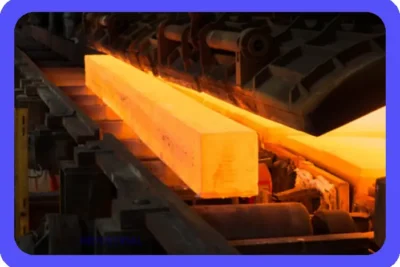
Optimización de Procesos al Descubierto: Secretos de un Ingeniero de Métodos con Décadas de Experiencia
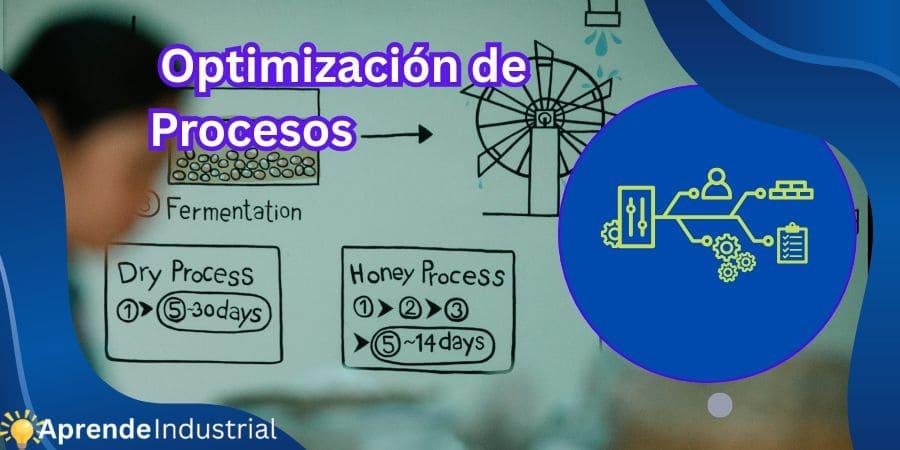
Mi primer trabajo como Ingeniero de Métodos me enseñó la lección más importante de mi carrera: la mayor parte del "trabajo" que vemos en una planta no aporta valor. Es movimiento, es espera, es transporte, es corrección de errores. Es desperdicio.
La verdadera optimización de procesos no consiste en hacer que la gente trabaje más rápido. Consiste en hacer que trabaje de manera más inteligente, eliminando sistemáticamente todo aquello que no contribuye directamente a transformar la materia prima en un producto que el cliente valora. Es el arte de ver lo invisible, de cuestionar el "siempre se ha hecho así" y de encontrar la elegancia en la simplicidad.
Durante años, con un cronómetro en una mano y un diagrama de espagueti en la otra, he diseccionado cientos de procesos. He aprendido que las mejores ideas no siempre vienen de un software complejo, sino de una observación atenta y de las preguntas correctas. Aquí te comparto algunos de los "secretos" o, mejor dicho, los principios fundamentales que he aplicado una y otra vez para transformar procesos caóticos en operaciones fluidas y rentables.
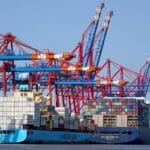
Secreto #1: Tu Herramienta Más Poderosa no es el Cronómetro, es el "Gemba Walk"
"Gemba" es un término japonés que significa "el lugar real", el sitio donde se crea el valor (la línea de producción, el taller, el punto de servicio). Un "Gemba Walk" es el acto de ir a ese lugar a observar, con respeto y curiosidad.
El error de oficina: Analizar datos y diagramas de flujo desde tu escritorio, creyendo que entiendes la realidad del proceso.
La práctica del Ingeniero de Métodos:
Ve y Observa sin Juzgar: Pasa tiempo real en la planta. No hables, no interrumpas. Solo observa el flujo. ¿Dónde se detiene? ¿Dónde hay cuellos de botella? ¿Qué movimientos parecen innecesarios?
Aspectos clave para mejorar la eficiencia en envíos internacionales
Habla con los Operarios (en su terreno): La persona que realiza la tarea todos los días tiene un doctorado en ese proceso. Pregúntale: "¿Qué es lo más frustrante de tu trabajo? ¿Si tuvieras una varita mágica, qué cambiarías? ¿Por qué hacemos esto de esta manera?". Sus respuestas son oro puro.
Mapea el Flujo Real, no el Ideal: Usa herramientas como el Value Stream Mapping (VSM) o un simple diagrama de espagueti para dibujar el movimiento real de un producto o de una persona. Te sorprenderás de los kilómetros innecesarios que se recorren cada día.
Un día de observación atenta en el Gemba te dará más información valiosa que una semana analizando reportes.
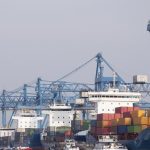
Secreto #2: Ataca los 8 Desperdicios del Lean como si Fueran tu Enemigo Público
La filosofía Lean Manufacturing nos regaló un marco de trabajo brillante para identificar ineficiencias. Memoriza estos 8 desperdicios (acrónimo DOWNTIME) y entrena tu ojo para detectarlos en todas partes:
TE PUEDE INTERESAR:
Defectos (Defects): Reprocesos, scrap, corrección de errores.
Overproducción (Overproduction): Producir más de lo que el cliente necesita en este momento. Es el peor de los desperdicios porque genera todos los demás.
Waiting (Esperas): Tiempo de inactividad de máquinas o personas esperando por material, instrucciones o una etapa anterior.
No Utilización del Talento (Non-Utilized Talent): No aprovechar las ideas, habilidades y creatividad de tu equipo.
Transporte (Transportation): Movimiento innecesario de materiales o productos.
Inventario (Inventory): Exceso de materia prima, producto en proceso o producto terminado. Oculta problemas y consume capital.
Movimiento (Motion): Movimiento innecesario de personas (agacharse, estirarse, caminar).
Exceso de Procesamiento (Extra-Processing): Realizar pasos que no añaden valor desde la perspectiva del cliente (ej. pulir una superficie que no se verá).
Mi táctica: En cada proceso que analices, pregúntate: "¿Qué tipo de desperdicio DOWNTIME veo aquí?". Ponerle un nombre al problema es el primer paso para eliminarlo.
Secreto #3: El Balanceo de Línea es el Corazón de un Flujo Continuo
El síntoma del desbalance: Ves a un operario corriendo para mantener el ritmo mientras que el siguiente en la línea está esperando con los brazos cruzados.
El objetivo: Lograr que el trabajo fluya a un ritmo constante (el "Takt Time"), distribuyendo las tareas de manera equitativa entre las estaciones de trabajo para que ninguna esté sobrecargada ni ociosa.
Mi enfoque práctico:
Mide el Tiempo de Ciclo de Cada Tarea: Desglosa el proceso en sus tareas más pequeñas y mide cuánto tiempo lleva cada una.
Calcula el Takt Time: Es el ritmo de la demanda del cliente. Se calcula como Tiempo de Producción Disponible / Demanda del Cliente. Este es el pulso al que tu línea debe latir.
Agrupa Tareas y Asigna a Estaciones: Combina las tareas de manera que el tiempo total de cada estación de trabajo sea lo más cercano posible (pero sin exceder) al Takt Time.
Experimenta y Ajusta: El balanceo de línea no es un cálculo estático. Implica rediseñar puestos de trabajo, crear ayudas visuales y formar a los operarios. La Calculadora de Balanceo de Líneas en este sitio es una excelente herramienta para empezar.
Un proceso balanceado es silencioso, fluido y predecible. El caos desaparece.
Conclusión
La optimización de procesos no es un proyecto con un inicio y un fin. Es una mentalidad de mejora continua (Kaizen). Las herramientas y técnicas son importantes, pero el verdadero "secreto" de un Ingeniero de Métodos eficaz es una curiosidad insaciable, un profundo respeto por las personas que hacen el trabajo y la perseverancia para cuestionar el status quo.
El proceso perfecto no existe. Pero la búsqueda de él es lo que impulsa a las mejores organizaciones del mundo. Y esa búsqueda empieza con un simple paseo por el Gemba.
Te Puede Interesar: