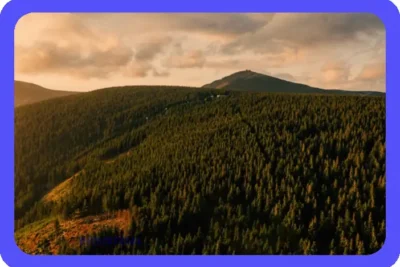
Cómo optimizar procesos industriales: Guía práctica
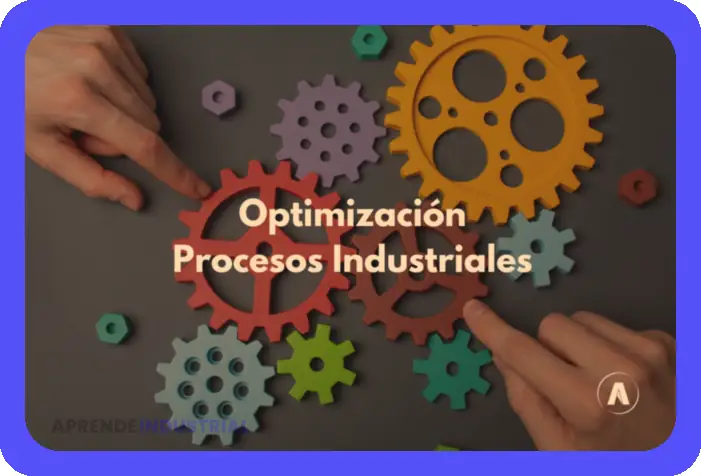
La optimización de procesos industriales es un pilar fundamental para el éxito en el competitivo panorama actual. En un mundo donde la eficiencia y la productividad son cruciales, las empresas buscan constantemente maneras de mejorar sus operaciones y reducir costos. Esto implica mucho más que simplemente aumentar la velocidad de producción; se trata de analizar profundamente cada etapa del proceso de producción, desde la adquisición de materia prima hasta la distribución del producto final, con el objetivo de identificar cuellos de botella y áreas de mejora. La optimización de procesos industriales no solo se limita a las fábricas; es aplicable a cualquier tipo de industria, desde la manufactura hasta los servicios.
Este artículo profundiza en el tema de la optimización de procesos industriales, explorando en detalle los aspectos clave necesarios para lograr una mejora sustancial en la eficiencia y la rentabilidad. Analizaremos diversas metodologías, herramientas y estrategias que las empresas pueden implementar para alcanzar una verdadera transformación en sus operaciones. Además, se presentarán ejemplos concretos y casos de estudio que ilustran los beneficios de una correcta optimización de procesos industriales.
- Identificando Oportunidades de Mejora en la Optimización de Procesos Industriales
- Mejora Continua (Kaizen) y la Optimización de Procesos Industriales
- Tecnología y Digitalización para la Optimización de Procesos Industriales
- Reducción de Costos a través de la Optimización de Procesos Industriales
- Mejora de la Calidad del Producto y la Satisfacción del Cliente mediante la Optimización de Procesos Industriales
- Medición y Monitoreo del Rendimiento en la Optimización de Procesos Industriales
- Herramientas y Metodologías para la Optimización de Procesos Industriales
- Casos de Éxito en la Optimización de Procesos Industriales
- Conclusión
- Preguntas Frecuentes
Identificando Oportunidades de Mejora en la Optimización de Procesos Industriales
Área de Mejora | Impacto Potencial | Acciones Recomendadas |
---|---|---|
Reducción de tiempos de inactividad en la línea de producción de ensamblaje | Aumento de la producción en un 15%, reducción de costos de mano de obra en un 8% | Implementación de un sistema de mantenimiento predictivo, capacitación adicional para operadores. |
Optimización del consumo de energía en el proceso de fundición | Reducción del consumo de energía en un 12%, disminución de la huella de carbono en un 10% | Actualización de equipos a modelos de mayor eficiencia energética, implementación de un sistema de monitoreo del consumo energético. |
Mejora en la gestión de inventario de materia prima | Reducción de costos de almacenamiento en un 7%, disminución de pérdidas por obsolescencia en un 5% | Implementación de un sistema de gestión de inventario justo a tiempo (JIT), mejora en la predicción de la demanda. |
Automatización del proceso de control de calidad | Reducción de errores en un 20%, aumento de la eficiencia en el control de calidad en un 18% | Implementación de un sistema de visión artificial, automatización del proceso de inspección. |
La primera etapa en la optimización de procesos industriales es la identificación precisa de las áreas que requieren atención. Este paso, crucial para el éxito de la iniciativa, involucra un análisis exhaustivo de cada etapa del proceso. Se debe prestar atención a los tiempos de ciclo, los niveles de inventario, los recursos utilizados (materia prima, energía, mano de obra) y la calidad del producto final. A menudo, las áreas con mayor potencial de mejora son aquellas que presentan cuellos de botella, alta tasa de defectos o altos costos. Por ejemplo, un análisis de la línea de producción podría revelar que una máquina en particular es constantemente un punto de congestión, frenando todo el proceso.
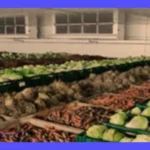
Es fundamental recopilar datos precisos, utilizando herramientas de monitoreo y análisis. Diagramas de flujo, mapas de procesos, y análisis de tiempos y movimientos son técnicas útiles para visualizar el flujo de trabajo y detectar ineficiencias. Además, es importante involucrar a los empleados en este proceso, ya que ellos poseen un conocimiento profundo de las operaciones cotidianas y pueden aportar información valiosa. Su experiencia proporciona una perspectiva única e irremplazable para detectar problemas ocultos. Una vez identificadas las áreas problemáticas, se puede comenzar a desarrollar planes de acción para su mejora.
El uso de herramientas tecnológicas, como software de gestión de procesos empresariales (BPM), puede facilitar significativamente la identificación de áreas de mejora. Estas herramientas permiten monitorear el rendimiento en tiempo real, generar reportes detallados y analizar grandes cantidades de datos para detectar patrones y tendencias. La automatización de ciertas tareas también puede liberar tiempo y recursos, permitiendo centrar la atención en las áreas que requieren más atención. La integración de la tecnología debe considerarse como parte integral de la optimización de procesos industriales.
Otro factor crucial es el análisis de los datos históricos. Mediante el estudio de los datos pasados, se pueden identificar tendencias y patrones que ayudan a predecir problemas futuros y a optimizar la planificación de los recursos. Además, el análisis de la información permite evaluar la efectividad de las medidas ya implementadas y ajustar los planes de acción según sea necesario. Sin esta evaluación continua, es difícil determinar el verdadero impacto de las iniciativas de optimización de procesos industriales. Un análisis profundo y sistemático es la clave para iniciar una efectiva mejora de procesos.
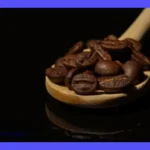
Mejora Continua (Kaizen) y la Optimización de Procesos Industriales
Implementación de Kaizen | Resultado |
---|---|
Reducción del tiempo de inactividad de la máquina mediante la implementación de un sistema de mantenimiento preventivo en una planta de ensamblaje de automóviles (Toyota, 2010-2012). | Disminución del 15% en el tiempo de inactividad, aumento del 12% en la producción y reducción del 8% en los costos de mantenimiento. |
Mejora del diseño del flujo de trabajo en una línea de producción de electrónica (Foxconn, 2018-2019). Se eliminaron cuellos de botella identificados a través del análisis de Value Stream Mapping. | Aumento del 20% en la eficiencia de la línea de producción, reducción del 10% en los defectos y mejora de la satisfacción laboral en un 15%. |
Implementación de un sistema 5S en una fábrica de textiles (Ejemplo ficticio, 2022-2023). Se enfocó en la organización del espacio de trabajo, limpieza y estandarización de procesos. | Reducción del 12% en los accidentes laborales, mejora en la calidad del producto y disminución del 7% en el tiempo de búsqueda de materiales. |
Utilización de círculos de calidad (QC) para mejorar la eficiencia en el proceso de embalaje en una empresa de alimentos (Ejemplo ficticio, 2021-2022). | Reducción del 8% en los costos de embalaje, aumento de la eficiencia del 10% y mejora en la calidad del embalaje. |
La filosofía Kaizen, que se traduce como "mejora continua," es fundamental para la optimización de procesos industriales. Este enfoque se centra en la mejora incremental y constante, en lugar de grandes cambios revolucionarios. Kaizen fomenta la participación de todos los empleados en la identificación y resolución de problemas, promoviendo un ambiente de colaboración y mejora continua. Aplicando este concepto, las empresas pueden realizar pequeños cambios graduales que, con el tiempo, producen mejoras significativas en la eficiencia y la productividad.
Un ejemplo de la aplicación de Kaizen podría ser la reorganización del espacio de trabajo para facilitar el flujo de materiales. Pequeñas modificaciones en la disposición de las máquinas, el almacenamiento de insumos o la distribución del espacio de trabajo pueden tener un impacto considerable en la velocidad de producción y la reducción de movimientos innecesarios. Otros ejemplos pueden ser la simplificación de procesos, la eliminación de pasos redundantes o la implementación de mejoras en la seguridad laboral. La metodología Kaizen destaca la importancia de la eficiencia y la reducción de desperdicios.
La metodología Kaizen se basa en la colaboración y la comunicación abierta. Se fomenta la participación activa de todos los empleados, desde los operarios hasta la alta gerencia, creando un ambiente de trabajo colaborativo en el que todos puedan contribuir con sus ideas e iniciativas. Es importante establecer una cultura organizacional que fomente la innovación y la mejora continua, donde las sugerencias de los empleados sean valoradas y consideradas.

Además del Kaizen, existen otras metodologías de mejora, como Lean Manufacturing y Six Sigma, que se enfocan en la eliminación de desperdicios y la mejora de la calidad, respectivamente. Estas metodologías complementan y enriquecen las estrategias de optimización de procesos industriales, ofreciendo un marco de trabajo estructurado para la mejora continua. La integración de diferentes enfoques puede ser fundamental para obtener resultados óptimos. El éxito de la optimización de procesos industriales depende, en gran medida, de la implementación consistente de estas metodologías.
La clave del éxito en la implementación de Kaizen radica en la capacidad para lograr que los cambios sean sostenibles. Es decir, no basta con implementar una mejora, sino que se debe asegurar que esta mejora se mantenga en el tiempo, incorporándose a los procesos de trabajo habituales. Para ello es importante documentar los cambios, capacitar a los empleados, y monitorear constantemente el rendimiento para asegurar que los resultados se mantienen.
Tecnología y Digitalización para la Optimización de Procesos Industriales
Tecnología | Beneficios y Aplicaciones |
---|---|
Internet de las Cosas (IoT) | Monitoreo en tiempo real de equipos y procesos, predicción de fallas, optimización de la cadena de suministro, mejora de la eficiencia energética. Ejemplo: Sensores en maquinaria detectan vibraciones anormales, permitiendo mantenimiento predictivo y evitando costosas paradas. |
Inteligencia Artificial (IA) y Machine Learning (ML) | Análisis predictivo de datos, automatización de tareas, optimización de la producción, control de calidad mejorado. Ejemplo: Algoritmos de IA analizan datos de producción para identificar patrones y optimizar la configuración de las máquinas, aumentando la productividad. |
Realidad Aumentada (RA) | Soporte remoto para técnicos, entrenamiento de empleados, mejora de la eficiencia en la fabricación y mantenimiento. Ejemplo: Técnicos utilizan gafas de RA para visualizar instrucciones superpuestas en equipos, facilitando las reparaciones. |
Robótica y Automatización | Aumento de la productividad, reducción de costos laborales, mejora de la seguridad en entornos peligrosos. Ejemplo: Robots colaborativos (cobots) trabajan junto a humanos en líneas de ensamblaje, realizando tareas repetitivas y peligrosas. |
Big Data y Analítica | Identificación de tendencias, mejora de la toma de decisiones, optimización de recursos, descubrimiento de nuevas oportunidades de negocio. Ejemplo: Análisis de grandes conjuntos de datos de producción para identificar cuellos de botella y optimizar los procesos. |
La tecnología juega un rol fundamental en la optimización de procesos industriales en la actualidad. La digitalización permite el monitoreo en tiempo real de los procesos, la automatización de tareas repetitivas, el análisis de datos complejos y la mejora de la toma de decisiones. Sistemas de gestión de producción, software de análisis de datos, robots industriales, y sensores inteligentes son herramientas clave para la optimización.
La implementación de sistemas de gestión de la cadena de suministro (SCM) permite una mejor planificación de la producción, gestión del inventario, y optimización de la logística. Esto puede reducir costos, minimizar los retrasos, y asegurar la entrega oportuna de los productos al cliente. Por ejemplo, un sistema SCM eficiente puede predecir con precisión la demanda futura, optimizando la producción para evitar sobreproducción o escasez de inventario.
La automatización de procesos repetitivos libera a los trabajadores de tareas tediosas y les permite enfocarse en actividades de mayor valor agregado, como la resolución de problemas y la innovación. Robots industriales, sistemas de automatización programable (PLC), y otras tecnologías automatizadas pueden aumentar la productividad, reducir errores y mejorar la seguridad en el lugar de trabajo. Es esencial integrar las nuevas tecnologías con las herramientas existentes para aprovechar al máximo su potencial.
Además, la recopilación y el análisis de grandes volúmenes de datos (Big Data) permite identificar patrones y tendencias que son imposibles de detectar mediante métodos tradicionales. El análisis de datos proporciona información valiosa para la mejora de los procesos, la optimización de la toma de decisiones y la predicción de problemas potenciales. Por ejemplo, el análisis de datos puede identificar las causas de las fallas en la producción, permitiéndole prevenirlas en el futuro. Por lo tanto, invertir en tecnología y en el análisis de datos es crucial para una efectiva optimización de procesos industriales.
La transformación digital de la industria no se limita a la adopción de nuevas tecnologías, sino que requiere un cambio cultural y una reorganización de los procesos de trabajo. Las empresas deben capacitar a sus empleados para que puedan utilizar las nuevas herramientas y tecnologías de manera eficiente y efectiva. Además, deben crear una cultura de innovación y colaboración que fomente la adopción de nuevas tecnologías y la mejora continua.
Reducción de Costos a través de la Optimización de Procesos Industriales
Una de las ventajas más significativas de la optimización de procesos industriales es la reducción de costos. Al eliminar la ineficiencia y el desperdicio, las empresas pueden reducir los gastos operativos y mejorar su rentabilidad. La reducción de costos se puede lograr a través de varios métodos, incluyendo la optimización del consumo de energía, la mejora de la utilización de recursos y la reducción de defectos.
La mejora en la eficiencia energética puede resultar en importantes ahorros. La identificación y la eliminación de fuentes de desperdicio energético, como el uso de equipos ineficientes o prácticas de consumo derrochadoras, pueden reducir significativamente los costos de energía. La optimización de los procesos de producción puede minimizar el consumo de materia prima y reducir el desperdicio. Un ejemplo podría ser la implementación de técnicas de producción justo a tiempo para reducir el inventario y el desperdicio de materiales.
La reducción de la tasa de defectos es otra forma clave para ahorrar dinero. La identificación y eliminación de las causas de los defectos en el proceso productivo puede reducir los costos asociados con las reparaciones, los rechazos y las devoluciones. La implementación de programas de control de calidad y la utilización de tecnologías de inspección pueden ayudar a identificar y corregir los problemas de calidad antes de que lleguen al cliente.
La optimización de los procesos de logística también puede resultar en significativos ahorros de costos. La optimización de rutas, la mejora de los procesos de envío y la implementación de sistemas de gestión de inventario pueden reducir los costos de transporte y almacenamiento. Por ejemplo, la consolidación de envíos puede reducir el número de entregas, minimizando los costos de transporte. Así pues, la optimización de procesos industriales puede contribuir de forma notable a la mejora de los resultados económicos de una empresa.
A través de una cuidadosa evaluación de los costos en todas las etapas del proceso, las empresas pueden identificar nuevas oportunidades de ahorro. El análisis de datos proporciona información valiosa para identificar áreas con alto potencial de reducción de costos. La implementación de un sistema de gestión de costos permite el seguimiento y el control de los gastos, permitiendo que las empresas tomen decisiones informadas para optimizar sus procesos y reducir los costos.
Mejora de la Calidad del Producto y la Satisfacción del Cliente mediante la Optimización de Procesos Industriales
La optimización de procesos industriales no solo beneficia a la empresa en términos de eficiencia y reducción de costos; también tiene un impacto significativo en la calidad del producto y la satisfacción del cliente. Al mejorar los procesos, se reducen los errores, se aumenta la consistencia y se mejora la confiabilidad del producto final. Esto lleva a una mayor satisfacción del cliente y a una mejora en la reputación de la marca.
La mejora de la calidad se logra mediante la implementación de un sistema de gestión de la calidad (SGC) como ISO 9001. Este sistema ayuda a la empresa a identificar y eliminar las causas de defectos, asegurando que el producto final cumpla con los estándares de calidad requeridos. Además, la implementación de controles de calidad en cada etapa del proceso ayuda a prevenir defectos y a garantizar la consistencia del producto.
Los sistemas de control de calidad son herramientas importantes en la mejora de procesos. Mediante la inspección regular de los productos y el seguimiento de los indicadores clave de rendimiento, se puede identificar rápidamente cualquier desviación de los estándares de calidad y tomar medidas correctivas. Ejemplos de indicadores clave de rendimiento (KPI) son la tasa de defectos, el tiempo de ciclo y la eficiencia de la producción. El seguimiento y el análisis de los KPI proporciona información valiosa para identificar áreas de mejora.
Un cliente satisfecho es un activo valioso para la empresa, y la optimización de procesos industriales contribuye directamente a esto. Los productos de alta calidad, la entrega oportuna y un servicio al cliente excelente son elementos fundamentales para la satisfacción del cliente. Las empresas que implementan eficientemente la optimización de procesos industriales pueden ofrecer productos y servicios de mayor calidad, mejorando así la fidelización de los clientes y su reputación en el mercado.
La comunicación efectiva con el cliente es otro componente importante para la satisfacción. La obtención de feedback del cliente y el seguimiento de las opiniones permiten a las empresas identificar áreas de mejora en sus procesos y productos. Al tener en cuenta las necesidades y expectativas de los clientes, las empresas pueden mejorar sus procesos y entregar productos y servicios que superen las expectativas del cliente, lo que fortalece la relación entre la empresa y sus clientes.
Medición y Monitoreo del Rendimiento en la Optimización de Procesos Industriales
La medición y el monitoreo del rendimiento son cruciales para evaluar la efectividad de la optimización de procesos industriales. Este proceso permite identificar áreas de mejora, hacer ajustes en el plan de optimización y justificar la inversión en estas mejoras. Los indicadores clave de rendimiento (KPIs) se utilizan para rastrear el progreso y medir el impacto de las iniciativas de optimización. Algunos KPIs comunes incluyen el tiempo de ciclo, la tasa de defectos, el costo unitario y la eficiencia de la producción.
El uso de software de gestión de procesos empresariales (BPM) facilita la recopilación y el análisis de datos de rendimiento. Estos sistemas proporcionan paneles de control en tiempo real que muestran el progreso y los indicadores clave de rendimiento. Esta visibilidad mejora la toma de decisiones y permite a las empresas ajustar rápidamente sus estrategias en función de los datos. Las alertas automáticas notifican a los gerentes sobre posibles desviaciones de los objetivos, facilitando la respuesta rápida a cualquier problema.
Es fundamental establecer metas específicas, medibles, alcanzables, relevantes y con plazos definidos (SMART) para el proceso de optimización. Esto permite a las empresas monitorear el progreso con claridad y evaluar la efectividad de las iniciativas de optimización. El seguimiento del progreso ayuda a mantener a todos los miembros del equipo enfocados en los objetivos y a celebrar los éxitos a lo largo del proceso.
El análisis de datos es esencial para obtener información valiosa del monitoreo del rendimiento. Las técnicas de análisis de datos, como el análisis estadístico y la minería de datos, ayudan a identificar patrones, tendencias y correlaciones que pueden pasar desapercibidas en un análisis superficial. Este análisis de datos profundos ayuda a identificar las causas raíz de los problemas y a mejorar la efectividad de las intervenciones correctivas.
Mediante el monitoreo continuo del rendimiento, las empresas pueden adaptarse a los cambios en el mercado y en el entorno de negocio. El análisis de la información ayuda a identificar los riesgos potenciales y las oportunidades de mejora. La capacidad de respuesta y adaptabilidad es esencial para el éxito en un mercado competitivo. Por tanto, la medición y el monitoreo continuo del rendimiento son fundamentales para mantener los beneficios de la optimización de procesos industriales a largo plazo.
Herramientas y Metodologías para la Optimización de Procesos Industriales
Existen diversas herramientas y metodologías que pueden utilizarse para la optimización de procesos industriales. La selección de las herramientas y metodologías más apropiadas dependerá de las necesidades específicas de cada empresa y del tipo de proceso que se busca optimizar. Algunas de las herramientas y metodologías más comunes incluyen el mapeo de procesos, el análisis de valor, la simulación y el análisis de la cadena de valor.
El mapeo de procesos es una técnica visual que representa gráficamente los pasos involucrados en un proceso. Esto ayuda a identificar cuellos de botella, redundancias y áreas de mejora. El mapeo de procesos facilita la comprensión del proceso y permite la identificación de las áreas con mayor potencial de optimización. Existen diferentes tipos de mapas de procesos, como los diagramas de flujo, los diagramas SIPOC y los mapas de flujo de valor.
El análisis de valor es una herramienta que se utiliza para identificar las funciones de un producto o proceso y determinar si las funciones se están realizando de manera eficiente y eficaz. Esto ayuda a eliminar funciones no esenciales y a mejorar la eficiencia del proceso. El análisis de valor se puede aplicar a cualquier producto o proceso, desde un producto manufacturado hasta un proceso de servicio.
La simulación es una técnica que se utiliza para modelar un proceso y analizar su comportamiento bajo diferentes escenarios. Esto permite a las empresas experimentar con diferentes configuraciones de procesos y predecir el impacto de los cambios antes de implementarlos. La simulación es una herramienta poderosa para la toma de decisiones y para la reducción del riesgo.
El análisis de la cadena de valor es una herramienta que se utiliza para analizar todas las actividades involucradas en la creación de un producto o servicio, desde la adquisición de materias primas hasta la entrega al cliente. Esto ayuda a identificar las áreas donde se puede agregar valor y mejorar la eficiencia del proceso. El análisis de la cadena de valor permite a las empresas mejorar su posición competitiva en el mercado.
La selección de las herramientas y metodologías más apropiadas dependerá del contexto específico de cada empresa. Es importante combinar diferentes herramientas y metodologías para maximizar los beneficios de la optimización de procesos industriales. La aplicación adecuada de estas herramientas y metodologías es fundamental para lograr resultados positivos en la optimización de procesos industriales.
Casos de Éxito en la Optimización de Procesos Industriales
Muchos casos de éxito demuestran el impacto positivo de la optimización de procesos industriales. Por ejemplo, una empresa manufacturera pudo reducir sus costos operativos en un 15% al implementar un sistema de gestión de la producción (MPS) y al mejorar sus procesos de control de inventario. Otro ejemplo es una empresa de logística que logró reducir sus tiempos de entrega en un 20% al optimizar sus rutas de entrega y al implementar un sistema de gestión de transporte (TMS).
Una empresa en el sector alimentario, al aplicar los principios Lean, eliminó pasos redundantes en su línea de producción, resultando en un aumento de la eficiencia del 10% y una reducción de residuos. Mientras que, en la industria textil, la incorporación de nuevas tecnologías de automatización llevó a una significativa reducción de costos y un aumento en la calidad del producto.
Estos casos de éxito demuestran la importancia de la optimización de procesos industriales para la competitividad. Sin embargo, es crucial entender que cada industria y empresa tiene sus peculiaridades. Por lo tanto, no hay una solución única para todos, sino que la implementación de estrategias de optimización debe ser personalizada y adaptada a las circunstancias específicas de cada caso. La clave está en un análisis profundo y la selección de las herramientas y metodologías adecuadas.
A pesar de los diferentes sectores, varios factores comunes contribuyen al éxito de la optimización de procesos industriales. Estos incluyen el compromiso de la alta dirección, la participación de los empleados, la selección de KPIs adecuados para el monitoreo, y la implementación de un sistema de gestión de cambios. Es importante recordar que el éxito a largo plazo depende de la cultura organizacional, que debe fomentar la mejora continua y la innovación.
El análisis de casos de éxito y las lecciones aprendidas de estos ejemplos pueden servir como guía para otras empresas que deseen implementar iniciativas de optimización de procesos industriales. Estudiar estos ejemplos permite identificar mejores prácticas y evitar errores comunes. Además, el compartir experiencias entre empresas puede promover la cooperación y el aprendizaje mutuo, acelerando la adopción de mejores prácticas en la industria.
Conclusión
La optimización de procesos industriales es una estrategia vital para cualquier empresa que busque mejorar su eficiencia, reducir costos, aumentar la calidad de sus productos y mejorar la satisfacción del cliente. Este proceso requiere un análisis profundo de las operaciones, la identificación de áreas de mejora, la implementación de metodologías como Kaizen y el uso de herramientas tecnológicas. La medición y el monitoreo del rendimiento son cruciales para garantizar el éxito a largo plazo.
Las empresas que adoptan una cultura de mejora continua y que invierten en la optimización de procesos industriales se posicionan para un crecimiento sostenible y un mayor éxito en el mercado competitivo. La aplicación efectiva de estas estrategias no solo impulsa la rentabilidad, sino que también mejora la satisfacción del cliente y la reputación de la marca. La transformación no es solo tecnológica, sino también cultural, requiriendo la participación activa de todos los niveles de la organización. Por lo tanto, el compromiso continuo con la mejora es clave para obtener los beneficios a largo plazo de la optimización de procesos industriales.
Preguntas Frecuentes
¿Qué beneficios ofrece la optimización de procesos industriales?
Aumenta la eficiencia y la productividad, reduciendo costos y mejorando la calidad del producto.
¿Cuáles son las metodologías clave para la optimización de procesos industriales?
Kaizen (mejora continua), Lean Manufacturing y Six Sigma son las más utilizadas.
¿Qué papel juega la tecnología en la optimización de procesos industriales?
Permite el monitoreo en tiempo real, la automatización y el análisis de datos para una mejor toma de decisiones.
¿Cómo se mide el éxito de la optimización de procesos industriales?
A través del seguimiento de KPIs como tiempo de ciclo, tasa de defectos, costo unitario y eficiencia de producción.
¿Es costoso implementar la optimización de procesos industriales?
El costo varía, pero las mejoras en eficiencia a menudo superan la inversión inicial.
Deja una respuesta
Te Puede Interesar: