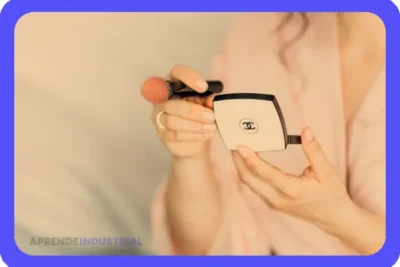
Sistema Andon de Bajo Costo: Solución Efectiva y Práctica
El sistema Andon es una herramienta fundamental en la gestión de la producción que permite a los operadores señalar problemas en tiempo real sin necesidad de abandonar su área de trabajo. Este concepto, que proviene del japonés y significa "luz", se ha convertido en un pilar dentro de las metodologías de mejora continua, especialmente en entornos de manufactura. La implementación de un sistema Andon de bajo costo no solo es viable, sino que también puede ser altamente efectivo para identificar y resolver anormalidades en el proceso productivo, mejorando así la eficiencia y la calidad del trabajo.
En este artículo, exploraremos en profundidad cómo implementar un sistema Andon de bajo costo, los requisitos previos necesarios, los pasos a seguir, los beneficios que se pueden obtener y los desafíos que podrían surgir durante su implementación. Nuestro objetivo es proporcionar una guía práctica y accesible para ingenieros industriales y profesionales del sector que deseen optimizar sus procesos mediante esta metodología. Además, se incluirán ejemplos prácticos y consejos útiles para facilitar la comprensión y aplicación del sistema.
Requisitos Previos
Antes de embarcarse en la implementación de un sistema Andon de bajo costo, es esencial contar con ciertos conocimientos y herramientas que facilitarán el proceso. A continuación, se detallan los requisitos más importantes:
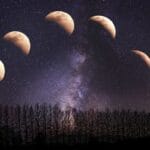
Conocimiento del Proceso Productivo
Es fundamental que los operadores y el personal involucrado en la implementación del sistema tengan un conocimiento profundo del proceso productivo. Esto incluye entender las etapas del proceso, los estándares de calidad y los puntos críticos donde pueden surgir problemas. Sin este conocimiento, será difícil identificar las anormalidades y reaccionar de manera efectiva.
Herramientas de Comunicación
La comunicación efectiva es clave para el éxito de un sistema Andon. Se recomienda contar con herramientas que faciliten la comunicación entre los operadores y el personal de supervisión. Esto puede incluir radios, teléfonos móviles o aplicaciones de mensajería instantánea. La rapidez en la comunicación permitirá una respuesta más ágil ante cualquier señal de alerta.
Capacitación del Personal
La capacitación del personal es un aspecto crucial para la implementación exitosa del sistema Andon. Todos los involucrados deben estar familiarizados con el funcionamiento del sistema, así como con los procedimientos a seguir al recibir una señal Andon. Esto incluye la identificación de problemas, la notificación a los supervisores y la documentación de las incidencias.
Lean Management: Importancia de SOP y Documentos de CalidadPasos de Implementación
La implementación de un sistema Andon de bajo costo puede dividirse en varios pasos clave. A continuación, se presenta un proceso detallado que puede ser seguido por cualquier organización:
Paso 1: Definición de Estándares
El primer paso en la implementación de un sistema Andon es definir los estándares de operación. Esto implica establecer qué constituye una anormalidad y cómo se debe señalar. Por ejemplo, si un operador detecta un problema en una máquina, debe saber que debe activar la señal Andon correspondiente.
Paso 2: Selección de Herramientas
Una vez que se han definido los estándares, el siguiente paso es seleccionar las herramientas que se utilizarán para el sistema Andon. Esto puede incluir luces LED, tableros visuales o incluso aplicaciones móviles. La elección de las herramientas dependerá del presupuesto y de las necesidades específicas de la organización.
Lean en 60 segundos: Claves para implementar Kaizen con éxitoPaso 3: Instalación del Sistema
La instalación del sistema Andon debe realizarse de manera que esté cerca de los operadores. Las luces o tableros deben ser visibles y accesibles para que los trabajadores puedan señalizar problemas sin dificultad. Es recomendable realizar pruebas del sistema antes de su implementación completa para asegurarse de que todo funcione correctamente.
Paso 4: Capacitación y Pruebas
Una vez instalado el sistema, es crucial llevar a cabo sesiones de capacitación para todos los operadores y supervisores. Durante estas sesiones, se deben realizar simulaciones de situaciones en las que se activaría la señal Andon. Esto ayudará a familiarizar al personal con el sistema y a identificar posibles áreas de mejora.
Paso 5: Monitoreo y Mejora Continua
Después de la implementación, es importante monitorear el funcionamiento del sistema Andon. Esto incluye registrar las incidencias reportadas, el tiempo de respuesta y la efectividad de las soluciones implementadas. Con base en esta información, se pueden realizar ajustes y mejoras continuas al sistema.
```html
Incidencia | Tiempo de Respuesta | Solución Implementada |
---|---|---|
Falla en la máquina 1 | 5 minutos | Reemplazo de pieza |
Problema de calidad en producto A | 10 minutos | Revisión de proceso |
```
Beneficios y Desafíos
La implementación de un sistema Andon de bajo costo ofrece una serie de beneficios significativos, aunque también puede presentar ciertos desafíos. A continuación, se analizan ambos aspectos:
Beneficios
Mejora en la Comunicación: Un sistema Andon facilita la comunicación entre los operadores y los supervisores, lo que permite una respuesta más rápida ante problemas. Esto puede resultar en una reducción del tiempo de inactividad y en una mejora general de la eficiencia operativa.
Identificación Rápida de Problemas: Al permitir que los operadores señalen problemas de manera inmediata, el sistema Andon ayuda a identificar anormalidades en tiempo real. Esto es crucial para mantener la calidad del producto y evitar que los problemas se agraven.
Fomento de la Cultura de Mejora Continua: La implementación de un sistema Andon promueve una cultura de mejora continua dentro de la organización. Los empleados se sienten empoderados para señalar problemas y contribuir a la solución, lo que puede aumentar la moral y la satisfacción laboral.
Desafíos
Resistencia al Cambio: Uno de los principales desafíos al implementar un sistema Andon puede ser la resistencia al cambio por parte de los empleados. Es importante abordar este aspecto mediante una comunicación clara sobre los beneficios del sistema y la capacitación adecuada.
Costos Iniciales: Aunque se busca un sistema de bajo costo, puede haber gastos iniciales asociados con la compra de herramientas y la capacitación del personal. Es fundamental planificar adecuadamente el presupuesto y buscar soluciones económicas.
Mantenimiento del Sistema: Una vez implementado, el sistema Andon requiere un mantenimiento regular para asegurar su correcto funcionamiento. Esto incluye la revisión de las herramientas utilizadas y la actualización de los estándares según sea necesario.
Ejemplos Prácticos
Para ilustrar la implementación de un sistema Andon de bajo costo, a continuación se presentan algunos ejemplos prácticos que pueden ser aplicados en diferentes entornos de trabajo.
Ejemplo 1: Fábrica de Ensamblaje
En una fábrica de ensamblaje, se puede implementar un sistema Andon utilizando luces LED de colores. Cada operador puede activar una luz roja si detecta un problema en su estación de trabajo. Esto alertará a los supervisores, quienes podrán acudir rápidamente para resolver la situación. Además, se puede utilizar un tablero visual para registrar las incidencias y las soluciones implementadas.
Ejemplo 2: Línea de Producción de Alimentos
En una línea de producción de alimentos, se puede utilizar un sistema de señalización basado en banderas. Cada operador puede tener una bandera de color que levantará al detectar un problema. Esto no solo es económico, sino que también es fácil de implementar y entender. La comunicación visual es clave en este entorno, donde la rapidez es esencial.
Ejemplo 3: Taller de Mantenimiento
En un taller de mantenimiento, se puede implementar un sistema Andon utilizando una aplicación móvil. Los operadores pueden enviar alertas a través de la aplicación al detectar problemas en las máquinas. Esto permite una comunicación instantánea y un registro digital de las incidencias, facilitando el seguimiento y la mejora continua.
Conclusión
El sistema Andon de bajo costo se presenta como una solución efectiva y práctica para mejorar la gestión de la producción en diversas industrias. A través de la implementación de este sistema, las organizaciones pueden lograr una comunicación más fluida, una identificación rápida de problemas y un fomento de la cultura de mejora continua.
Es fundamental que los ingenieros industriales y los profesionales del sector comprendan la importancia de este sistema y estén dispuestos a invertir tiempo y recursos en su implementación. A pesar de los desafíos que puedan surgir, los beneficios superan con creces las dificultades, y el resultado final será un entorno de trabajo más eficiente y productivo. La clave está en la capacitación, la comunicación y el compromiso de todos los involucrados en el proceso.
Si deseas profundizar más en este tema y obtener consejos adicionales, te invitamos a seguir nuestro canal de YouTube, donde compartimos más recursos y estrategias para la mejora continua en la ingeniería industrial.
Referencias
- Sistemas Andon para fábricas inteligentes
- Sistema Andon resolucion de problemas en tiempo real en ...
- Sistema Andon: Cómo funciona el sistema
Deja una respuesta
Te Puede Interesar: