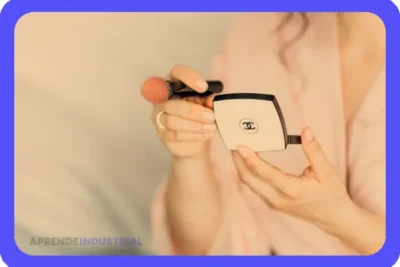
Mejora continua: Capacidad y control estadístico de procesos
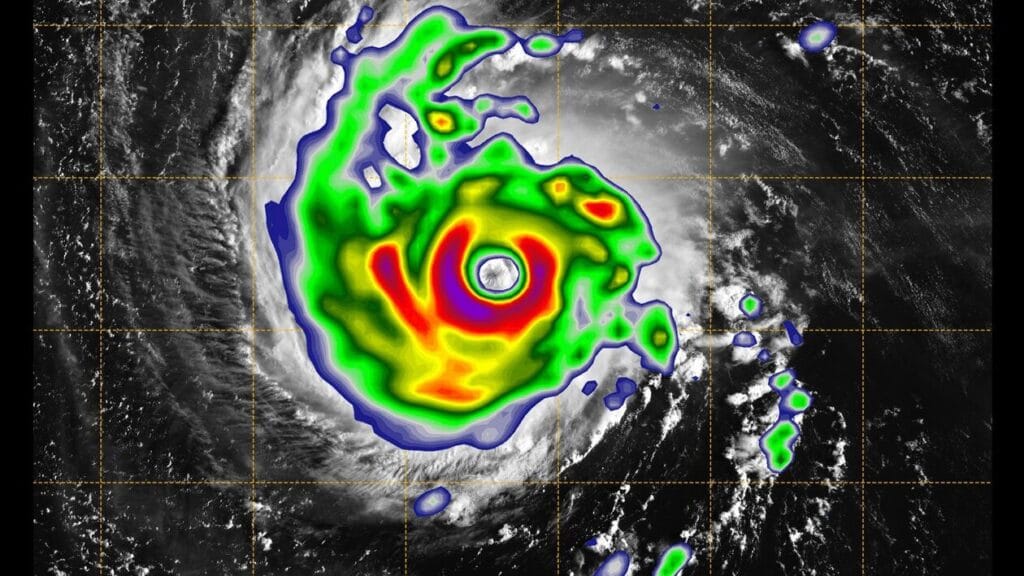
La mejora continua es un concepto fundamental en la ingeniería industrial que busca optimizar procesos, productos y servicios de manera constante. En este contexto, la capacidad de procesos y el control estadístico se presentan como herramientas esenciales para garantizar que los procesos cumplan con las especificaciones requeridas y, al mismo tiempo, se mantengan dentro de los límites de calidad establecidos. Estas herramientas no solo permiten identificar áreas de mejora, sino que también ayudan a prevenir problemas antes de que ocurran, lo que resulta en una mayor eficiencia y satisfacción del cliente.
Este artículo tiene como objetivo explorar en profundidad la capacidad y el control estadístico de procesos, proporcionando una guía completa sobre sus características, beneficios y aplicaciones en la ingeniería industrial. A lo largo del texto, se presentarán ejemplos matemáticos, tablas y listas de verificación que facilitarán la comprensión de estos conceptos. Además, se invitará a los lectores a reflexionar sobre la importancia de implementar estas herramientas en sus propios entornos laborales.
Características de la Capacidad de Procesos
La capacidad de procesos se refiere a la habilidad de un proceso para producir resultados que cumplan con las especificaciones establecidas. Esta capacidad se mide a través de varios índices, como Cp, Cpk, Pp y Ppk, que permiten evaluar la variabilidad y el centrado del proceso. Un proceso con alta capacidad es aquel que produce productos dentro de las tolerancias especificadas, mientras que un proceso con baja capacidad puede generar productos defectuosos o fuera de especificación.
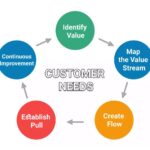
Una de las características más importantes de la capacidad de procesos es su relación con la variabilidad. La variabilidad puede ser causada por múltiples factores, como la materia prima, el equipo utilizado, las condiciones ambientales y la intervención humana. Por lo tanto, es crucial identificar y controlar estas fuentes de variabilidad para mejorar la capacidad del proceso. La implementación de técnicas de control estadístico puede ayudar a monitorear y reducir la variabilidad, lo que a su vez mejora la capacidad del proceso.
Además, la capacidad de procesos no es estática; puede cambiar con el tiempo debido a factores internos y externos. Por esta razón, es fundamental realizar evaluaciones periódicas de la capacidad del proceso para asegurarse de que se mantenga dentro de los límites aceptables. Esto implica la recolección y análisis de datos, así como la implementación de acciones correctivas cuando sea necesario.
Beneficios del Control Estadístico de Procesos
El control estadístico de procesos (CEP) es una metodología que utiliza herramientas estadísticas para monitorear y controlar un proceso. Uno de los principales beneficios del CEP es la capacidad de detectar variaciones en el proceso antes de que se conviertan en problemas significativos. Esto permite a las organizaciones tomar medidas proactivas para corregir desviaciones y mantener la calidad del producto.

Otro beneficio importante del CEP es la mejora en la eficiencia operativa. Al identificar y eliminar fuentes de variabilidad, las organizaciones pueden reducir el desperdicio y optimizar el uso de recursos. Esto no solo se traduce en ahorros de costos, sino que también contribuye a una mayor satisfacción del cliente al garantizar productos de alta calidad.
Además, el CEP fomenta una cultura de mejora continua dentro de la organización. Al involucrar a los empleados en el monitoreo y análisis de procesos, se promueve un sentido de responsabilidad y compromiso con la calidad. Esto puede llevar a una mayor innovación y a la implementación de mejores prácticas en toda la organización.
Indicadores de Capacidad de Procesos
Existen varios indicadores que se utilizan para medir la capacidad de un proceso. Entre los más comunes se encuentran Cp, Cpk, Pp y Ppk. Cada uno de estos índices proporciona información valiosa sobre la capacidad del proceso y su rendimiento.

Cp y Cpk
El índice Cp mide la capacidad potencial de un proceso, es decir, la capacidad del proceso para producir resultados dentro de las especificaciones si el proceso está centrado. Se calcula utilizando la siguiente fórmula:
Cp = (USL - LSL) / (6 * σ)
Donde:
- USL es el límite superior de especificación.
- LSL es el límite inferior de especificación.
- σ es la desviación estándar del proceso.
Por otro lado, el índice Cpk mide la capacidad real del proceso, teniendo en cuenta su centrado. Se calcula de la siguiente manera:
Cpk = min[(USL - μ) / (3 * σ), (μ - LSL) / (3 * σ)]
Donde:
- μ es la media del proceso.
Un Cp o Cpk mayor a 1.33 generalmente indica que el proceso es capaz de cumplir con las especificaciones, mientras que un valor menor a 1 sugiere que el proceso necesita mejoras.
Pp y Ppk
Los índices Pp y Ppk son similares a Cp y Cpk, pero se utilizan para evaluar la capacidad de procesos a partir de datos de producción en lugar de datos de muestra. El índice Pp se calcula de la siguiente manera:
Pp = (USL - LSL) / (6 * σ)
Y el índice Ppk se calcula como:
Ppk = min[(USL - μ) / (3 * σ), (μ - LSL) / (3 * σ)]
Estos índices son útiles para evaluar la capacidad de procesos en situaciones donde se dispone de datos históricos o cuando se está en la fase de producción.
Métodos de Evaluación de Capacidad
La evaluación de la capacidad de un proceso puede realizarse mediante diferentes métodos, cada uno con sus propias ventajas y desventajas. Algunos de los métodos más comunes incluyen el análisis de histogramas, el uso de gráficos de control y el cálculo de índices de capacidad.
Análisis de Histogramas
El análisis de histogramas es una técnica visual que permite observar la distribución de los datos de un proceso. Al crear un histograma, se pueden identificar patrones, tendencias y la variabilidad del proceso. Esto es especialmente útil para detectar problemas de calidad y áreas de mejora.
Para crear un histograma, se deben seguir los siguientes pasos:
- Recolectar datos del proceso.
- Dividir el rango de datos en intervalos (bins).
- Contar la frecuencia de datos en cada intervalo.
- Graficar los intervalos en el eje horizontal y las frecuencias en el eje vertical.
Un histograma bien diseñado puede proporcionar información valiosa sobre la capacidad del proceso y ayudar a identificar si el proceso está centrado y dentro de las especificaciones.
Gráficos de Control
Los gráficos de control son herramientas estadísticas que permiten monitorear un proceso a lo largo del tiempo. Estos gráficos muestran la variabilidad del proceso y ayudan a identificar si el proceso está bajo control o si hay señales de problemas. Un gráfico de control típico incluye una línea central que representa la media del proceso, así como líneas de control superior e inferior que representan los límites de control.
Para construir un gráfico de control, se deben seguir estos pasos:
- Recolectar datos del proceso en intervalos regulares.
- Calcular la media y la desviación estándar de los datos.
- Establecer los límites de control superior e inferior.
- Graficar los datos en el tiempo y agregar las líneas de control.
Los gráficos de control son una herramienta poderosa para la mejora continua, ya que permiten a los equipos de trabajo identificar rápidamente cualquier desviación del proceso y tomar medidas correctivas.
Ejemplos Matemáticos de Capacidad de Procesos
Para ilustrar cómo se aplican los conceptos de capacidad de procesos, a continuación se presentan algunos ejemplos matemáticos resueltos paso a paso.
Ejemplo 1: Cálculo de Cp y Cpk
Supongamos que un proceso de fabricación tiene los siguientes datos:
- Límite superior de especificación (USL): 10
- Límite inferior de especificación (LSL): 6
- Media del proceso (μ): 8
- Desviación estándar (σ): 0.5
Para calcular Cp y Cpk, utilizamos las fórmulas mencionadas anteriormente.
- Calcular Cp:
Cp = (USL - LSL) / (6 * σ) = (10 - 6) / (6 * 0.5) = 4 / 3 = 1.33
- Calcular Cpk:
Cpk = min[(USL - μ) / (3 * σ), (μ - LSL) / (3 * σ)]
Cpk = min[(10 - 8) / (3 * 0.5), (8 - 6) / (3 * 0.5)]
Cpk = min[2 / 1.5, 2 / 1.5] = min[1.33, 1.33] = 1.33
En este caso, tanto Cp como Cpk son iguales a 1.33, lo que indica que el proceso es capaz de cumplir con las especificaciones.
Ejemplo 2: Cálculo de Pp y Ppk
Ahora consideremos un proceso con los siguientes datos:
- Límite superior de especificación (USL): 15
- Límite inferior de especificación (LSL): 10
- Media del proceso (μ): 12
- Desviación estándar (σ): 1.2
Para calcular Pp y Ppk, utilizamos las fórmulas correspondientes.
- Calcular Pp:
Pp = (USL - LSL) / (6 * σ) = (15 - 10) / (6 * 1.2) = 5 / 7.2 = 0.694
- Calcular Ppk:
Ppk = min[(USL - μ) / (3 * σ), (μ - LSL) / (3 * σ)]
Ppk = min[(15 - 12) / (3 * 1.2), (12 - 10) / (3 * 1.2)]
Ppk = min[3 / 3.6, 2 / 3.6] = min[0.833, 0.556] = 0.556
En este caso, Pp es 0.694 y Ppk es 0.556, lo que indica que el proceso no es capaz de cumplir con las especificaciones.
Implementación de Herramientas de Mejora Continua
La implementación de herramientas de mejora continua, como la capacidad y el control estadístico de procesos, requiere un enfoque sistemático. A continuación, se presentan algunos pasos clave para llevar a cabo esta implementación.
Paso 1: Capacitación del Personal
La capacitación del personal es fundamental para el éxito de la implementación de herramientas de mejora continua. Los empleados deben comprender los conceptos de capacidad de procesos y control estadístico, así como las herramientas y técnicas asociadas. Esto puede incluir talleres, cursos en línea y sesiones de formación práctica.
Paso 2: Recolección de Datos
La recolección de datos es un paso crítico en el proceso de mejora continua. Se deben establecer procedimientos para recolectar datos de manera sistemática y consistente. Esto puede incluir la utilización de hojas de control, software de gestión de calidad y sistemas de monitoreo en tiempo real.
Paso 3: Análisis de Datos
Una vez que se han recolectado los datos, es necesario analizarlos para identificar tendencias, patrones y áreas de mejora. Esto puede implicar el uso de herramientas estadísticas, como gráficos de control, histogramas y análisis de capacidad. El análisis de datos debe ser un proceso continuo para garantizar que se mantenga la calidad del proceso.
Conclusión
La mejora continua a través de la capacidad y el control estadístico de procesos es esencial para garantizar la calidad y eficiencia en la ingeniería industrial. Estas herramientas permiten a las organizaciones evaluar su rendimiento, identificar áreas de mejora y tomar decisiones informadas para optimizar sus procesos.
La implementación de estas herramientas no solo mejora la calidad del producto, sino que también fomenta una cultura de mejora continua dentro de la organización. Al capacitar al personal, recolectar y analizar datos de manera sistemática, las empresas pueden mantenerse competitivas en un entorno en constante cambio.
La capacidad y el control estadístico de procesos son herramientas poderosas que, cuando se utilizan correctamente, pueden llevar a una mejora significativa en la calidad y eficiencia de los procesos industriales. Se invita a los lectores a reflexionar sobre la importancia de estas herramientas en su propio trabajo y a considerar su implementación en sus organizaciones.
Referencias
Deja una respuesta
Te Puede Interesar: