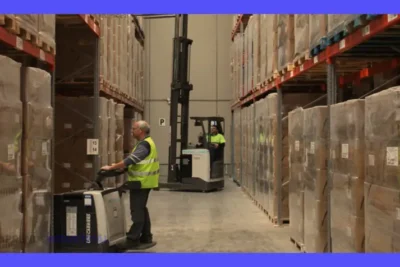
Picking por zonas: Guía para optimizar la preparación de pedidos
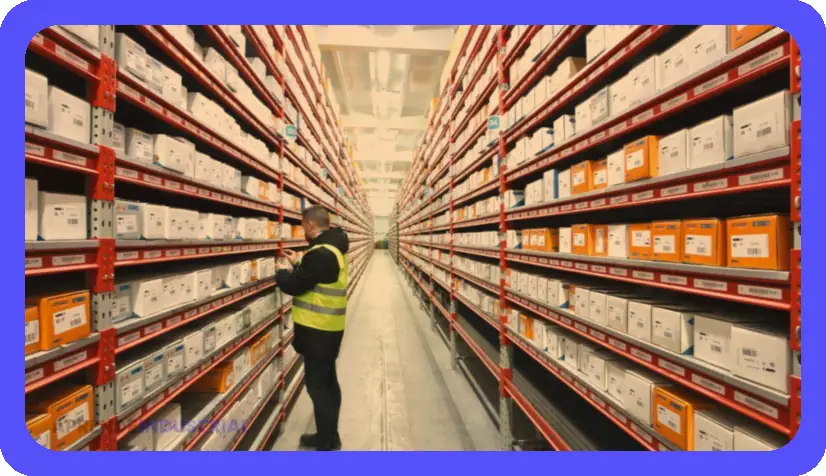
La optimización de los procesos de almacén es crucial para la eficiencia de cualquier negocio que maneje inventario. Una estrategia clave para lograrlo es la implementación de sistemas de picking por zonas. Este método consiste en dividir el almacén en secciones o zonas dedicadas a la preparación de pedidos, asignando a cada zona un operario o un grupo de operarios. Esto permite una recolección más eficiente y rápida del material, minimizando los desplazamientos innecesarios y, por lo tanto, reduciendo los tiempos de preparación de pedidos.
Este artículo explorará en detalle los aspectos clave de la implementación de zonas de picking en un almacén. Analizaremos las diferentes metodologías, las ventajas y desventajas, los requisitos tecnológicos, y los factores cruciales para una implementación exitosa. Además, proporcionaremos ejemplos prácticos y consejos útiles para que puedas aplicar este método en tu propio almacén y optimizar tus operaciones. Aprenderás cómo la correcta planificación y organización de las zonas de picking pueden transformar la eficiencia de tu proceso de picking.
- Tipos de Picking por Zonas: Secuencial vs. Simultáneo
- Diseño y Zonificación del Almacén para Picking por Zonas
- Software de Gestión de Almacén (SGA) para Picking por Zonas
- Métricas de Rendimiento y Optimización Continua
- Capacitación del Personal y Gestión del Cambio
- Ventajas y Desventajas del Picking por Zonas
- Ejemplos de Implementación de Picking por Zonas
- Consideraciones Finales para la Implementación Exitosa
- Conclusión
- Preguntas Frecuentes
Tipos de Picking por Zonas: Secuencial vs. Simultáneo
Característica | Picking Secuencial | Picking Simultáneo |
---|---|---|
Método de Recolección | El recolector visita cada zona de picking en un orden predefinido, recolectando todos los artículos de una zona antes de pasar a la siguiente. | Varios recolectores trabajan simultáneamente, cada uno responsable de una zona específica. |
Eficiencia | Menos eficiente para pedidos con artículos dispersos en múltiples zonas. Mayor tiempo de viaje. | Mayor eficiencia para pedidos con artículos dispersos. Menor tiempo de viaje total, pero puede requerir más organización y coordinación. |
Costo | Costo de mano de obra generalmente menor, requiere menos personal. | Costo de mano de obra generalmente mayor, requiere más personal y gestión de equipo. |
Complejidad | Menos complejo de implementar y gestionar. | Más complejo de implementar y gestionar; requiere una planificación y coordinación cuidadosa. |
Adecuado para | Pedidos con artículos concentrados en pocas zonas, almacenes pequeños o con baja densidad de artículos. | Pedidos con artículos dispersos en múltiples zonas, almacenes grandes o con alta densidad de artículos, alto volumen de pedidos. |
Ejemplo | Un recolector que recoge todos los artículos de la zona A, luego todos los de la zona B, y así sucesivamente. | Tres recolectores, cada uno recogiendo artículos de una zona diferente (A, B, C) simultáneamente. |
Existen dos métodos principales de picking por zonas: el secuencial (pick and pass) y el simultáneo (pick and merge). En el pick and pass, cada operario trabaja en una zona específica y pasa el pedido a la siguiente zona para que otro operario continúe con la preparación. Esto es ideal para almacenes con un volumen de pedidos moderado. Por ejemplo, un almacén de artículos voluminosos donde cada zona se especializa en un tipo de producto.
Por otro lado, el pick and merge implica que cada operario recolecta artículos de múltiples pedidos simultáneamente en su zona. Al final de la preparación, los pedidos se consolidan. Esta estrategia resulta más eficiente en almacenes con alto volumen de pedidos, donde el tiempo de preparación es crucial. Imaginemos un almacén de comercio electrónico, donde cada zona se especializa en una categoría de producto y los operarios preparan partes de varios pedidos a la vez. La elección entre pick and pass y pick and merge dependerá del volumen de pedidos y la configuración del almacén. Un buen análisis de tus operaciones te ayudará a determinar el método más adecuado. La flexibilidad en el manejo de las zonas de picking es un factor a considerar en la elección del mejor método.
El sistema de zonas de picking mejora la eficiencia de los operarios y reduce el tiempo total de preparación. La organización de estas zonas influye significativamente en la eficacia del sistema.
Diseño y Zonificación del Almacén para Picking por Zonas
Zona | Características y Productos |
---|---|
Zona A: Artículos de alta rotación | Ubicación cercana a la zona de expedición. Almacenamiento en estanterías de fácil acceso. Productos: artículos de limpieza, papelería básica, componentes electrónicos de alta demanda. Sistema FIFO implementado. |
Zona B: Artículos de rotación media | Ubicación intermedia. Almacenamiento en estanterías de altura media. Productos: material de oficina especializado, herramientas, repuestos de maquinaria. Sistema FIFO y LIFO combinados. |
Zona C: Artículos de baja rotación | Ubicación alejada de la zona de expedición. Almacenamiento en estanterías de gran altura o paletización. Productos: materiales de archivo, repuestos de maquinaria obsoleta, herramientas de uso ocasional. Sistema LIFO. |
Zona D: Artículos de gran tamaño/volumen | Ubicación con acceso para carretillas elevadoras. Almacenamiento en racks selectivos para paletas. Productos: maquinaria pesada, mobiliario de oficina, materiales de construcción. Sistema LIFO. |
Zona E: Productos de temporada | Ubicación adaptable según la época del año. Almacenamiento en estanterías móviles. Productos: artículos navideños, artículos de verano (piscinas, etc). Sistema FIFO. |
El diseño y la zonificación del almacén son fundamentales para el éxito del picking por zonas. Un diseño deficiente puede anular las ventajas del método. Se debe considerar la frecuencia de picking de cada producto, el tamaño y peso de los artículos, y las características del flujo de trabajo. Una buena práctica es agrupar productos de alta demanda en zonas de fácil acceso y con mayor cantidad de personal, mientras que los productos de baja demanda pueden ubicarse en zonas más alejadas.
La optimización del slotting, es decir, la ubicación de los productos dentro del almacén, es clave. Esto implica usar algoritmos que consideren la frecuencia de acceso, el tamaño, y la demanda para asignar ubicaciones óptimas a cada producto dentro de cada zona. Una correcta zonificación garantiza que los operarios recorran la menor distancia posible al recoger los artículos, maximizando su productividad. La planificación cuidadosa de las zonas de picking puede reducir los costos de operación.
Además, es importante considerar el tamaño y la forma de las zonas. Zonas demasiado grandes pueden resultar en desplazamientos innecesarios, mientras que zonas demasiado pequeñas pueden limitar la capacidad de los operarios. Se debe buscar un equilibrio que optimice la productividad sin generar congestión o ineficiencias. Un diseño adecuado de las zonas de picking implica prever espacio para el movimiento de operarios y material, minimizando los atascos y conflictos.
La implementación del picking por zonas exige una cuidadosa planificación del layout del almacén. Considerar la ergonomía para el bienestar de los operarios es un factor vital en esta etapa.
Software de Gestión de Almacén (SGA) para Picking por Zonas
Software | Características Clave para Picking por Zonas |
---|---|
NetSuite Warehouse Management | Optimización de rutas de picking, asignación dinámica de zonas, gestión de múltiples ubicaciones, integración con otros sistemas ERP, análisis de rendimiento en tiempo real, capacidad para gestionar diferentes métodos de picking (wave picking, batch picking, zone picking). |
Fishbowl Inventory | Asignación de zonas de picking, seguimiento de inventario en tiempo real, gestión de lotes y seriales, integración con Shopify y otras plataformas de comercio electrónico, informes personalizados para el análisis del rendimiento del picking. |
SAP EWM (Extended Warehouse Management) | Gestión avanzada de almacenes, optimización de rutas de picking con algoritmos inteligentes, control de acceso a zonas, integración con otros sistemas SAP, gestión de múltiples flujos de trabajo, análisis predictivos para la optimización de la planificación. |
Infor WMS | Asignación flexible de zonas, gestión de olas de picking, seguimiento de rendimiento de los operarios, integración con otros sistemas de Infor, adaptabilidad a diferentes tipos de almacenes y procesos de picking. |
La implementación eficiente del picking por zonas requiere un software de gestión de almacén (SGA) robusto. El SGA es esencial para coordinar las operaciones, asignar pedidos a las zonas correspondientes, optimizar el slotting, y automatizar la gestión de ubicaciones. Un buen SGA permitirá el seguimiento en tiempo real de la preparación de pedidos, detectando cuellos de botella y optimizando los recursos.
El SGA debe ser capaz de generar rutas de picking óptimas para cada operario dentro de su zona, minimizando los desplazamientos y maximizando la eficiencia. Además, un sistema de gestión de inventario integrado es esencial para garantizar la precisión de los datos y evitar errores en la preparación de pedidos. La correcta integración de la información permite un mejor control de las zonas de picking.
La funcionalidad del SGA debe permitir la generación de informes que muestren la productividad de cada zona y de cada operario. Esta información es crucial para identificar áreas de mejora y optimizar la estrategia de picking por zonas. La selección adecuada del SGA es vital para obtener los beneficios esperados de la implementación de este método. El software se convierte en un pilar fundamental para la optimización del picking por zonas.
Un SGA bien implementado es esencial para el éxito de las zonas de picking y la eficiencia del almacén.
Métricas de Rendimiento y Optimización Continua
Para evaluar la efectividad del picking por zonas, es necesario monitorear ciertas métricas de rendimiento. Algunas métricas importantes incluyen el tiempo de picking por pedido, la precisión del picking, la distancia recorrida por operario, y la productividad por operario. El seguimiento de estas métricas proporciona información valiosa para identificar áreas de mejora y optimizar la eficiencia del sistema.
El análisis de estas métricas permite evaluar el impacto del sistema de zonas de picking en la productividad del almacén. Por ejemplo, si el tiempo de picking aumenta a pesar de la implementación del sistema, se debe analizar la causa raíz para realizar los ajustes necesarios, ya sea optimizando las zonas o mejorando la formación de los empleados. La optimización del sistema de picking por zonas es un proceso continuo.
Además, es importante analizar la satisfacción de los empleados. Un sistema de zonas de picking mal implementado puede generar estrés y frustración en los operarios, lo que impacta negativamente en su productividad. Obtener retroalimentación de los empleados permite identificar problemas y realizar los ajustes necesarios para mejorar la ergonomía y el flujo de trabajo. Un sistema eficiente mejora la moral de los empleados.
La optimización del sistema de picking por zonas es un proceso iterativo que requiere monitoreo constante y ajustes según sea necesario.
Capacitación del Personal y Gestión del Cambio
La implementación exitosa de zonas de picking requiere una adecuada capacitación del personal. Los operarios deben ser instruidos en los procedimientos de trabajo, en el uso del SGA, y en la importancia de la precisión en la preparación de pedidos. La capacitación debe incluir la comprensión del sistema de zonas, las rutas óptimas, y los métodos de manejo de materiales.
Un programa de capacitación efectivo asegura que los empleados entiendan y adopten la metodología correctamente, minimizando los errores y maximizando la eficiencia. La gestión del cambio también es crucial. Los empleados deben estar preparados para la transición a un nuevo sistema de trabajo. La comunicación abierta y la participación de los empleados en el proceso de implementación son clave para garantizar su aceptación y colaboración.
La formación de los empleados en la utilización del SGA y en los procedimientos de trabajo optimiza la eficiencia del sistema. Un cambio bien gestionado aumenta la probabilidad de un resultado positivo en la implementación del sistema de zonas de picking.
Ventajas y Desventajas del Picking por Zonas
El picking por zonas ofrece numerosas ventajas, entre ellas la reducción de los tiempos de preparación de pedidos, la mejora de la precisión en el picking, y el aumento de la productividad. Además, ayuda a minimizar los desplazamientos de los operarios, lo que reduce la fatiga y aumenta la eficiencia. La especialización de los operarios en zonas específicas también puede mejorar su experiencia y rapidez.
Sin embargo, también existen algunas desventajas. La implementación puede requerir una inversión inicial significativa en software y hardware. Además, la necesidad de un SGA eficaz puede incrementar los costos operativos. La implementación también puede requerir un cambio en la organización del trabajo, lo que puede generar resistencia por parte de los empleados si no se gestiona adecuadamente el cambio.
El balance entre los beneficios y los costos de la implementación del sistema de zonas de picking se debe considerar cuidadosamente. Las ventajas superan a las desventajas en muchos casos, especialmente en almacenes con alto volumen de pedidos.
Ejemplos de Implementación de Picking por Zonas
Imaginemos un almacén de una tienda online de ropa. Se podría dividir el almacén en zonas por tipo de prenda: tops, pantalones, vestidos, etc. Cada zona contaría con un operario encargado de recoger los artículos de los pedidos asignados a esa zona. Este enfoque permite una especialización del personal y un manejo eficiente de las diferentes prendas.
Consideremos otro ejemplo, un almacén de repuestos de automóvil. Las zonas podrían dividirse por marca, tipo de vehículo o tipo de repuesto. Este sistema permite una ubicación lógica y un acceso rápido a los artículos requeridos. La asignación de artículos y el diseño de las zonas de picking son cruciales para el éxito de la estrategia.
Estos ejemplos ilustran la flexibilidad del sistema de picking por zonas. La implementación específica dependerá de la configuración del almacén y del tipo de artículos gestionados.
Consideraciones Finales para la Implementación Exitosa
Para una implementación exitosa, es fundamental realizar un análisis exhaustivo de las necesidades del almacén, incluyendo el volumen de pedidos, el tipo de productos, y el espacio disponible. Este análisis informará las decisiones sobre el diseño de las zonas, la selección del SGA, y la capacitación del personal. La planificación cuidadosa es crucial.
Es vital considerar las implicaciones de la implementación en los procesos existentes. Una gestión del cambio efectiva asegurará una transición suave y minimizará las interrupciones. La comunicación con los empleados es esencial para obtener su apoyo y colaboración. La flexibilidad en el ajuste del sistema de zonas de picking es una ventaja.
La monitorización continua de las métricas clave es crucial para identificar áreas de mejora y optimizar el sistema a lo largo del tiempo. La implementación del picking por zonas es una inversión que, si se gestiona bien, generará un retorno significativo en términos de eficiencia y productividad.
Conclusión
La implementación de un sistema de picking por zonas representa una estrategia poderosa para optimizar la preparación de pedidos en un almacén. Este método, que puede ser secuencial o simultáneo, ofrece ventajas significativas en términos de eficiencia, precisión, y reducción de costos. Sin embargo, un diseño y una implementación cuidadosos, junto con la selección del SGA adecuado y la capacitación del personal, son cruciales para cosechar los beneficios de este sistema. El análisis continuo de las métricas de rendimiento permite la optimización continua y la adaptación a las necesidades cambiantes del almacén. El éxito del picking por zonas reside en una planificación exhaustiva, una ejecución eficiente y un compromiso con la mejora continua.
Preguntas Frecuentes
¿Qué es el picking por zonas?
Es una estrategia de preparación de pedidos que divide el almacén en áreas para asignar a operarios, optimizando el proceso.
¿Qué tipo de software se necesita para el picking por zonas?
Se requiere un Software de Gestión de Almacén (SGA) capaz de coordinar las operaciones y optimizar el slotting.
¿Cuáles son las principales ventajas del picking por zonas?
Reduce tiempos de preparación, aumenta la precisión y optimiza los desplazamientos de los operarios.
Deja una respuesta
Te Puede Interesar: