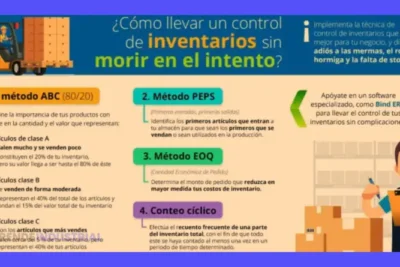
Cómo evitar la rotura de stock: Guía práctica
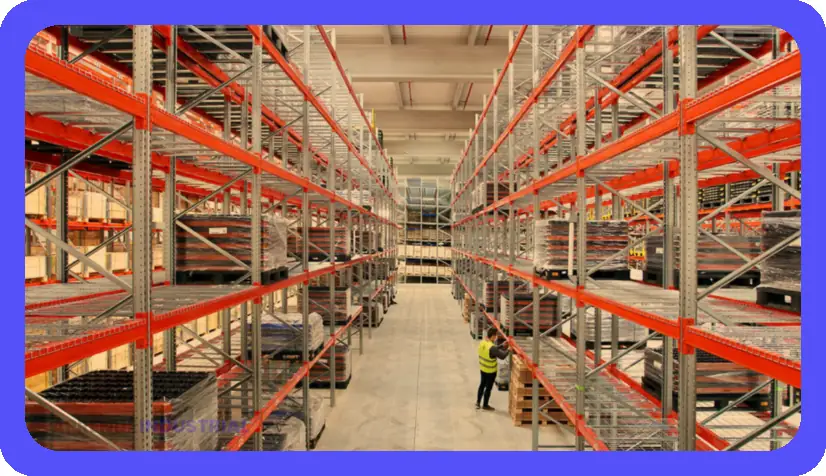
La rotura de stock, también conocida como ruptura de stock, es un problema común para muchas empresas, independientemente de su tamaño o sector. Se define simplemente como la ausencia de un producto en el inventario cuando un cliente lo solicita. Esto puede ocurrir por diversas razones, desde una mala gestión de la cadena de suministro hasta una previsión de la demanda imprecisa. Las consecuencias de una rotura de stock pueden ser devastadoras, afectando directamente las ventas, la satisfacción del cliente y, en última instancia, la rentabilidad del negocio. Un cliente insatisfecho por la falta del producto puede optar por comprarlo en la competencia, generando una pérdida inmediata de ingresos y un impacto negativo en la reputación de la empresa.
Este artículo profundizará en el análisis de la rotura de stock, explorando en detalle las causas principales, las consecuencias negativas que acarrea y, lo más importante, las estrategias efectivas para prevenirla. A lo largo del texto, se presentarán ejemplos prácticos, herramientas y técnicas que cualquier negocio puede implementar para minimizar el riesgo de experimentar una rotura de stock y, por ende, maximizar sus ganancias y la satisfacción de sus clientes. Aprenderás a optimizar tus procesos de inventario y predicción de demanda para asegurar una gestión eficiente de tus existencias.
- Comprendiendo la Rotura de Stock: Causas y Consecuencias
- Previsión de la Demanda: Clave para Evitar la Rotura de Stock
- Sistemas de Gestión de Inventario: Un Pilar Fundamental
- Control de Indicadores Clave de Rendimiento (KPI's)
- Optimización de la Cadena de Suministro: Colaboración y Eficiencia
- Inventario Permanente: Un Control Exhaustivo
- Automatización de Procesos Intralogísticos: Mayor Eficiencia y Menor Margen de Error
- Control del Deterioro de Mercancías: Evitando Pérdidas
- Conclusión
- Preguntas Frecuentes
Comprendiendo la Rotura de Stock: Causas y Consecuencias
Causa | Consecuencia |
---|---|
Incorrecta previsión de la demanda | Pérdida de ventas, daño a la reputación de la marca, insatisfacción del cliente. |
Problemas en la cadena de suministro (retrasos en la entrega, escasez de materias primas) | Disminución de la productividad, aumento de los costos de producción, incumplimiento de plazos de entrega. |
Mala gestión de inventario (falta de control, errores en el conteo de existencias) | Desabastecimiento, aumento de costos de almacenamiento, obsolescencia de productos. |
Demanda inesperada (picos de ventas estacionales o por promociones) | Pérdida de oportunidades de venta, aumento de la presión sobre los recursos. |
Problemas de producción (fallos en la maquinaria, baja eficiencia) | Reducción en la capacidad productiva, incremento en los costos de producción, plazos de entrega más largos. |
Desastres naturales o eventos imprevistos | Interrupción completa de la producción y distribución, pérdidas financieras significativas. |
La rotura de stock representa una interrupción significativa en el flujo de ventas y, por lo tanto, es crucial entender sus causas. Una de las causas más frecuentes es la imprecisión en la previsión de la demanda. Si no se estima correctamente la cantidad de productos que se necesitarán, es probable que se produzcan faltantes. Además, problemas en la cadena de suministro, como retrasos en las entregas de los proveedores o errores en el transporte, pueden contribuir a la rotura de stock. Por otro lado, un sistema de gestión de inventario deficiente dificulta el seguimiento preciso de las existencias, lo que incrementa el riesgo de quedarse sin productos. Finalmente, eventos inesperados, como desastres naturales o crisis económicas, también pueden generar rotura de stock.
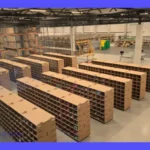
Las consecuencias de una rotura de stock son negativas para cualquier negocio. La pérdida de ventas es la más inmediata y obvia. Los clientes insatisfechos pueden optar por comprar en la competencia, lo que se traduce en una pérdida de ingresos y una disminución de la cuota de mercado. Además, la reputación de la marca se ve afectada, ya que los clientes pueden percibir a la empresa como poco confiable o ineficiente. La rotura de stock también puede generar costos adicionales, como gastos en transporte urgente para reponer el stock o en campañas de marketing para mitigar el daño a la imagen de la empresa.
La rotura de stock es un problema serio con consecuencias económicas. Una empresa que constantemente experimenta rotura de stock sufrirá una disminución significativa en sus beneficios. Los clientes insatisfechos son menos propensos a regresar, impactando la lealtad y las ventas futuras. Por lo tanto, la prevención de la rotura de stock es una prioridad crucial para la salud financiera de cualquier empresa.
Es fundamental recordar que la prevención de la rotura de stock no es solo una cuestión de tener un gran inventario. Se trata de una gestión eficiente que involucra precisión en la previsión de la demanda, optimización de la cadena de suministro, y un sistema de control de inventario efectivo. Se necesita una visión holística para prevenir este problema.
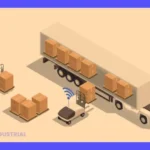
Previsión de la Demanda: Clave para Evitar la Rotura de Stock
Trimestre | Demanda Predicción (Unidades) |
---|---|
Q1 2022 | 12500 |
Q2 2022 | 15000 |
Q3 2022 | 18000 |
Q4 2022 | 22000 |
Q1 2023 | 13000 |
Q2 2023 | 16000 |
Q3 2023 | 19000 |
Q4 2023 | 23500 |
Q1 2024 | 13500 |
Q2 2024 | 17000 |
Q3 2024 | 20500 |
Q4 2024 | 25000 |
Una previsión de la demanda precisa es el primer paso crucial para prevenir la rotura de stock. Esto implica analizar datos históricos de ventas, considerar tendencias del mercado y anticipar fluctuaciones estacionales. Para ello, se pueden emplear diferentes métodos, como el análisis de series temporales, modelos de pronóstico o herramientas de inteligencia artificial. Por ejemplo, si una empresa vende más sombrillas en verano, debe anticipar este aumento en la demanda y asegurar un stock suficiente para satisfacerla. Sin embargo, es importante tener en cuenta un margen de error en la previsión, ya que los imprevistos siempre son posibles.
Para mejorar la precisión de la previsión, es recomendable segmentar la demanda. Analizar las ventas por región geográfica, grupo demográfico o producto específico permite una previsión más ajustada a las necesidades reales. Además, integrar información de otros canales de venta, como la tienda online o las ventas a través de mayoristas, proporciona una visión más completa de la demanda total. Mantener una comunicación fluida con los proveedores es vital para anticipar posibles retrasos en las entregas y ajustar la previsión en consecuencia.
El uso de software especializado puede simplificar el proceso de previsión de la demanda. Estas herramientas integran datos de diferentes fuentes, automatizan los cálculos y ofrecen reportes que facilitan la toma de decisiones. Además, la colaboración entre los equipos de ventas, marketing y operaciones es fundamental para una previsión precisa. El equipo de ventas, por ejemplo, puede aportar información valiosa sobre la demanda futura basada en la interacción directa con los clientes.
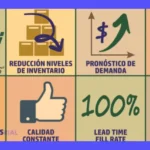
Un método sencillo para empezar es analizar las ventas de los últimos años. Si las ventas de un producto aumentaron un 10% cada año, es prudente anticipar un aumento similar para el próximo año. Sin embargo, hay que considerar factores externos que puedan afectar la demanda, como nuevas tendencias de mercado o el lanzamiento de productos similares de la competencia.
Sistemas de Gestión de Inventario: Un Pilar Fundamental
Sistema de Gestión de Inventario | Características Clave |
---|---|
Zoho Inventory | Integración con otras herramientas de Zoho, gestión de múltiples almacenes, seguimiento de pedidos, automatización de flujos de trabajo, informes personalizados. |
Fishbowl Inventory | Especializado en manufactura y distribución, gestión de lotes y números de serie, seguimiento de costos, integración con QuickBooks. |
NetSuite | Solución ERP completa que incluye gestión de inventario, ideal para empresas de gran tamaño, gestión de cadena de suministro, planificación de recursos empresariales. |
Katana MRP | Software de planificación de recursos de fabricación (MRP), ideal para empresas manufactureras, gestión de materiales, programación de producción. |
Cin7 | Gestiona múltiples canales de venta (online y offline), gestión de inventario en tiempo real, automatización de envíos, precios dinámicos. |
Un sistema de gestión de inventario eficiente es fundamental para prevenir la rotura de stock. Los sistemas de planificación de recursos empresariales (ERP) son herramientas potentes que integran la gestión de inventario con otros procesos de la empresa, como las compras, las ventas y la contabilidad. Estos sistemas permiten llevar un control preciso del stock disponible, las entradas y salidas de mercancía y las previsiones de demanda. Además, ofrecen alertas sobre el nivel de stock mínimo, lo que permite realizar pedidos de reposición a tiempo y evitar la rotura de stock.
Además de los ERP, existen sistemas de gestión de almacenes (WMS) que optimizan el almacenamiento y la logística interna. Estos sistemas automatizan tareas como la ubicación de productos en el almacén, la gestión de las ubicaciones y el seguimiento de la mercancía. Esto asegura una mayor eficiencia en la gestión del inventario y reduce el riesgo de errores. Un WMS eficiente permite una mejor localización de los productos, evitando pérdidas de tiempo en la búsqueda de artículos y optimizando el proceso de picking y packing.
Es importante escoger un sistema de gestión de inventario adecuado a las necesidades de la empresa. Las opciones varían desde sistemas simples y económicos para pequeñas empresas hasta sistemas complejos e integrados para grandes organizaciones. La elección debe considerar factores como el tamaño del inventario, la complejidad de la cadena de suministro y el presupuesto disponible.
Independientemente del sistema que se utilice, es fundamental mantener la información actualizada. La precisión de los datos es crucial para la eficacia de cualquier sistema de gestión de inventario. Los errores en la entrada de datos pueden llevar a una mala gestión del inventario y, en consecuencia, a la rotura de stock. Por lo tanto, es fundamental establecer protocolos de control de calidad de los datos ingresados.
Control de Indicadores Clave de Rendimiento (KPI's)
Para monitorear la salud del inventario y prevenir la rotura de stock, es fundamental el control de los KPI's. Algunos de los indicadores más relevantes son el punto de pedido (ROP), la rotación de inventario y el nivel de servicio. El punto de pedido (ROP) es el nivel de inventario en el cual se debe realizar un nuevo pedido para reponer el stock antes de que se agote. Este punto se calcula considerando la demanda, el tiempo de entrega de los proveedores y un margen de seguridad. La rotación de inventario mide la velocidad a la que se vende el stock durante un período determinado. Un índice de rotación alto indica una buena gestión del inventario, mientras que un índice bajo puede señalar la necesidad de ajustar la estrategia.
El nivel de servicio, por su parte, mide la capacidad de la empresa para satisfacer la demanda de sus clientes. Se expresa como el porcentaje de pedidos que se cumplen sin retrasos debido a la rotura de stock. Un nivel de servicio alto es deseable, pero también hay que tener en cuenta el coste de mantener un inventario elevado. Un equilibrio entre ambos aspectos es fundamental.
El monitoreo regular de estos KPI's permite identificar potenciales problemas y tomar acciones correctivas a tiempo. Por ejemplo, si el punto de pedido se acerca al nivel de stock actual, se debe realizar un nuevo pedido para evitar la rotura de stock. Si la rotación de inventario es baja, se debe analizar la demanda y ajustar la estrategia de gestión del stock. El uso de software de gestión de inventario facilita el seguimiento de estos KPI's y la generación de reportes que ayudan en la toma de decisiones.
Estos KPI's deben ser monitoreados de forma continua y analizados regularmente. Las tendencias detectadas en estos indicadores proporcionarán información valiosa para ajustar las estrategias de gestión del inventario. Además, la comparación de estos KPI's con los de la competencia puede ofrecer una visión externa del rendimiento de la gestión del inventario.
Optimización de la Cadena de Suministro: Colaboración y Eficiencia
Una cadena de suministro eficiente es esencial para evitar la rotura de stock. Esto implica una estrecha colaboración con los proveedores, una gestión eficaz del transporte y una planificación precisa de la producción. La comunicación con los proveedores es clave para anticipar posibles retrasos en las entregas y evitar situaciones de emergencia. Se debe contar con acuerdos claros que establezcan tiempos de entrega y penalizaciones por incumplimiento.
La selección de proveedores fiables es también crucial. Se deben considerar factores como la capacidad de producción, la experiencia, la reputación y la estabilidad financiera del proveedor. La diversificación de proveedores es una estrategia que reduce el riesgo de dependencia de un solo proveedor y protege contra posibles imprevistos. Un buen sistema de seguimiento y trazabilidad de las mercancías desde el origen hasta el almacén facilita la gestión de la cadena de suministro.
La optimización del transporte implica elegir los medios de transporte adecuados, considerando la urgencia de la entrega y el coste del transporte. La utilización de sistemas de seguimiento permite monitorizar el estado de los envíos en tiempo real y anticipar posibles retrasos. Una gestión eficiente del transporte reduce el riesgo de retrasos y asegura una llegada puntual de la mercancía.
Una buena planificación de la producción es vital para evitar la rotura de stock, sobre todo en la producción propia. El análisis de la demanda permite ajustar la producción a las necesidades reales y evitar la sobreproducción o la falta de productos. La gestión de los inventarios de materias primas es crucial para garantizar el suministro continuo de materiales necesarios para la producción.
Inventario Permanente: Un Control Exhaustivo
La implementación de un sistema de inventario permanente permite un control exhaustivo del stock en tiempo real. A diferencia de los sistemas periódicos, donde el inventario se verifica en momentos específicos, el inventario permanente realiza el seguimiento del stock después de cada transacción. Este sistema ofrece mayor precisión en el conocimiento de las existencias, lo que disminuye el riesgo de rotura de stock.
Un inventario permanente requiere un sistema de gestión informatizado que registra automáticamente las entradas y salidas de mercancía. Este sistema debe estar integrado con otros sistemas de la empresa, como el sistema de punto de venta (POS) y el sistema de gestión de almacenes (WMS). La integración de datos permite una visibilidad completa del inventario en todo momento.
La precisión del inventario permanente depende de la exactitud de las transacciones registradas. Es fundamental contar con un sistema robusto de control de calidad de la información ingresada y de conciliación entre los registros físicos y los sistemas informáticos. Los inventarios cíclicos son una práctica complementaria que ayuda a verificar la exactitud del inventario permanente y a detectar posibles errores o inconsistencias.
Aunque más complejo de implementar que un sistema de inventario periódico, la información en tiempo real que ofrece un inventario permanente es vital para una correcta toma de decisiones. Esta información permite responder de forma ágil a las fluctuaciones en la demanda y a los cambios en la cadena de suministro, minimizando así el riesgo de rotura de stock. La mejora en la visibilidad del inventario permite optimizar la gestión de stocks, minimizar los costes de almacenaje y prevenir posibles pérdidas por obsolescencia.
Automatización de Procesos Intralogísticos: Mayor Eficiencia y Menor Margen de Error
La automatización de los procesos intralogísticos, es decir, los procesos internos de un almacén, juega un papel esencial para prevenir la rotura de stock. La automatización permite reducir los errores humanos, mejorar la eficiencia y aumentar la velocidad de los procesos de manipulación de materiales. Ejemplos de automatización incluyen el uso de robots móviles autónomos (AMR), sistemas de clasificación automática y sistemas de gestión de almacenes (WMS) avanzados.
Los AMR pueden encargarse del transporte de mercancías dentro del almacén, reduciendo los tiempos de movimiento y optimizando el flujo de materiales. Los sistemas de clasificación automática, por su parte, ordenan y dirigen las mercancías a sus ubicaciones correctas en el almacén, minimizando los errores y aumentando la velocidad de procesamiento. Sistemas WMS avanzados ofrecen funcionalidades como la optimización de la ubicación de los productos en el almacén, la planificación de rutas óptimas para los operarios y el seguimiento en tiempo real del inventario.
La automatización no solo aumenta la eficiencia y reduce errores, sino que también permite una mejor utilización del espacio de almacenamiento. Al optimizar los procesos de manipulación de materiales, se aprovecha al máximo el espacio disponible, minimizando los costes de almacenaje.
Para implementar la automatización, es importante evaluar las necesidades específicas del almacén y elegir las soluciones que mejor se adapten a ellas. Se deben considerar factores como el tamaño del almacén, el volumen de mercancías, el tipo de productos y el presupuesto disponible. Además, es fundamental contar con la formación adecuada del personal para operar y mantener los sistemas automatizados.
Control del Deterioro de Mercancías: Evitando Pérdidas
El deterioro de mercancías es un factor que puede contribuir significativamente a la rotura de stock, aunque de manera indirecta. Cuando los productos se deterioran o caducan, se reduce el stock disponible, creando una situación de escasez que puede afectar las ventas. Para evitarlo, es esencial implementar un sistema de gestión de la calidad que controle la caducidad y el estado de las mercancías.
Esto incluye el uso de sistemas de gestión del inventario que rastreen la fecha de caducidad de los productos y generen alertas cuando se acercan a su fecha límite. Se debe establecer un sistema de rotación de stocks (FIFO o FEFO) para asegurar que los productos más antiguos se vendan primero. Además, es importante controlar las condiciones de almacenamiento, asegurando que la temperatura, la humedad y la iluminación sean las adecuadas para cada tipo de producto.
La implementación de un sistema de control de calidad que revise la mercancía al entrar y salir del almacén ayuda a detectar posibles problemas de deterioro antes de que afecten significativamente el stock. El registro de los daños y la causa de estos puede ayudar a evitar problemas similares en el futuro. Además, es importante considerar la posibilidad de ofrecer descuentos o promociones en productos con fechas de caducidad próximas para acelerar su venta y evitar pérdidas.
Un control exhaustivo de la mercancía evita no solo pérdidas económicas sino también problemas de seguridad alimentaria o de salud relacionados con productos deteriorados. Una correcta gestión de la caducidad contribuye a la satisfacción del cliente, ya que asegura la entrega de productos en óptimas condiciones.
Conclusión
La prevención de la rotura de stock es un desafío clave para cualquier negocio que busca optimizar su eficiencia y satisfacer a sus clientes. Como hemos visto a lo largo de este artículo, no se trata simplemente de tener un gran inventario, sino de una gestión integrada y estratégica que considera la previsión precisa de la demanda, la optimización de la cadena de suministro, la implementación de sistemas de gestión de inventario eficientes, el monitoreo constante de KPI's y el control del deterioro de mercancías.
La aplicación de las estrategias detalladas, desde la mejora en la previsión de la demanda hasta la automatización de los procesos intralogísticos, reduce significativamente el riesgo de experimentar roturas de stock. Recuerda que la inversión en tecnología y la formación del personal son cruciales para la implementación exitosa de estas estrategias. Una adecuada gestión del inventario asegura no solo la satisfacción del cliente, sino también la salud financiera de la empresa a largo plazo. El correcto manejo de la rotura de stock implica un control meticuloso de cada etapa del proceso, desde la adquisición de materia prima hasta la entrega del producto al cliente final.
Preguntas Frecuentes
¿Qué es el punto de pedido en la gestión de inventario?
Es el nivel de inventario que desencadena un nuevo pedido de reposición para evitar una rotura de stock. Se calcula considerando la demanda, el tiempo de entrega y un margen de seguridad.
¿Cómo puedo mejorar la precisión de mi previsión de la demanda?
Implementando un sistema de recogida de datos más preciso, utilizando herramientas de análisis predictivo e incluyendo la retroalimentación del equipo de ventas en el proceso de predicción.
¿Qué herramientas tecnológicas puedo utilizar para prevenir la rotura de stock?
Existen sistemas ERP, WMS y software especializados en gestión de inventarios que automatizan el proceso, facilitan la previsión y alertan sobre bajos niveles de stock.
¿Qué pasa si tengo una rotura de stock constante?
Se produce una pérdida significativa de ventas, daño a la imagen de la marca, disminución de la fidelización de clientes y aumento de costos logísticos para solucionar la falta de producto.
¿Qué es la rotación de inventario y por qué es importante?
Mide la velocidad a la que se vende el stock. Un índice de rotación bajo indica una mala gestión de inventario, lo que puede generar roturas de stock.
Deja una respuesta
Te Puede Interesar: