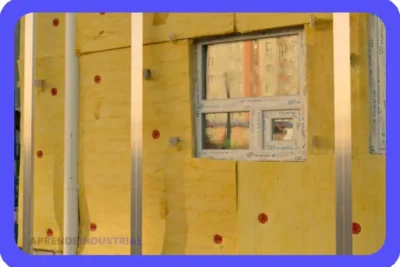
Tipos de Fallas en Maquinaria y Sistemas: Guía Completa
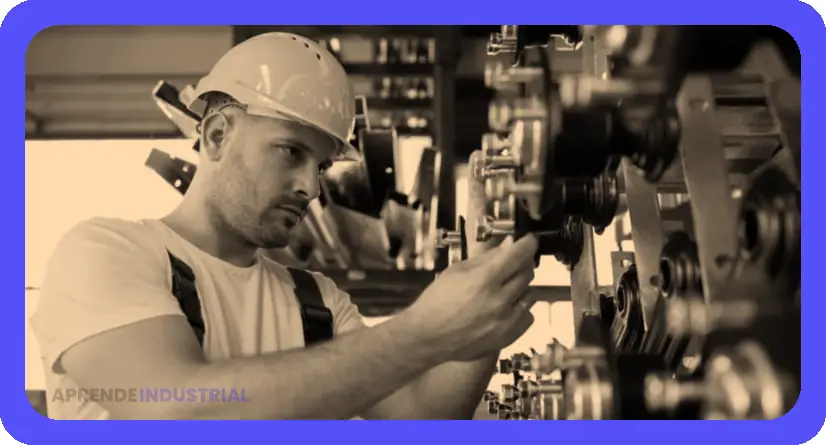
El mantenimiento industrial es crucial para la eficiencia y seguridad de cualquier operación. Un componente fundamental de un programa de mantenimiento eficaz es el estudio de fallas en maquinaria y sistemas. Comprender las causas raíz de las averías permite a las empresas optimizar sus procesos, reducir costos de reparación, mejorar la seguridad de los empleados y, en última instancia, aumentar la productividad. Las fallas en los equipos pueden interrumpir la producción, generar pérdidas económicas significativas e incluso causar accidentes graves. Por lo tanto, el análisis exhaustivo de estas tipos de fallas en maquinaria y sistemas es esencial para la competitividad y el éxito a largo plazo.
Este artículo explorará en detalle los aspectos clave del estudio de fallas en maquinaria y sistemas. Analizaremos diferentes tipos de fallas, sus causas, métodos de detección y las mejores prácticas para prevenirlas. Aprenderemos a identificar patrones, analizar datos y aplicar estrategias de mantenimiento predictivo para minimizar el impacto de las fallas. A través de ejemplos prácticos, ilustraremos cómo un enfoque sistemático para el análisis de fallas puede contribuir a un mantenimiento industrial más eficiente y seguro.
- Identificación de los Tipos de Fallas
- Análisis de Causas Raíces de las Fallas
- Prevención de Fallas: Mantenimiento Preventivo
- Mantenimiento Predictivo: Monitoreo y Diagnóstico
- Implementación de un Programa de Análisis de Fallas
- Ejemplos de Estudios de Fallas en la Industria
- El Impacto de las Fallas en la Productividad
- Conclusión
- Preguntas Frecuentes
Identificación de los Tipos de Fallas
Tipo de Falla | Descripción | Ejemplos |
---|---|---|
Falla por tensión | Fractura de un material debido a esfuerzos de tracción que superan su resistencia a la tensión. | Rotura de un cable de acero por sobrecarga, fractura de un componente cerámico sometido a tracción. |
Falla por compresión | Fractura de un material debido a esfuerzos de compresión que superan su resistencia a la compresión. A menudo implica aplastamiento o pandeo. | Aplastamiento de una columna de hormigón, pandeo de una viga metálica delgada. |
Falla por fatiga | Fractura de un material debido a la aplicación repetida de cargas cíclicas, incluso si las cargas individuales son inferiores a la resistencia estática del material. | Fractura de un eje de transmisión por vibraciones repetidas, grietas en una estructura metálica sometida a cargas de flexión cíclicas. |
Falla por fluencia | Deformación permanente de un material bajo una carga constante aplicada durante un período prolongado de tiempo. | Deformación lenta de un puente metálico bajo su propio peso, deformación de una tubería sometida a alta presión durante años. |
Falla por impacto | Fractura de un material debido a una carga de impacto repentina y de alta energía. | Rotura de un parabrisas por impacto de una piedra, daño en una estructura por un impacto de un objeto pesado. |
Falla por corrosión | Degradación de un material debido a una reacción química con su entorno. | Oxidación de una tubería de acero, corrosión de un componente metálico en un ambiente húmedo. |
El primer paso para mejorar el mantenimiento industrial es identificar con precisión los tipos de fallas en maquinaria y sistemas. Las fallas pueden clasificarse en varias categorías, incluyendo fallas mecánicas, eléctricas, de proceso, de calidad y humanas. Las fallas mecánicas involucran componentes físicos como rodamientos, engranajes o ejes, y pueden ser causadas por desgaste, fatiga, corrosión o mala lubricación. Las fallas eléctricas pueden incluir cortocircuitos, sobrecargas o fallos en los componentes electrónicos. Las fallas de proceso se refieren a problemas en el flujo de trabajo o en la calidad del producto. Las fallas de calidad, por su parte, resultan en productos defectuosos o que no cumplen con las especificaciones. Por último, las fallas humanas son errores cometidos por los operadores o personal de mantenimiento.
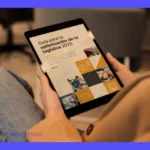
Entender la diferencia entre estos tipos de fallas en maquinaria y sistemas es fundamental para establecer un programa de mantenimiento preciso. Por ejemplo, una falla mecánica recurrente en un determinado componente puede indicar la necesidad de mejorar el diseño o la calidad de los materiales. Mientras tanto, las fallas eléctricas repetidas pueden sugerir problemas en el sistema eléctrico o la necesidad de un mejor mantenimiento preventivo. Una identificación correcta de la causa raíz de la falla evita la repetición del problema.
Las fallas pueden manifestarse de diversas maneras. Algunos problemas son evidentes, como un componente roto, mientras que otros son más sutiles, como una ligera vibración o un aumento en la temperatura de operación. La observación cuidadosa, junto con el uso de instrumentos de monitoreo y diagnóstico, facilita la detección temprana de anomalías. Una detección temprana de los problemas ayuda a prevenir fallas catastróficas y costosas.
Un factor crucial en la identificación de los tipos de fallas en maquinaria y sistemas es la documentación precisa. Se debe mantener un registro detallado de todas las fallas, incluyendo la fecha, hora, ubicación, tipo de falla y las acciones tomadas para corregirla. Esta información es invaluable para el análisis de tendencias y la identificación de patrones de fallas.
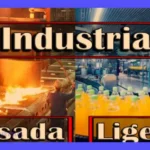
Las investigaciones post-falla deben ser exhaustivas y sistemáticas, siguiendo métodos de análisis de raíz causa.
Análisis de Causas Raíces de las Fallas
Causa Raíz | Descripción de la Falla y Acciones Correctivas |
---|---|
Falta de capacitación del personal | Incumplimiento del procedimiento de seguridad en la operación de la máquina X, resultando en un fallo mecánico el 15/10/2023. Se implementó un programa de entrenamiento adicional para todo el personal, con énfasis en el procedimiento de seguridad mencionado. |
Deficiencia en el mantenimiento preventivo | Fallo en el sistema de refrigeración de la máquina Y el 22/11/2023 debido a la falta de limpieza y lubricación periódica. Se estableció un programa de mantenimiento preventivo más riguroso, incluyendo checklist detallado y monitoreo del estado de la máquina. |
Diseño deficiente del componente Z | Fractura repetida del componente Z en la máquina W a partir del 01/12/2023. Se realizó un rediseño del componente Z con materiales más resistentes y un proceso de fabricación mejorado. El nuevo diseño fue implementado el 15/01/2024 |
Problemas con la calidad de los materiales | Defectos en la materia prima utilizada para la producción del producto A, resultando en un lote defectuoso detectado el 28/02/2024. Se cambió el proveedor de materia prima a uno con un mejor control de calidad y se realizaron pruebas más exhaustivas a la materia prima entrante. |
Una vez identificados los tipos de fallas en maquinaria y sistemas, el siguiente paso es analizar sus causas raíces. Este análisis es crucial para implementar medidas preventivas eficaces y evitar que la falla se repita. El análisis de causa raíz implica la investigación sistemática de los eventos que llevaron a la falla.
Existen diversas metodologías para realizar el análisis de causa raíz, incluyendo el Diagrama de Ishikawa (también conocido como Diagrama de Espina de Pescado), el Análisis de Modo y Efecto de Fallas (AMEF) y el 5 Porqués. Estos métodos ayudan a identificar las causas principales detrás de las fallas, en lugar de centrarse solo en los síntomas.
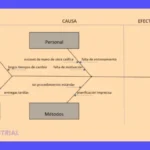
El Diagrama de Ishikawa permite visualizar las diferentes causas potenciales de una falla, organizándolas en categorías como maquinaria, materiales, métodos, mano de obra, medio ambiente y medición. Por ejemplo, una falla en una bomba centrífuga podría tener como causas la falta de lubricación (maquinaria), la corrosión del eje (materiales), un procedimiento de mantenimiento inadecuado (métodos) o errores humanos en la operación (mano de obra).
El AMEF es una herramienta proactiva que se utiliza para identificar posibles fallas antes de que ocurran, permitiendo implementar medidas preventivas para minimizar su impacto. Este método consiste en identificar todos los posibles modos de fallo de un sistema o componente, analizar su severidad, probabilidad de ocurrencia y capacidad de detección, y determinar acciones preventivas.
Por otro lado, el método de los 5 Porqués implica hacer la pregunta "¿Por qué?" repetidamente hasta llegar a la causa raíz del problema. Esta técnica simple, pero efectiva, ayuda a desentrañar la cadena de eventos que condujeron a la falla.
Independientemente del método utilizado, es crucial que el análisis de causa raíz sea exhaustivo, objetivo e involucre a diferentes personas con conocimientos relevantes.
Prevención de Fallas: Mantenimiento Preventivo
Tarea de Mantenimiento | Frecuencia |
---|---|
Inspección visual de correas y poleas | Mensual |
Lubricación de cojinetes y engranajes | Trimestral |
Revisión del sistema de refrigeración (limpieza y llenado) | Semestral |
Cambio de filtros de aire y aceite | Anual |
Inspección completa del sistema eléctrico (cables, conectores, etc.) | Anual |
Calibración de instrumentos de medida | Anual |
Revisión y limpieza del sistema de escape | Anual |
Inspección de seguridad (protecciones, dispositivos de emergencia) | Semestral |
La prevención de fallas es un aspecto crucial del mantenimiento industrial. Para minimizar las interrupciones, los costos y los riesgos, es fundamental establecer un programa de mantenimiento preventivo eficaz. Este programa incluye inspecciones periódicas, lubricación, limpieza y reemplazo de componentes antes de que fallen. En esencia, se trata de anticiparse a los problemas y abordar los riesgos potenciales antes de que se conviertan en fallas costosas.
Un programa efectivo de mantenimiento preventivo comienza con un inventario preciso de todos los equipos. Se deben identificar los componentes clave y su vida útil esperada. A partir de esto, se puede establecer un cronograma de mantenimiento, con intervalos específicos para cada tarea.
Además, la selección adecuada de lubricantes es fundamental para la prevención de fallas. La lubricación adecuada reduce la fricción y el desgaste, aumentando la vida útil de los componentes.
La limpieza regular del equipo también es crucial para prevenir fallas. La acumulación de polvo, suciedad y residuos puede obstruir los componentes, afectar su funcionamiento y provocar fallas prematuras.
Finalmente, la capacitación del personal de mantenimiento es vital. Los empleados deben estar capacitados en los procedimientos de mantenimiento preventivo, en el uso de equipos de diagnóstico y en la resolución de problemas.
Un mantenimiento preventivo bien implementado no solo reduce las fallas, sino que también contribuye a mejorar la seguridad de los empleados y aumentar la eficiencia general de la planta.
La mejora continua es fundamental para lograr el objetivo de minimizar los tipos de fallas en maquinaria y sistemas. Revisar periódicamente el plan de mantenimiento preventivo y actualizarlo en base a la información recogida es esencial.
Mantenimiento Predictivo: Monitoreo y Diagnóstico
El mantenimiento predictivo representa un salto adelante en la optimización del mantenimiento industrial. A diferencia del mantenimiento preventivo, que se basa en intervalos de tiempo predefinidos, el mantenimiento predictivo utiliza técnicas de monitoreo y diagnóstico para detectar posibles fallas antes de que ocurran. De esta manera, se pueden programar las reparaciones de forma oportuna, evitando interrupciones inesperadas.
Las técnicas de monitoreo incluyen la vigilancia de vibraciones, temperatura, presión, corriente eléctrica y otras variables relevantes. Se utilizan sensores para recopilar datos en tiempo real, que son analizados para identificar anomalías. Un aumento en la vibración, por ejemplo, puede indicar un problema inminente en un rodamiento.
El análisis de los datos de monitoreo permite a los profesionales del mantenimiento anticipar las fallas y programar las reparaciones en momentos convenientes. Esto minimiza el tiempo de inactividad y maximiza la eficiencia operativa.
Las técnicas de diagnóstico incluyen el análisis de aceite, termografía y análisis de vibraciones más avanzado. Estas técnicas ayudan a identificar la causa raíz de una anomalía detectada durante el monitoreo. El análisis de aceite, por ejemplo, puede revelar la presencia de partículas metálicas que indican un desgaste excesivo en los componentes.
La implementación del mantenimiento predictivo requiere una inversión inicial en sensores, software de análisis de datos y capacitación del personal. Sin embargo, el retorno de la inversión suele ser significativo, gracias a la reducción de las fallas inesperadas y al aumento de la disponibilidad de los equipos.
Implementación de un Programa de Análisis de Fallas
La implementación de un programa efectivo de análisis de fallas requiere un enfoque sistemático y la colaboración entre diferentes departamentos de la organización. Aquí hay algunos pasos clave a seguir:
- Establecer un equipo multidisciplinario: El equipo debe incluir profesionales de mantenimiento, ingeniería, producción y operaciones.
- Definir objetivos y métricas: Definir qué se quiere lograr con el programa y cómo se medirá el éxito. Se pueden utilizar indicadores clave de rendimiento (KPI) como la tasa de fallas, el tiempo medio entre fallas (MTBF) y el tiempo medio de reparación (MTTR).
- Desarrollar un procedimiento estandarizado: Crear un procedimiento detallado para la recopilación, análisis e informes de fallas.
- Capacitar al personal: Es esencial capacitar al personal en las técnicas de análisis de causa raíz y en el uso de las herramientas de recopilación de datos.
- Implementar un sistema de gestión de datos: Un sistema eficiente para la recopilación, almacenamiento y análisis de datos de fallas es fundamental para el éxito del programa.
- Monitorear y mejorar continuamente: Revisar periódicamente el programa para evaluar su efectividad y realizar los ajustes necesarios.
Un programa exitoso de análisis de fallas contribuirá a la mejora continua del mantenimiento industrial y a la reducción de costos.
Ejemplos de Estudios de Fallas en la Industria
Analicemos algunos ejemplos concretos de tipos de fallas en maquinaria y sistemas y sus análisis:
Falla en un motor eléctrico: Un motor eléctrico de una línea de producción falla repentinamente. El análisis revela sobrecalentamiento debido a una falta de ventilación adecuada. La solución implica mejorar el sistema de refrigeración del motor. Este caso ilustra la importancia de las inspecciones y mantenimiento preventivo.
Falla en una bomba de agua: Una bomba de agua en una planta de proceso presenta una vibración excesiva. El análisis de vibración revela un desbalance en el rotor. Se realiza un balanceo dinámico para corregir el problema. Este ejemplo destaca la utilidad de las técnicas de monitoreo predictivo.
Falla en una cinta transportadora: Una cinta transportadora se rompe debido a un desgaste excesivo en una de sus poleas. El análisis indica una falta de lubricación adecuada. La solución implica establecer un cronograma de lubricación más frecuente. Esto enfatiza la necesidad de un mantenimiento preventivo riguroso.
Estos ejemplos ilustran la importancia del análisis de fallas para identificar las causas raíces y prevenir problemas futuros.
El Impacto de las Fallas en la Productividad
Las fallas en los equipos y maquinaria industrial tienen un impacto significativo en la productividad. Los periodos de inactividad no planificados pueden generar pérdidas económicas considerables, afectando los plazos de entrega, la calidad del producto y la satisfacción del cliente. El tiempo de inactividad puede ser especialmente problemático para las empresas que operan con procesos continuos, donde incluso un breve paro puede tener consecuencias graves.
Además de las pérdidas económicas directas, las fallas también pueden generar costos indirectos significativos. Esto incluye los costos asociados con la reparación, el reemplazo de piezas, la mano de obra y las pérdidas de producción. La falta de una gestión eficiente de las fallas también puede impactar negativamente la reputación de la empresa. Un historial de fallas frecuentes puede dañar la confianza de los clientes y generar problemas con la seguridad.
Para minimizar el impacto de las fallas en la productividad, es crucial invertir en un programa de mantenimiento preventivo y predictivo eficaz. Esto implica la implementación de un sistema eficiente para el seguimiento, análisis y corrección de las fallas. También es importante capacitar al personal en las técnicas de mantenimiento y en la resolución de problemas.
El análisis de los datos de fallas puede proporcionar información valiosa para identificar las causas raíz de los problemas y implementar mejoras en los procesos. Un buen programa de mantenimiento y análisis de fallas permite a las empresas optimizar sus procesos, mejorar la eficiencia y aumentar la rentabilidad.
Conclusión
El estudio de fallas en maquinaria y sistemas es un elemento esencial en el mantenimiento industrial eficiente y seguro. Comprender los tipos de fallas en maquinaria y sistemas, sus causas y las estrategias para prevenirlas es fundamental para reducir el tiempo de inactividad, minimizar los costos y garantizar la seguridad de los trabajadores. A través de la implementación de programas de mantenimiento preventivo y predictivo, junto con un análisis exhaustivo de las causas raíces de las fallas, las empresas pueden optimizar sus operaciones y aumentar su competitividad. La información obtenida del análisis de fallas no solo sirve para corregir problemas presentes, sino que también alimenta la mejora continua en los procesos y la prevención de futuras fallas.
La inversión en un programa de análisis de fallas es una inversión en la mejora de la eficiencia, la seguridad y la rentabilidad de la organización. Un enfoque sistemático y la colaboración entre diferentes equipos son claves para el éxito en la reducción de los tipos de fallas en maquinaria y sistemas.
Preguntas Frecuentes
¿Qué es un análisis de causa raíz?
Es un proceso sistemático para identificar la causa fundamental de un problema, no solo sus síntomas. Permite acciones preventivas efectivas.
¿Cómo puedo mejorar mi programa de mantenimiento?
Implementando mantenimiento preventivo y predictivo, además de un análisis exhaustivo de fallas y la formación adecuada del personal.
¿Cuáles son los beneficios de un programa de análisis de fallas?
Reduce el tiempo de inactividad, costos de reparación, mejora la seguridad y optimiza los procesos industriales.
¿Qué tipos de datos debo recopilar para analizar una falla?
Fecha, hora, tipo de falla, componentes afectados, acciones tomadas para corregirla y las causas potenciales.
¿Existen herramientas software para el análisis de fallas?
Sí, existen muchos programas de gestión de mantenimiento (CMMS) que facilitan este proceso y el análisis de datos.
Deja una respuesta
Te Puede Interesar: