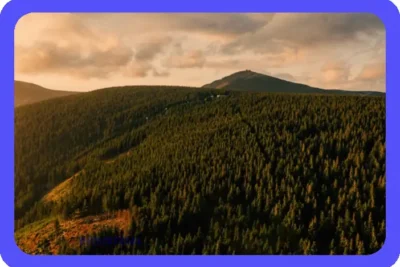
Cómo aplicar Lean Manufacturing en español: Guía práctica
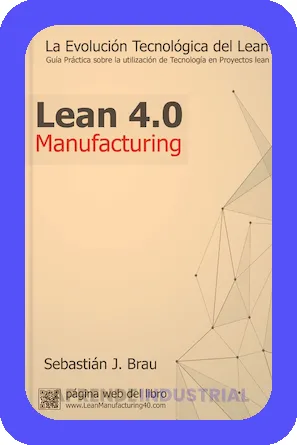
La metodología lean manufacturing es un enfoque revolucionario en la gestión de la producción que ha transformado la manera en que las empresas operan en todo el mundo. Se centra en la eliminación de desperdicios (muda) en todos los procesos, desde el diseño hasta la entrega al cliente. Esta filosofía, originada en Toyota, prioriza la eficiencia, la calidad y la satisfacción del cliente por encima de todo. La implementación de lean manufacturing requiere un cambio cultural significativo dentro de la organización, fomentando la participación activa de todos los empleados en la búsqueda constante de mejoras. El resultado final es un aumento significativo en la rentabilidad, una reducción en los costos operativos y una mejora en la competitividad del mercado.
Este artículo explorará en detalle los aspectos clave de la metodología lean manufacturing, proporcionando una guía práctica para su implementación. Analizaremos los siete tipos de desperdicios, las herramientas lean más importantes y los pasos necesarios para integrar con éxito lean manufacturing en cualquier tipo de organización. Aprenderemos cómo identificar y eliminar los desperdicios, optimizar los procesos y crear un flujo de trabajo más eficiente. Se presentarán ejemplos reales, estudios de caso y consejos prácticos para facilitar la comprensión y la aplicación de esta valiosa metodología de gestión.
Los 7 Desperdicios (Muda) en Lean Manufacturing
La filosofía lean manufacturing se centra en la identificación y eliminación de los siete tipos de desperdicios, conocidos como "muda" en japonés. Estos desperdicios son las actividades que no añaden valor al producto o servicio desde la perspectiva del cliente. Identificar y eliminarlos es fundamental para la optimización de los procesos y el aumento de la eficiencia. Los siete desperdicios son:
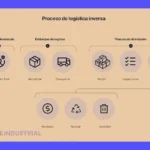
Sobreproducción
La sobreproducción es la creación de bienes o servicios antes de que sean necesarios. Esto lleva a un aumento de los costos de almacenamiento, a la obsolescencia de los productos y a la posibilidad de que los productos terminados no satisfagan la demanda real del mercado. Por ejemplo, producir 1000 unidades de un producto cuando solo se requieren 500 genera 500 unidades de desperdicio. La solución pasa por producir solo lo que se necesita, en el momento que se necesita, con la cantidad que se necesita, siguiendo un sistema de producción “justo a tiempo”.
Tiempo de Espera
El tiempo de espera se refiere al tiempo que los materiales, los productos o los empleados permanecen inactivos, esperando que el siguiente paso del proceso se complete. Este tiempo no agrega valor alguno y representa un costo significativo para la empresa. Ejemplo: Un empleado que espera a que llegue una pieza para poder continuar con su trabajo. Minimizar el tiempo de espera implica una planificación exhaustiva, optimizando los flujos de trabajo y la comunicación entre los diferentes departamentos.
Transporte
El transporte innecesario de materiales o productos representa un desperdicio de tiempo, recursos y energía. Mover materiales de un lugar a otro sin una necesidad justificada genera costos adicionales y aumenta la probabilidad de daños o pérdidas. Ejemplo: Mover componentes entre diferentes departamentos sin necesidad implica coste y tiempo extra. La solución consiste en organizar el espacio de trabajo de forma eficiente, acortando las distancias y utilizando sistemas de transporte apropiados.
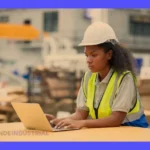
Movimiento
Los movimientos innecesarios de los empleados o las máquinas también constituyen un desperdicio. Esto incluye movimientos repetitivos o ineficientes que no añaden valor al producto. Por ejemplo: Un trabajador que debe caminar largas distancias para conseguir materiales. La optimización del diseño de puestos de trabajo es primordial para reducir los movimientos innecesarios y aumentar la productividad.
Inventario
El inventario excesivo representa un gran desperdicio, incluyendo costos de almacenamiento, el riesgo de obsolescencia o deterioro de los materiales y la dificultad para gestionar un gran volumen de existencias. Mantener grandes stocks no implica mayor eficiencia ni productividad, es más, puede perjudicar la gestión del espacio y añadir complicaciones innecesarias. El objetivo del lean manufacturing es reducir el inventario al mínimo necesario para satisfacer la demanda.
Sobreprocesamiento
El sobreprocesamiento implica realizar más trabajo del necesario para satisfacer las necesidades del cliente. Esto puede incluir el uso de maquinaria sofisticada y compleja cuando una solución más simple sería suficiente, o añadir características innecesarias al producto. Por ejemplo: Usar una máquina CNC para un proceso que podría hacerse manualmene. En este caso, la clave es eliminar pasos innecesarios que no añaden valor al producto.
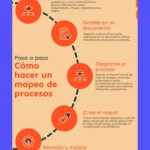
Defectos
Los defectos en la producción representan un enorme desperdicio, incluyendo los costos de reparación o reemplazo de los productos defectuosos, el tiempo perdido en la detección y corrección de los errores y la potencial pérdida de clientes insatisfechos. Ejemplo: Un producto defectuoso que debe ser desechado implica una gran pérdida de materia prima, tiempo y recursos. La prevención de defectos es fundamental para una producción eficiente.
Herramientas Lean Manufacturing para la Mejora Continua
La implementación de lean manufacturing se basa en el uso de diversas herramientas que facilitan la identificación y eliminación de los desperdicios. Algunas de las más importantes son:
5S
El 5S es una metodología para organizar el lugar de trabajo de forma eficiente y segura. Las cinco "S" son: Seiri (clasificación), Seiton (orden), Seisō (limpieza), Seiketsu (estandarización) y Shitsuke (disciplina). Implementar el 5S crea un ambiente de trabajo más organizado, seguro y eficiente, lo que se traduce en una mejora de la productividad.
Kaizen
Kaizen significa "mejora continua" en japonés. Esta filosofía promueve la participación activa de todos los empleados en la búsqueda constante de mejoras en los procesos. Se basa en la realización de pequeñas mejoras continuas, en lugar de grandes cambios repentinos, lo que se traduce en una optimización constante de los procesos.
Value Stream Mapping (VSM)
El Value Stream Mapping (Mapeo del Flujo de Valor) es una herramienta visual que permite representar gráficamente el flujo de materiales e información en un proceso. Ayuda a identificar los pasos que no agregan valor y a encontrar oportunidades de mejora. Esto permite visualizar los procesos de forma más clara y sencilla, identificando cuellos de botella y áreas de mejora.
Kanban
Kanban es un sistema de gestión visual que se utiliza para controlar el flujo de trabajo. Se basa en el uso de tarjetas o señales para indicar la demanda de materiales o productos. Kanban ayuda a evitar la sobreproducción y a mantener el inventario bajo control.
Poka-Yoke
Poka-Yoke, que significa “a prueba de errores” en japonés, es una metodología para diseñar procesos que eviten la ocurrencia de errores humanos. Esto se logra mediante la implementación de mecanismos que impidan la realización de acciones incorrectas.
Implementación de Lean Manufacturing: Un Enfoque Paso a Paso
La implementación de lean manufacturing requiere un enfoque sistemático y una estrategia clara. El proceso debe ser gradual y participativo, involucrando a todos los empleados de la organización. Aquí hay algunos pasos clave para la implementación exitosa de lean manufacturing:
- Formación: Es fundamental capacitar a los empleados sobre los principios y herramientas de lean manufacturing.
- Identificación de los desperdicios: Se debe realizar un análisis exhaustivo de los procesos para identificar los siete desperdicios (muda).
- Mapeo del flujo de valor: El mapeo del flujo de valor (VSM) es crucial para visualizar los procesos y identificar áreas de mejora.
- Implementación de mejoras: Se deben implementar las mejoras identificadas, priorizando aquellas que generen un mayor impacto.
- Seguimiento y medición: Es importante monitorear el progreso y medir el impacto de las mejoras implementadas.
- Mejora continua (Kaizen): La mejora continua es fundamental para mantener la eficiencia y la competitividad.
Casos de Éxito de Lean Manufacturing
Muchas empresas de todo el mundo han logrado implementar con éxito lean manufacturing, obteniendo resultados notables en términos de reducción de costos, mejora de la calidad y aumento de la productividad. Algunos ejemplos incluyen Toyota, que fue pionera en la filosofía lean, y otras empresas que han adaptado los principios lean a sus propias operaciones, adaptándolas a sus procesos y logrando reducir significativamente los tiempos de entrega y los costos de producción.
Conclusión
La metodología lean manufacturing ofrece una estrategia poderosa para optimizar procesos, mejorar la calidad y aumentar la rentabilidad. Eliminando los siete desperdicios (muda), las empresas pueden lograr una mayor eficiencia, mejorar la satisfacción del cliente y ganar una ventaja competitiva. La implementación exitosa de lean manufacturing requiere un enfoque sistemático, la participación activa de los empleados y un compromiso con la mejora continua. A través de herramientas como el 5S, Kaizen, y el Value Stream Mapping, las empresas pueden transformarse radicalmente, obteniendo resultados positivos a largo plazo. Recordemos que la metodología lean manufacturing no es solo una serie de técnicas, sino un cambio de mentalidad que prioriza el valor para el cliente y la eliminación de todo lo que no lo aporte.
Preguntas Frecuentes
¿Qué es el desperdicio (muda) en Lean Manufacturing?
El desperdicio (muda) en lean manufacturing son actividades que no añaden valor para el cliente y deben eliminarse para optimizar procesos.
¿Cuáles son las herramientas principales de Lean Manufacturing?
Las principales herramientas son 5S, Kaizen, Value Stream Mapping, Kanban y Poka-Yoke, entre otras.
¿Cómo se implementa Lean Manufacturing en una empresa?
La implementación implica formación, identificación de desperdicios, mapeo del flujo de valor e implementación de mejoras.
¿Qué beneficios aporta la metodología Lean Manufacturing?
Beneficios incluyen la reducción de costos, mejora de la calidad, aumento de la eficiencia y mayor satisfacción del cliente.
¿Es aplicable Lean Manufacturing a todas las industrias?
Sí, los principios lean son aplicables a cualquier industria, aunque la implementación requiere adaptación al contexto específico.
Deja una respuesta
Te Puede Interesar: