como carretillas elevadoras, sistemas de almacenamiento, y sistemas de gestión. Un adecuado mantenimiento previene problemas mayores y prolonga la vida útil de los equipos, optimizando el rendimiento.
Esta área debe tener un espacio designado para guardar herramientas y repuestos. Se debe crear un registro de mantenimiento para realizar un seguimiento de las actividades y programar las tareas preventivas. La capacitación del personal en el mantenimiento básico de los equipos es crucial para reducir el tiempo de inactividad.
Es fundamental establecer un programa de mantenimiento preventivo que incluya inspecciones regulares y limpieza de los equipos, así como la reparación de cualquier daño o mal funcionamiento. Un buen programa de mantenimiento incluye el control de inventario de repuestos y la gestión de contratos de mantenimiento con proveedores externos, si es necesario.
La seguridad dentro de las zonas de un almacén dedicadas al mantenimiento debe ser prioritaria, utilizando los equipos de protección individual necesarios y siguiendo los protocolos de seguridad. La optimización del mantenimiento impacta directamente en la productividad y minimiza los tiempos de inactividad.
Devoluciones: Gestión Eficiente de la Mercancía Retornada
La gestión de devoluciones es un aspecto esencial en el funcionamiento de un almacén. Esta zona debe estar diseñada para facilitar el proceso de recepción, inspección y re-almacenaje de la mercancía devuelta. Un proceso eficiente de devoluciones ayuda a optimizar el stock, reducir costos y mejorar la satisfacción del cliente.
Esta zona debe contar con un procedimiento claro y definido para el registro, la inspección y el procesamiento de la mercancía devuelta. Se necesita espacio suficiente para el almacenamiento temporal de los artículos devueltos, mientras se realiza la inspección de su estado. Se debe contar con personal capacitado para gestionar el proceso y tomar decisiones sobre la mercancía devuelta (re-almacenamiento, reparación, desecho).
La documentación precisa es fundamental. Se debe mantener un registro detallado de cada devolución, incluyendo la información del cliente, la fecha de devolución, el motivo de la devolución y el estado del artículo. El uso de un sistema informático puede facilitar la gestión de este proceso.
Para optimizar esta área, se puede implementar un sistema de control de calidad que ayude a identificar las causas de las devoluciones y reducir su frecuencia. Se puede considerar un área específica para la reparación de los productos devueltos, en caso de que sea posible. La integración del sistema de devoluciones con el WMS facilita la gestión del inventario.
Reenvasado: Adaptando el Embalaje a las Necesidades
En muchos almacenes, especialmente en el sector del comercio electrónico, existe la necesidad de un área de reenvasado. Aquí, los productos se vuelven a empaquetar para adaptarse a las necesidades específicas de cada pedido. Se puede necesitar cambiar el tamaño del embalaje, añadir protecciones adicionales, o personalizar el envoltorio.
Esta área debe contar con los materiales necesarios, como cajas, rellenos protectores, cinta adhesiva y otros materiales de embalaje. Un diseño eficiente de esta zona facilita el flujo de trabajo y la optimización del tiempo de reenvasado. Las herramientas y materiales deben estar organizados y fácilmente accesibles.
La capacitación del personal en las técnicas de embalado es fundamental para asegurar la protección del producto durante el transporte. Se deben utilizar técnicas de embalaje adecuadas para evitar daños durante el envío. La gestión eficiente de los materiales de embalaje minimiza los costos y reduce el desperdicio.
Además, la eficiencia en el reenvasado reduce el tiempo de preparación de pedidos y optimiza el proceso logístico. Un sistema de seguimiento de los materiales de embalaje permite controlar los inventarios y gestionar los pedidos de nuevos materiales. La integración de esta área con el sistema de gestión de almacenes optimiza la gestión del proceso completo.
Cuarentena: Almacenamiento Temporal de Productos
Finalmente, algunas zonas de un almacén deben incluir un área de cuarentena. Este espacio está reservado para el almacenamiento temporal de productos que requieren una inspección adicional, ya sea por cuestiones de calidad, daños o por estar sujetos a regulaciones específicas. Esta área está separada del resto del almacén para prevenir la contaminación cruzada o el acceso no autorizado.
Esta área debe estar claramente señalizada y de fácil acceso para el personal autorizado. Se debe llevar un registro detallado de los productos en cuarentena, incluyendo las razones de su almacenamiento en esta zona y la fecha de su llegada. Se debe contar con un procedimiento definido para su inspección y posterior procesamiento.
Una vez que se realiza la inspección y se verifica que el producto cumple con las especificaciones, se trasladará a la zona de almacenaje correspondiente. En caso contrario, se tomará la decisión correspondiente, según la naturaleza del problema detectado (desecho, reparación, etc.). La gestión adecuada de esta zona previene la contaminación y asegura la calidad de los productos.
El control de acceso y la seguridad son fundamentales en esta zona. Solo el personal autorizado puede acceder a este área, lo que protege la integridad del producto y previene cualquier riesgo de contaminación o daños. Un control estricto de entradas y salidas garantiza la transparencia en el manejo de los productos en cuarentena.
Conclusión
El diseño eficiente de un almacén requiere una planificación cuidadosa de las diferentes zonas de un almacén. Cada área juega un papel crucial en la optimización del flujo de trabajo y la eficiencia global de las operaciones. Desde las zonas de carga hasta el área de cuarentena, cada espacio debe estar optimizado para facilitar el proceso logístico. El uso de sistemas de gestión de almacenes (WMS) y otras tecnologías es esencial para la automatización y el control de las operaciones. Una planificación exhaustiva considerando el tipo de mercancía, el volumen de trabajo y las necesidades específicas de la empresa garantiza la creación de un almacén eficiente, productivo y rentable. Recordar la importancia de la optimización de las áreas de almacen es clave para el éxito de cualquier negocio.
La correcta distribución y gestión de las zonas de un almacén impactan directamente en la productividad, la rentabilidad y la satisfacción del cliente. Una adecuada planificación, la implementación de tecnología y la capacitación del personal son factores cruciales para optimizar el funcionamiento del almacén en su totalidad. Optimizar las zonas de almacen implica una inversión a largo plazo que se traduce en eficiencia y crecimiento.
Preguntas Frecuentes
¿Cuál es la importancia de la correcta distribución de las zonas de un almacén?
La correcta distribución de las zonas de un almacén impacta directamente en la eficiencia, productividad y rentabilidad del negocio.
¿Qué tecnología se puede implementar para optimizar las áreas de un almacén?
Los sistemas WMS, lectores de códigos de barras, RFID y software de gestión de transporte son ejemplos de tecnología que optimiza las áreas de un almacén.
¿Cómo afecta el tamaño del almacén a la distribución de sus zonas?
El tamaño del almacén influye directamente en la distribución de sus zonas, determinando el espacio disponible para cada área.
¿Qué factores debo considerar al diseñar las zonas de un almacén?
Considere el tipo de mercancía, volumen de operaciones, flujo de trabajo, equipo a utilizar, y la seguridad al diseñar las zonas de un almacén.
¿Es necesario contratar a un especialista para diseñar las zonas de un almacén?
Contratar a un especialista en logística y diseño de almacenes asegura un diseño eficiente y optimizado para las necesidades específicas del negocio.
Deja una respuesta
Te Puede Interesar: