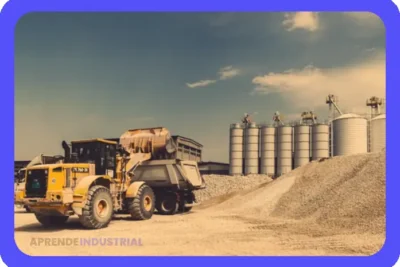
5 Modelos de Pedido & Modelo de Pedidos para Inventarios
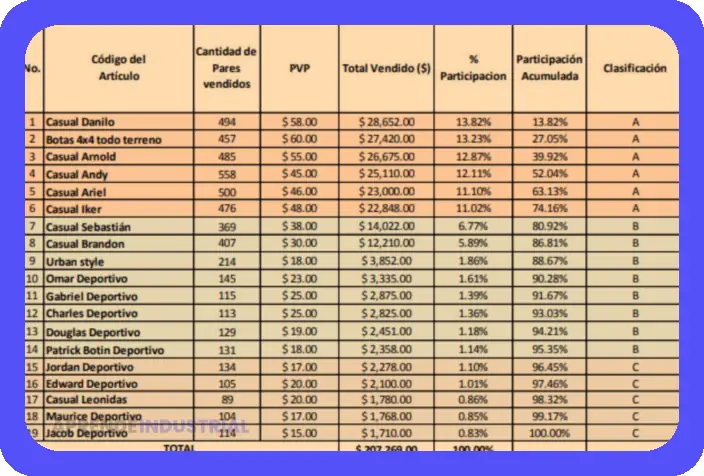
La gestión eficiente de inventarios es crucial para el éxito de cualquier empresa. Un sistema de modelos de pedido bien implementado puede marcar la diferencia entre el éxito y el fracaso, optimizando los costos, minimizando el riesgo de ruptura de stock y maximizando la rentabilidad. Este aspecto es fundamental para la competitividad en el mercado actual, donde la agilidad y la capacidad de respuesta a la demanda son elementos clave. La correcta selección y aplicación de un modelo de pedido está intrínsecamente ligado a la estrategia general de la empresa, incluyendo aspectos como la demanda del producto, el costo de almacenamiento, el costo de pedido y la velocidad de reposición.
Este artículo explorará en detalle los aspectos clave de la aplicación de diversos modelos de pedido dentro de una matriz de estrategia de inventarios. Analizaremos cinco modelos populares, describiendo sus características, fortalezas y debilidades, y su aplicación según las particularidades de cada producto o bien. Además, proporcionaremos herramientas y consideraciones para que puedas elegir el modelo de pedido que mejor se adapte a las necesidades específicas de tu negocio. Aprenderás a evaluar la eficiencia de cada modelo y a responder preguntas clave para una implementación exitosa.
- Los Cinco Modelos de Pedido para la Gestión de Inventarios
- Modelo s,Q (Cantidad Fija, Punto de Reorden)
- Modelo s,S (Punto de Reorden, Nivel de Inventario)
- Modelo R,S (Pedido Periódico, Nivel de Inventario)
- Modelo R,s,S (Pedido Periódico, Punto de Reorden, Nivel de Inventario)
- Modelo CPP (Cantidad Fija, Pedido Periódico)
- Matriz de Estrategia de Inventarios y Selección del Modelo de Pedido
- Evaluación de la Eficiencia de los Modelos de Pedido
- Implementación y Adaptación de los Modelos de Pedido
- Consideraciones Finales sobre la Elección de un Modelo de Pedido
- Conclusión
- Preguntas Frecuentes
Los Cinco Modelos de Pedido para la Gestión de Inventarios
Modelo de Pedido | Descripción | Ventajas | Desventajas |
---|---|---|---|
Sistema de Punto de Reorden (ROP) | Se basa en un nivel de inventario mínimo predefinido. Cuando el inventario alcanza este punto, se realiza un pedido de reposición de una cantidad fija. | Simple y fácil de implementar; adecuado para artículos de demanda estable. | Puede llevar a un exceso de inventario si la demanda fluctúa; no considera la incertidumbre de la demanda o el tiempo de entrega. |
Sistema de Reposición Continua (Just-in-Time o JIT) | Se enfoca en la entrega de materiales justo a tiempo para su uso en la producción, minimizando el inventario en mano. | Reduce los costos de almacenamiento y minimiza el riesgo de obsolescencia; mejora la eficiencia operativa. | Requiere una estrecha colaboración con los proveedores; susceptible a interrupciones en la cadena de suministro. |
Sistema de Reposición Periódica (Periodic Review) | El inventario se revisa en intervalos regulares (diarios, semanales, mensuales, etc.), y se realiza un pedido para llevar el inventario hasta un nivel de objetivo predefinido. | Reduce la frecuencia de los pedidos; puede ser más eficiente que el ROP para artículos con demandas variables. | Puede resultar en un inventario más alto que el ROP; requiere un sistema de seguimiento preciso. |
Sistema de Reposición Basado en la Demanda (Demand-Driven) | Los pedidos se basan en la demanda real de los productos, utilizando pronósticos precisos y datos históricos de ventas. | Optimiza los niveles de inventario; reduce el riesgo de exceso o escasez. | Requiere datos de demanda precisos y un sistema de pronóstico sofisticado; puede ser complejo de implementar. |
Sistema de Reposición MRP (Material Requirements Planning) | Un sistema de planificación de materiales que utiliza una lista de materiales (BOM) para calcular las necesidades de materiales para la producción y generar planes de pedido. | Planifica eficientemente las necesidades de materiales; ayuda a evitar cuellos de botella en la producción. | Requiere datos precisos de la lista de materiales, inventarios y programa de producción; puede ser complejo de implementar y mantener. |
Empezaremos por analizar los cinco modelos de pedido para la gestión de inventarios: s,Q; s,S; R,S; R,s,S; y CPP. Cada uno tiene su propia lógica y se adapta a diferentes contextos. La elección del modelo de pedido ideal depende de factores como la demanda, la variabilidad, el costo de almacenamiento y el costo de realizar un pedido.
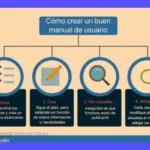
El primer paso para una buena gestión de inventarios es comprender los diferentes modelos de pedido disponibles. Un modelo inadecuado puede resultar en costos excesivos de almacenamiento o en rupturas de stock. Este análisis te ayudará a tomar una decisión informada.
Modelo s,Q (Cantidad Fija, Punto de Reorden)
Semana | Inventario al Final de la Semana | Demanda Semanal | Pedidos Realizados | Cantidad Pedida |
---|---|---|---|---|
1 | 100 | 20 | Sí | 100 |
2 | 80 | 15 | No | 0 |
3 | 65 | 25 | No | 0 |
4 | 40 | 18 | Sí | 100 |
5 | 122 | 22 | No | 0 |
6 | 100 | 20 | No | 0 |
7 | 80 | 25 | No | 0 |
8 | 55 | 15 | Sí | 100 |
9 | 140 | 30 | No | 0 |
10 | 110 | 10 | No | 0 |
Este modelo de pedido es uno de los más simples y ampliamente utilizados. Cuando el inventario disponible baja hasta un nivel de reorden (s), se realiza un pedido de una cantidad fija (Q). Es simple de implementar y requiere pocos cálculos, ideal para artículos con demanda estable y predecible. Sin embargo, puede generar un exceso de inventario si la demanda fluctúa. La cantidad de pedido (Q) se calcula generalmente utilizando formulas que consideran la demanda anual, el costo de pedido y el costo de almacenamiento.
Por ejemplo, si 's' es 100 unidades y 'Q' es 500, se realizará un pedido de 500 unidades cada vez que el inventario caiga a 100 unidades. Este modelo de pedido es efectivo para artículos con demanda relativamente estable y costos de almacenamiento bajos. El cálculo de Q optimiza el costo total considerando los costos de pedido y mantenimiento de inventario.
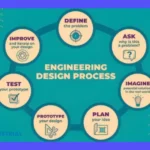
Para determinar el valor óptimo de Q, podemos utilizar la fórmula de Wilson: Q = √(2DS/H), donde D es la demanda anual, S es el costo de realizar un pedido y H es el costo de mantener una unidad en inventario durante un año. Este cálculo nos ayuda a encontrar el punto de equilibrio entre los costos de pedido y los de almacenamiento.
Modelo s,S (Punto de Reorden, Nivel de Inventario)
Semana | Inventario al inicio de la semana | Demanda semanal | Inventario al final de la semana | Pedido (si aplica) | Cantidad Pedida |
---|---|---|---|---|---|
1 | 100 | 25 | 75 | Sí | 50 |
2 | 125 | 30 | 95 | No | 0 |
3 | 95 | 20 | 75 | No | 0 |
4 | 75 | 35 | 40 | Sí | 60 |
5 | 100 | 28 | 72 | No | 0 |
6 | 72 | 32 | 40 | Sí | 60 |
7 | 100 | 22 | 78 | No | 0 |
En este modelo de pedido, se realiza un pedido variable para alcanzar un nivel de inventario deseado (S) cada vez que el inventario baja al punto de reorden (s). La cantidad pedida es, por lo tanto, S-s. Este modelo de pedido se adapta mejor a situaciones donde la demanda es más variable. Nos permite mantener un stock de seguridad, minimizando el riesgo de ruptura de stock, incluso con fluctuaciones en la demanda.
Imaginemos un escenario donde 's' es 50 unidades y 'S' es 200. Cuando el inventario disponible llega a 50 unidades, se realiza un pedido de 150 unidades (200 - 50) para llevar el inventario al nivel deseado de 200 unidades. Este modelo es más complejo que el s,Q, pero ofrece mayor flexibilidad para gestionar la incertidumbre en la demanda.
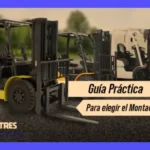
Modelo R,S (Pedido Periódico, Nivel de Inventario)
Este modelo de pedido se basa en la revisión periódica del inventario a intervalos regulares de tiempo (R). En cada revisión, se realiza un pedido para alcanzar un nivel de inventario deseado (S). Este método es útil cuando se gestionan varios artículos simultáneamente, ya que simplifica la logística de los pedidos.
Por ejemplo, si R es de 1 semana y S es 100 unidades, se revisa el inventario cada semana y se realiza un pedido para llegar a 100 unidades. Independientemente del nivel de inventario, el pedido se realiza periódicamente. Esto puede ser más eficiente para artículos con demandas menores o con un proceso de pedido complejo.
Modelo R,s,S (Pedido Periódico, Punto de Reorden, Nivel de Inventario)
Este modelo de pedido combina los dos anteriores. Se revisa el inventario a intervalos regulares (R), pero solo se realiza un pedido si el inventario es inferior al punto de reorden (s). El pedido se calcula para llegar al nivel de inventario deseado (S). Este modelo reduce el número de pedidos y permite gestionar la demanda variable de forma efectiva.
Este modelo ofrece una buena combinación entre la periodicidad de los pedidos (R) y la gestión de seguridad del stock (s,S). Es una solución más robusta para situaciones donde se necesita flexibilidad y control.
Modelo CPP (Cantidad Fija, Pedido Periódico)
Este modelo de pedido es el más sencillo, ordenando una cantidad fija 'Q' a intervalos fijos de tiempo. La simplicidad de este sistema es su principal ventaja. Sin embargo, no considera las fluctuaciones de demanda ni los niveles de stock. Es adecuado para artículos con demanda constante y predecible, donde los errores en la previsión no tienen un impacto significativo en los costos.
Si 'Q' es 1000 unidades y el intervalo es 1 mes, se ordenan 1000 unidades cada mes, independientemente del nivel de inventario actual. Este modelo de pedido es de fácil gestión, pero su rigidez puede ser una desventaja en situaciones con demanda inestable.
Matriz de Estrategia de Inventarios y Selección del Modelo de Pedido
La elección del modelo de pedido adecuado no debe hacerse de forma aislada. Es esencial integrarlo con una matriz de estrategia de inventarios. Esta matriz considera factores críticos como la demanda (previsible o impredecible), el valor del artículo (alto o bajo) y la importancia estratégica del artículo para el negocio.
Esta matriz clasifica los artículos en diferentes categorías, cada una con sus propios requisitos de gestión de inventario. Por ejemplo, artículos con demanda alta y previsible se gestionan de forma distinta a aquellos con demanda baja e impredecible. La matriz guía la selección del modelo de pedido más adecuado para cada categoría de producto.
Evaluación de la Eficiencia de los Modelos de Pedido
Una vez implementado un modelo de pedido, es fundamental evaluarlo regularmente para verificar su eficiencia. Hay varias métricas clave que ayudan a esta evaluación, incluyendo los niveles de inventario, la tasa de ruptura de stock, el costo de almacenamiento y el costo total de gestión de inventario. De esta manera, se asegura que la estrategia implementada sigue siendo la más adecuada.
Implementación y Adaptación de los Modelos de Pedido
La implementación de cualquier modelo de pedido requiere una planificación cuidadosa. Se deben considerar varios aspectos como la disponibilidad de datos precisos sobre la demanda, la capacidad de previsión, la infraestructura de software y la formación del personal. Es importante entender que un modelo de pedido no es una solución estática; debe adaptarse y ajustarse con el tiempo según la evolución de la demanda y las condiciones del mercado.
Consideraciones Finales sobre la Elección de un Modelo de Pedido
La selección del mejor modelo de pedido requiere un análisis cuidadoso de las necesidades específicas de la empresa. No hay un modelo universalmente óptimo; la mejor opción dependerá de los factores mencionados anteriormente, incluyendo la variabilidad de la demanda, la importancia del artículo, el costo de almacenamiento y el costo de pedido. Un análisis detallado de estos factores ayudará a la toma de decisiones informadas sobre la selección del modelo de pedido.
Conclusión
La correcta selección y aplicación de un modelo de pedido es fundamental para la eficiente gestión de inventarios. Los cinco modelos discutidos—s,Q, s,S, R,S, R,s,S y CPP—ofrecen diferentes enfoques, cada uno con sus propias ventajas y desventajas. La clave está en comprender las características de cada modelo y, usando una matriz de estrategia de inventarios, determinar cuál se adapta mejor a las necesidades específicas de tu empresa. Recuerda que la elección del modelo de pedido no es un proceso estático, sino un proceso dinámico que debe revisarse y ajustarse periódicamente para asegurar la optimización de los costos y la satisfacción de la demanda. Una buena implementación de un modelo de pedido puede significar la diferencia entre una gestión exitosa y una gestión ineficiente de tus recursos.
El éxito de la gestión de inventarios se basa en la correcta elección y aplicación del modelo de pedido más adecuado, optimizando el equilibrio entre la disponibilidad de productos, los costos de almacenamiento y los costos de pedido.
Preguntas Frecuentes
¿Cuál es el mejor modelo de pedido para una pequeña empresa?
Depende de la complejidad y variabilidad de sus productos. Para artículos simples, el modelo s,Q puede ser suficiente.
¿Cómo se calcula el punto de reorden (s)?
El cálculo de 's' depende del tiempo de entrega del proveedor y de la demanda diaria. Se suele agregar un stock de seguridad para cubrir la incertidumbre.
¿Qué sucede si la demanda cambia drásticamente?
Es necesario reevaluar y ajustar los parámetros del modelo de pedido seleccionado, considerando el uso de modelos más robustos ante la incertidumbre.
¿Puedo utilizar diferentes modelos de pedido para distintos productos?
Sí, es común utilizar distintos modelos de pedido según las características específicas de cada producto.
¿Qué software me ayuda a gestionar los modelos de pedido?
Existen numerosos sistemas de gestión de inventario (ERP, WMS) que pueden ayudar a implementar y gestionar los distintos modelos de pedido.
Deja una respuesta
Te Puede Interesar: