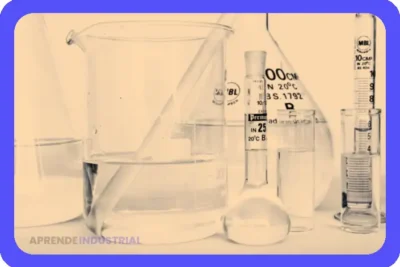
Seguridad que Funciona: Estrategias de un Gerente de Mantenimiento para un Entorno Laboral Cero Accidentes
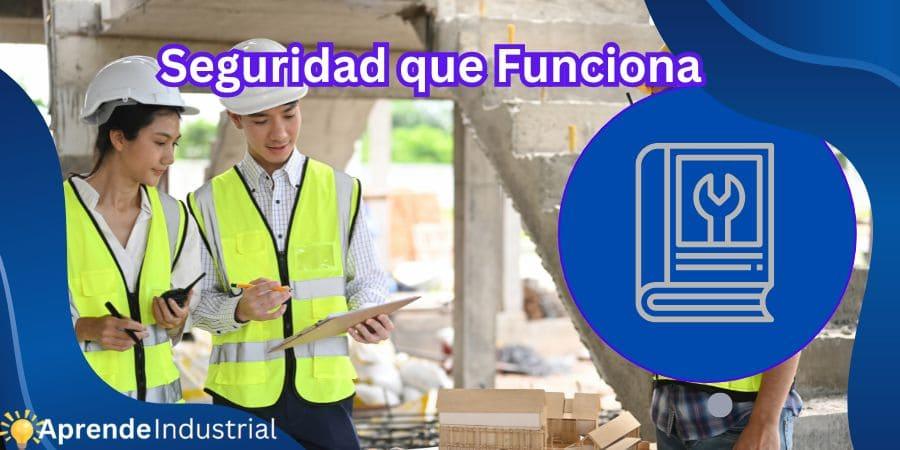
Durante años, en muchas organizaciones, Seguridad y Mantenimiento han operado como dos reinos separados. Seguridad se encargaba de los cascos, las charlas y los reportes de incidentes. Mantenimiento se encargaba de las graseras, los repuestos y los paros de emergencia. Se hablaban, sí, pero a menudo solo cuando algo ya había salido mal.
Como Gerente que ha tenido la responsabilidad de ambos mundos, he descubierto una verdad fundamental: no existe una frontera real entre un mantenimiento de clase mundial y una seguridad de clase mundial. Son dos caras de la misma moneda. Un equipo bien mantenido es un equipo seguro. Un programa de seguridad que ignora el estado de la maquinaria es un programa condenado al fracaso.
Olvídate de pensar en la seguridad solo como un conjunto de normas. Piensa en ella como el resultado natural de un entorno de trabajo predecible y controlado. Y el departamento que controla ese entorno, más que ningún otro, es Mantenimiento. Aquí te comparto mis estrategias clave para fusionar estos dos mundos y construir una cultura de "cero accidentes" desde la sala de máquinas.
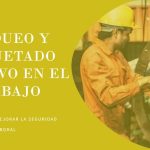
Estrategia #1: El Mantenimiento Preventivo es tu Mejor Programa de Seguridad
El enfoque reactivo: Esperar a que una máquina falle para repararla. Esto no solo causa paradas de producción, sino que crea escenarios de alto riesgo. Una reparación de emergencia es, por definición, apresurada, estresante y a menudo realizada en condiciones subóptimas.
Mi estrategia proactiva: La mayoría de los accidentes relacionados con maquinaria no ocurren durante la operación normal, sino durante intervenciones imprevistas. Un fallo catastrófico de una correa, una fuga de alta presión, un cortocircuito... son bombas de tiempo.
Plan de Mantenimiento Preventivo (MP) Robusto: Cada equipo crítico debe tener un plan de MP detallado basado en las recomendaciones del fabricante y la experiencia histórica. Esto incluye inspecciones, lubricación, calibración y sustitución de piezas de desgaste.
Integra las Inspecciones de Seguridad en las Rutinas de MP: Cuando un técnico de mantenimiento inspecciona una máquina, no solo debe revisar los componentes mecánicos. Debe revisar también las guardas de seguridad, los paros de emergencia, la señalización y las condiciones de orden y limpieza del área. El checklist de mantenimiento es un checklist de seguridad.
Cuáles son los Significados de los Símbolos de Seguridad Industrial
Análisis de Fallos (Causa Raíz): Cuando un equipo falle, no te limites a repararlo. Pregunta: ¿Por qué falló? ¿Pudo haberse prevenido? Usa herramientas como los 5 Porqués o un diagrama de Ishikawa para entender la causa raíz y ajustar tu plan de MP para que no vuelva a ocurrir.
Estrategia #2: LOTO (Lockout/Tagout) No es una Opción, es la Ley de Oro
El error mortal: "Es solo un ajuste rápido, no hace falta bloquear la energía". Esta frase ha precedido a innumerables tragedias.
Mi estrategia de "Tolerancia Cero": El procedimiento de Bloqueo y Etiquetado (LOTO) es el ritual más sagrado en cualquier intervención de mantenimiento o limpieza de maquinaria. Es la línea de defensa final e innegociable entre un trabajador y una fuente de energía peligrosa (eléctrica, mecánica, hidráulica, neumática, etc.).
Procedimientos LOTO Específicos por Máquina: No basta con un procedimiento genérico. Cada máquina compleja debe tener su propio procedimiento visual que indique claramente todos los puntos de aislamiento de energía.
5 Pasos para Implementar un SGSSO de Éxito: Guía Práctica
Candados y Tarjetas Personales e Intransferibles: Cada técnico debe tener su propio candado y su propia tarjeta. Solo él puede retirarlos. Esto elimina la confusión y asegura la responsabilidad personal.
Formación y Auditorías Constantes: La formación en LOTO no es un evento de una sola vez. Debe ser refrescada anualmente y auditada con regularidad mediante observaciones en campo para corregir desvíos y reforzar su importancia.
Estrategia #3: El Orden y la Limpieza (5S) son tus Indicadores Visuales de Riesgo
La percepción errónea: Las 5S (Clasificar, Ordenar, Limpiar, Estandarizar, Sostener) son solo una metodología para "tener el taller bonito".
Mi visión estratégica: Un área de trabajo sucia y desordenada es un campo de minas. Un derrame de aceite es un riesgo de caída. Herramientas tiradas en el suelo son riesgos de tropiezo. Trapos sucios cerca de un motor caliente son un riesgo de incendio. El desorden oculta peligros.
Empodera al Equipo de Mantenimiento como Líderes de 5S: Ellos son los que mejor conocen los equipos y las áreas de trabajo. Deben liderar con el ejemplo, manteniendo sus talleres y carros de herramientas impecables.
Limpiar es Inspeccionar: Cuando un operario o un técnico limpia una máquina, tiene la oportunidad única de detectar fugas, fisuras, pernos sueltos o cables desgastados que de otra manera pasarían desapercibidos. La limpieza es una forma de inspección proactiva.
Gestión Visual: Usa la estandarización de las 5S para mejorar la seguridad. Delimita pasillos peatonales, áreas de almacenamiento de materiales peligrosos y zonas de operación de equipos. Usa códigos de colores para tuberías. Un entorno claro y visual es un entorno intuitivo y seguro.
Conclusión
Deja de ver a tu equipo de mantenimiento solo como "reparadores de máquinas". Son los guardianes de la confiabilidad y, por extensión, los guardianes de la seguridad operativa.
Cuando inviertes en su formación, les das las herramientas adecuadas y los empoderas para que no solo reparen fallos, sino que los prevengan, estás construyendo el programa de seguridad más robusto y sostenible posible. Una cultura de seguridad que funciona no se impone desde una oficina; se construye día a día en la planta, con grasa en las manos y un profundo respeto por la maquinaria y por las personas que la operan. Y en el corazón de esa cultura, siempre encontrarás al equipo de Mantenimiento.
Te Puede Interesar: