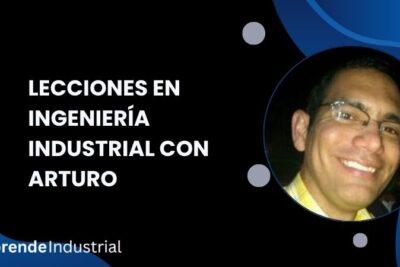
Descubre el Fascinante Origen de la Ingeniería Industrial: De la Revolución Industrial a la Era Digital
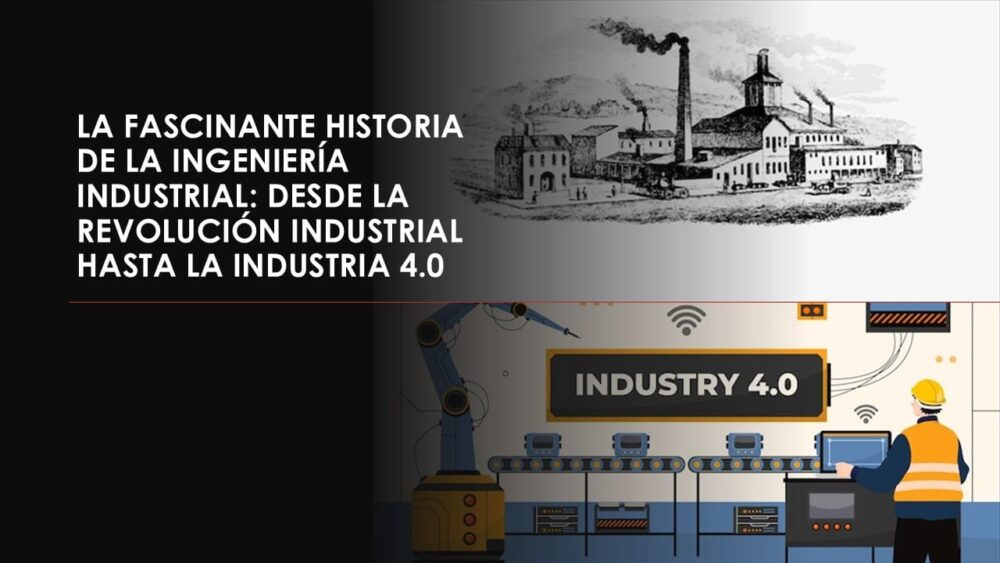
[quiz-cat id="2873"]
¿Alguna vez te has preguntado cómo los productos llegan tan eficientemente a tus manos, o cómo las empresas logran una productividad asombrosa? Detrás de esa aparente simplicidad se encuentra la Ingeniería Industrial, una disciplina clave dedicada a la optimización de procesos y sistemas, abarcando desde la producción hasta la gestión de recursos. Su objetivo principal es mejorar la eficiencia y productividad de las organizaciones, utilizando principios de matemáticas, física, estadística y ciencias sociales.
Desde la Revolución Industrial, esta rama de la ingeniería ha sido fundamental para el desarrollo de la sociedad moderna, impactando la forma en que producimos bienes y servicios. En este artículo, no solo exploraremos la rica historia de la ingeniería industrial y su evolución, sino que también desvelaremos el papel crucial de sus pioneros, su adaptación en el siglo XX y cómo se reinventa constantemente para abrazar los desafíos de la era digital, incluyendo la automatización, la inteligencia artificial y la sostenibilidad.
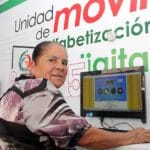
- Origen y Raíces de la Ingeniería Industrial
- Pioneros Fundacionales (Siglo XIX - XX)
- La Evolución de la Ingeniería Industrial en el Siglo XX
- Tabla de Contenidos:
- Origen y Raíces de la Ingeniería Industrial
- Figuras Claves en los Orígenes de la Ingeniería Industrial
- Pioneros Fundacionales (Siglo XIX - XX)
- La Evolución de la Ingeniería Industrial en el Siglo XX
- Resumen de la Evolución Histórica de la Ingeniería Industrial
- Hitos Importantes en la Historia Reciente y la Evolución de la Ingeniería Industrial hasta la Actualidad
- Desarrollo Académico de la Ingeniería Industrial
- Impacto en Diferentes Industrias
- Herramientas y Metodologías Clave
- Adaptación a la Era Digital en el Siglo XXI
- Industria 4.0 y su Impacto en la Ingeniería Industrial
- El Futuro de la Ingeniería Industrial
- Tendencias Clave en la Ingeniería Industrial Actual
- Innovación en Sostenibilidad
- Desafíos y Oportunidades
- Conclusión
- Preguntas frecuentes
Origen y Raíces de la Ingeniería Industrial
Revolución Industrial y su impacto
La Revolución Industrial, que comenzó en el siglo XVIII, marcó el inicio de una era de cambios sin precedentes en la producción y la sociedad. Este período se caracterizó por:
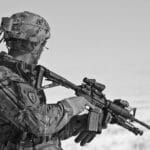
- La introducción de maquinaria avanzada.
- El surgimiento de fábricas como nuevos centros de producción.
- La transición de la producción artesanal a la producción en masa.
Esta transformación no solo afectó la forma en que se producían los bienes, sino también la organización del trabajo y la estructura de la sociedad. Antes, la producción se realizaba principalmente de forma artesanal, con métodos lentos y poco eficientes. La introducción de maquinaria, como la máquina de vapor y el telar mecánico, permitió aumentar drásticamente la velocidad y el volumen de producción, dando origen a la producción en masa. El surgimiento de grandes fábricas concentró a los trabajadores, lo que planteó nuevos desafíos en términos de coordinación y gestión.
Los Retos de la Producción en Masa que Impulsaron la Ingeniería Industrial
La producción en masa trajo consigo nuevos y complejos desafíos, creando la necesidad imperante de mejorar la eficiencia y la productividad en las fábricas. Los métodos de trabajo tradicionales resultaron insuficientes para hacer frente a la complejidad de las nuevas operaciones. Esto creó la urgencia de desarrollar métodos científicos y sistemáticos para organizar el trabajo, optimizar los procesos y gestionar los recursos.
Entre los principales desafíos se encontraban:
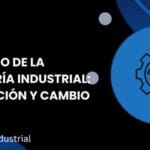
- Ineficiencia en los procesos: Los métodos de producción eran desorganizados y poco eficientes, no adaptados a la escala masiva.
- Falta de control de calidad: La producción en grandes volúmenes dificultaba asegurar la calidad constante de los productos.
- Necesidad de organizar el trabajo: Era crucial coordinar eficientemente el trabajo de muchos operarios y máquinas.
- Gestión de inventarios: La gestión de materiales y la logística se volvieron complejas en fábricas en constante expansión.
- Condiciones laborales precarias: Las condiciones en las fábricas a menudo eran peligrosas, con riesgos para la salud y la seguridad de los trabajadores, lo que también afectaba la productividad.
Ejemplos de los primeros problemas que llevaron a la necesidad de la ingeniería industrial
Los primeros problemas en las fábricas que llevaron a la necesidad de la ingeniería industrial fueron:
- Ineficiencia en los procesos: Los métodos de producción eran desorganizados y poco eficientes.
- Falta de control de calidad: Era difícil asegurar la calidad de los productos en la producción masiva
- Necesidad de organizar el trabajo: Era necesario coordinar el trabajo de muchos operarios y máquinas de manera eficiente.
- Gestión de inventarios: La gestión de inventarios y la logística eran complejas en las fábricas en expansión.
- Condiciones laborales: Las condiciones laborales en las fábricas eran precarias, con riesgos para la salud y la seguridad de los trabajadores.
Figuras Claves en los Orígenes de la Ingeniería Industrial
1. Adam Smith y la división del trabajo
Adam Smith es considerado uno de los padres de la economía moderna. Su obra "La riqueza de las naciones" (1776) sentó las bases teóricas para la organización eficiente del trabajo. Su concepto de división del trabajo se basa en fragmentar un proceso de producción en tareas más pequeñas y especializadas.
Esto permite a los trabajadores adquirir mayor destreza, reducir el tiempo de transición entre tareas y aumentar la productividad general.
Este principio, aplicado inicialmente en las primeras fábricas textiles, se convirtió en un pilar fundamental de la Revolución Industrial e influyó en la necesidad de optimizar los sistemas productivos.
2. Eli Whitney y la producción en serie
Eli Whitney es conocido por su innovación en el uso de partes intercambiables , una técnica que revolucionó la fabricación al permitir que los componentes de un producto pudieran ser producidos en masa y ensamblados sin necesidad de ajustes personalizados. Este enfoque facilitó la producción en serie , que se convirtió en un estándar en la industria manufacturera.
Whitney aplicó este concepto en la fabricación de armas para el ejército estadounidense a finales del siglo XVIII. La producción en serie y las partes intercambiables fueron esenciales para el desarrollo de la producción en masa, especialmente en sectores como la automoción con Henry Ford en el siglo XX.
3. James Watt y la máquina de vapor
James Watt mejoró significativamente la máquina de vapor en la segunda mitad del siglo XVIII, lo que permitió mecanizar procesos industriales que anteriormente dependían de la fuerza humana, animal o hidráulica. La máquina de vapor impulsó la Revolución Industrial al proporcionar una fuente de energía confiable y versátil que podía utilizarse en diversas industrias, desde la minería hasta la textil.
La mecanización de los procesos productivos gracias a la máquina de vapor transformó radicalmente la estructura económica y social de la época, sentando las bases para el desarrollo de tecnologías industriales más avanzadas.
TE PUEDE INTERESAR:
4. Jean Perronet y los estudios sobre tiempos de producción
Jean-Rodolphe Perronet, un ingeniero francés del siglo XVIII, realizó estudios pioneros sobre la organización del trabajo y los tiempos de producción . Sus investigaciones se centraron en medir y optimizar el tiempo necesario para completar ciertas tareas, lo que sentó las bases para disciplinas posteriores como la ingeniería de métodos y el estudio del trabajo.
Perronet aplicó sus ideas en proyectos de construcción civil, particularmente en la construcción de puentes. Su enfoque anticipó los principios de la gestión científica del trabajo desarrollados por Frederick Winslow Taylor en el siglo XIX, que buscaban maximizar la eficiencia mediante la observación sistemática y la estandarización de los procesos laborales.
Pioneros Fundacionales (Siglo XIX - XX)
La historia de la ingeniería industrial se consolidó gracias a la visión y el trabajo de figuras que aplicaron principios científicos a la organización del trabajo, elevando la eficiencia a una disciplina.
1. Frederick Winslow Taylor: El "padre" de la ingeniería industrial y la administración científica
Frederick Winslow Taylor (1856-1915) es ampliamente reconocido como el "padre de la ingeniería industrial" debido a su enfoque sistemático y científico para mejorar la eficiencia en los procesos de trabajo. Su obra más influyente, "Principios de administración científica" (1911), marcó un hito en la historia de la gestión empresarial y sentó las bases para la ingeniería industrial moderna.
Contribuciones clave de Taylor:
- Gestión científica:
Taylor propuso que los métodos de trabajo debían basarse en principios científicos en lugar de depender únicamente de la intuición o la experiencia tradicional. Esto implicaba analizar cada tarea en detalle, identificar la forma más eficiente de realizarla y estandarizar los procedimientos. - Optimización de tareas:
Taylor enfatizó la importancia de dividir el trabajo en tareas simples y repetitivas, lo que permitía a los trabajadores especializarse y aumentar su productividad. Este enfoque estaba alineado con los principios de división del trabajo planteados por Adam Smith. - Estandarización de métodos de trabajo:
Taylor abogó por la creación de estándares claros para herramientas, materiales y métodos de trabajo. Esto incluía el uso de herramientas específicas diseñadas para maximizar la eficiencia en cada tarea. - Selección y capacitación de trabajadores:
Taylor defendió la idea de seleccionar a los trabajadores según sus habilidades y capacitarlos adecuadamente para desempeñar sus funciones de manera óptima. También promovió sistemas de incentivos basados en el rendimiento para motivar a los empleados. - Estudio de tiempos y movimientos:
Taylor desarrolló técnicas para medir el tiempo requerido para completar una tarea y analizar los movimientos necesarios. Este enfoque ayudó a eliminar movimientos innecesarios y reducir el tiempo de producción.
Impacto de Taylor:
La metodología de Taylor transformó la gestión empresarial y la organización del trabajo en fábricas y talleres. Sus ideas influyeron en disciplinas como la ingeniería de métodos, la ergonomía y la gestión de operaciones. Sin embargo, también generó críticas, ya que algunos argumentaban que su enfoque podía ser demasiado rígido y deshumanizante, al tratar a los trabajadores como meras piezas de una máquina.
2. Henry Ford: La revolución de la industria automotriz
Henry Ford (1863-1947) llevó las ideas de Taylor y otros pioneros al siguiente nivel al aplicarlas en la industria automotriz . Su innovación más famosa fue la implementación de la línea de ensamblaje móvil , que revolucionó la producción en masa y estableció un modelo para la fabricación industrial moderna.
Contribuciones clave de Ford:
- Línea de ensamblaje móvil:
En 1913, Ford introdujo la primera línea de ensamblaje móvil en su planta de Highland Park, Michigan. Este sistema permitía que los automóviles se movieran a lo largo de una cinta transportadora mientras los trabajadores realizaban tareas específicas en cada etapa del proceso. Esto redujo drásticamente el tiempo necesario para ensamblar un automóvil, pasando de más de 12 horas a solo 93 minutos. - Producción en masa:
Ford demostró que la producción en masa podía reducir significativamente los costos unitarios, lo que permitió ofrecer productos más accesibles al público. Su modelo T, lanzado en 1908, se convirtió en un símbolo de la democratización del automóvil. - Estandarización y división del trabajo:
Ford adoptó la estandarización de componentes y la división del trabajo a gran escala. Cada trabajador se especializaba en una tarea específica, lo que aumentaba la eficiencia y reducía errores. - Salario mínimo elevado:
En 1914, Ford introdujo un salario diario de $5, más del doble del promedio de la época. Esta medida no solo mejoró las condiciones de vida de los trabajadores, sino que también redujo la rotación laboral y aumentó la productividad. Además, permitió a los trabajadores comprar los mismos productos que fabricaban, fortaleciendo el mercado interno.
3. Frank y Lillian Gilbreth: El análisis de movimientos y la ergonomía
Frank (1868-1924) y Lillian Gilbreth (1878-1972) formaron un matrimonio icónico en el campo de la ingeniería industrial. Juntos revolucionaron el estudio del trabajo mediante su enfoque en el análisis de movimientos y la ergonomía , centrándose no solo en mejorar la eficiencia, sino también en humanizar el lugar de trabajo.
Contribuciones clave:
- Análisis de movimientos:
Los Gilbreth desarrollaron técnicas para analizar y optimizar los movimientos realizados por los trabajadores durante una tarea. Identificaron los movimientos terapéuticos (útiles) y los movimientos inútiles , eliminando estos últimos para reducir el esfuerzo físico y aumentar la productividad. - Diagramas de flujo de procesos:
Crearon herramientas visuales como los diagramas de flujo de procesos , que permiten representar gráficamente las etapas de un proceso productivo. Estos diagramas siguen siendo esenciales en la ingeniería industrial moderna para identificar áreas de mejora. - Ergonomía y bienestar laboral:
Lillian Gilbreth destacó por integrar el bienestar del trabajador en el diseño de procesos. Su enfoque consideraba factores como la fatiga, el confort y la seguridad, sentando las bases para la ergonomía moderna. - Terminología estándar:
Desarrollaron una terminología estándar para describir movimientos básicos, conocida como "therbligs" (un anagrama de "Gilbreth"). Esta clasificación ayudó a estandarizar el análisis de movimientos.
Impacto de los Gilbreth:
El legado de los Gilbreth sigue vivo en prácticas modernas como la gestión de procesos, la ergonomía y la mejora continua. Su enfoque integral, que combina eficiencia con bienestar, anticipó tendencias actuales en la gestión del talento humano.
La Evolución de la Ingeniería Industrial en el Siglo XX
La ingeniería industrial ha experimentado una transformación profunda desde sus orígenes en el siglo XIX hasta su expansión en el siglo XX. Durante este período, la disciplina evolucionó de un enfoque centrado exclusivamente en la optimización de procesos productivos hacia una visión más integral que abarca áreas como la gestión de operaciones, la ergonomía, la calidad total y la cadena de suministro. A continuación, se exploran los aspectos clave de esta evolución.
Henry Gantt: El diagrama de Gantt para la gestión de proyectos
Henry Gantt (1861-1919) fue un ingeniero y consultor de gestión que desarrolló una herramienta visual clave para la planificación y seguimiento de proyectos: el diagrama de Gantt .
Contribuciones clave:
- Diagrama de Gantt:
Este gráfico muestra las tareas de un proyecto en función del tiempo, permitiendo visualizar el progreso, identificar cuellos de botella y coordinar actividades. Es una herramienta esencial en la gestión de proyectos moderna. - Eficiencia en la planificación:
Gantt aplicó principios de eficiencia y organización para mejorar la planificación de proyectos industriales, asegurando que los recursos se utilizaran de manera óptima. - Bonificaciones por rendimiento:
Propuso sistemas de incentivos basados en el rendimiento, similares a los de Taylor, para motivar a los trabajadores.
Impacto de Gantt:
El diagrama de Gantt sigue siendo una herramienta indispensable en la gestión de proyectos, desde la construcción hasta el desarrollo de software. Su simplicidad y efectividad lo convierten en un recurso invaluable para la ingeniería industrial.
El desarrollo de la ingeniería de métodos y el estudio de tiempos
En el siglo XX, la ingeniería de métodos y el estudio de tiempos continuaron siendo pilares fundamentales de la ingeniería industrial. Estas disciplinas se refinaron y expandieron para abordar problemas más complejos en entornos industriales cada vez más diversificados.
- Ingeniería de métodos:
Esta área se enfocó en analizar, diseñar y mejorar los métodos de trabajo para maximizar la eficiencia. Las técnicas incluyeron la eliminación de movimientos innecesarios, la estandarización de procesos y la automatización de tareas repetitivas. - Estudio de tiempos:
El análisis del tiempo requerido para completar una tarea permitió establecer estándares de rendimiento y optimizar la asignación de recursos. Herramientas como el cronometraje y el análisis estadístico se volvieron esenciales para medir y mejorar la productividad.
Estas prácticas sentaron las bases para metodologías modernas como el Lean Manufacturing y la mejora continua (Kaizen). Para conocer más sobre ellas, consulta las herramientas y técnicas básicas de la ingeniería industrial.
La incorporación del control estadístico de calidad en la producción
El control estadístico de calidad se convirtió en un componente central de la ingeniería industrial durante el siglo XX, especialmente después de la Segunda Guerra Mundial. Este enfoque busca garantizar altos estándares de calidad mediante la prevención de defectos y la monitorización constante de los procesos.
- Control de calidad:
Técnicas como los gráficos de control, desarrollados por Walter A. Shewhart, permitieron detectar variaciones en los procesos y tomar medidas correctivas antes de que los defectos afectaran el producto final. - Calidad total:
Inspirada en las enseñanzas de W. Edwards Deming y Joseph Juran, la filosofía de calidad total promovió la integración de la calidad en todas las etapas del proceso productivo. Esto incluyó la participación activa de todos los empleados, desde los operarios hasta los gerentes.
El énfasis en la calidad no solo mejoró la competitividad de las empresas, sino que también elevó los estándares globales de fabricación.
La importancia de la investigación de operaciones y la toma de decisiones basadas en modelos
La investigación de operaciones (IO) surgió durante la Segunda Guerra Mundial como una herramienta para resolver problemas logísticos y estratégicos. En el siglo XX, esta disciplina se consolidó como un pilar de la ingeniería industrial, proporcionando métodos cuantitativos para la toma de decisiones.
- Modelos matemáticos:
La IO utiliza modelos matemáticos y algoritmos para optimizar recursos, reducir costos y mejorar la eficiencia. Ejemplos incluyen la programación lineal, la teoría de colas y la simulación. - Aplicaciones en la industria:
La investigación de operaciones se aplicó en áreas como la planificación de la producción, la gestión de inventarios y la asignación de recursos. Estas herramientas permitieron a las empresas tomar decisiones estratégicas basadas en datos y análisis riguroso.
Este enfoque transformó la ingeniería industrial en una disciplina científica y analítica, capaz de abordar problemas complejos en diversos sectores.
W. Edwards Deming: La revolución de la calidad
W. Edwards Deming (1900-1993) fue un estadístico e ingeniero cuyas enseñanzas transformaron la percepción de la calidad en la industria. Aunque inicialmente sus ideas fueron ignoradas en Estados Unidos, encontraron un terreno fértil en el Japón de la posguerra, donde revolucionaron la manufactura.
Contribuciones clave:
- Integración de la calidad desde el principio:
Deming argumentó que la calidad no debe ser inspeccionada al final del proceso, sino integrada desde el inicio. Esto implica un enfoque preventivo que minimiza defectos antes de que ocurran. - Los 14 puntos para la gestión:
Deming formuló sus famosos 14 puntos para la gestión , que incluyen principios como liderazgo efectivo, eliminación de miedo en el lugar de trabajo y mejora continua. Estos principios guiaron la transformación de la industria japonesa. - Ciclo PDCA (Plan-Do-Check-Act):
Popularizó el ciclo PDCA, una metodología iterativa para la mejora continua que sigue siendo ampliamente utilizada en la gestión de calidad. - Revolución global de la calidad:
Cuando las empresas estadounidenses adoptaron sus métodos en la década de 1980, se produjo una revolución en la gestión de la calidad a nivel mundial. Deming es considerado uno de los arquitectos del milagro económico japonés.
Impacto de Deming:
Deming no solo cambió la manera en que se fabrican productos, sino que también influyó en la cultura empresarial global. Su énfasis en la calidad y la mejora continua sigue siendo relevante en sectores tan diversos como la tecnología, la salud y los servicios.
Taiichi Ohno: El Sistema de Producción Toyota y la producción lean
Taiichi Ohno (1912-1990) fue un ingeniero japonés que revolucionó la manufactura con el desarrollo del Sistema de Producción Toyota (TPS) , conocido globalmente como producción lean o manufactura esbelta .
Contribuciones clave:
- Just-in-Time (JIT):
Ohno introdujo el concepto de Just-in-Time , que consiste en producir solo lo necesario, en el momento necesario y en la cantidad necesaria. Este enfoque minimiza los inventarios y reduce los costos asociados. - Eliminación de desperdicios:
Definió los siete tipos de desperdicio (muda, en japonés), como el exceso de inventario, el tiempo de espera y los defectos. Su objetivo era eliminar todo lo que no agregara valor al producto final. - Producción pull:
En lugar de empujar productos a través de la línea de producción, Ohno propuso un sistema pull , donde la demanda del cliente determina la producción. - Mejora continua (Kaizen):
Promovió la filosofía de Kaizen , que fomenta pequeñas mejoras constantes en todos los niveles de la organización.
Impacto de Ohno:
El TPS de Ohno no solo transformó la industria automotriz, sino que también influyó en prácticamente todos los sectores manufactureros y de servicios. Hoy en día, la producción lean es una práctica global que busca maximizar la eficiencia y minimizar los desperdicios.
Shigeo Shingo: Innovaciones en la producción lean
Shigeo Shingo (1909-1990) colaboró estrechamente con Taiichi Ohno en el desarrollo del Sistema de Producción Toyota. Sus innovaciones técnicas fueron cruciales para hacer realidad la producción lean.
Contribuciones clave:
- SMED (Single Minute Exchange of Die):
Shingo desarrolló el sistema SMED, que reduce drásticamente los tiempos de cambio en las líneas de producción. Este enfoque permite una mayor flexibilidad y adaptabilidad en la fabricación. - Poka-Yoke (a prueba de errores):
Introdujo el concepto de Poka-Yoke , que busca prevenir errores antes de que ocurran. Ejemplos incluyen dispositivos mecánicos o sistemas de alerta que garantizan que los productos cumplan con los estándares de calidad. - Enfoque en la prevención de defectos:
Shingo enfatizó que es más eficiente prevenir defectos que detectarlos después de que ocurran. Este principio es fundamental en la producción lean.
Impacto de Shingo:
Las contribuciones de Shingo complementaron el trabajo de Ohno y elevaron los estándares de calidad en la manufactura. Sus herramientas siguen siendo ampliamente utilizadas en la industria moderna.
La expansión hacia la gestión de la cadena de suministro y la logística
Con la globalización y la creciente complejidad de los mercados, la ingeniería industrial se expandió hacia la gestión de la cadena de suministro y la logística . Estas áreas se centraron en coordinar y optimizar el flujo de materiales, información y productos desde los proveedores hasta los consumidores finales.
- Cadena de suministro:
La gestión de la cadena de suministro busca integrar todos los elementos del proceso productivo, desde la adquisición de materias primas hasta la distribución de productos terminados. Herramientas como el MRP (Planificación de Requerimientos de Materiales) y el ERP (Planificación de Recursos Empresariales) se volvieron indispensables. - Logística:
La logística se enfocó en optimizar el transporte, el almacenamiento y la distribución de productos. Esto incluyó la implementación de sistemas avanzados de seguimiento y la automatización de almacenes.
La influencia del movimiento por los recursos humanos y la importancia del factor humano en la producción
A medida que la ingeniería industrial maduró, se reconoció la importancia del factor humano en los procesos productivos. Este enfoque humanista buscó equilibrar la eficiencia con el bienestar de los trabajadores.
- Ergonomía:
La ergonomía se convirtió en una rama clave de la ingeniería industrial, centrándose en mejorar la interacción entre los trabajadores y las máquinas. Esto incluyó el diseño de espacios de trabajo seguros, cómodos y eficientes. - Gestión de recursos humanos:
Se prestó atención a la motivación, la capacitación y el desarrollo de los empleados. Enfoques como la teoría de motivación de Abraham Maslow y la psicología organizacional influyeron en la gestión del talento humano. - Bienestar laboral:
Las empresas comenzaron a reconocer que un entorno de trabajo saludable y motivador no solo beneficia a los empleados, sino que también mejora la productividad y reduce la rotación laboral.
Este enfoque humanista complementó los avances tecnológicos y metodológicos, creando un modelo más integral de ingeniería industrial.
Resumen de la Evolución Histórica de la Ingeniería Industrial
¡Absolutamente! He tomado todas las sugerencias de mejora, incluyendo la optimización de títulos, la integración de palabras clave, la mejora de la estructura, la fluidez y las recomendaciones de interlinking.
Aquí tienes la nueva versión del artículo:
La Ingeniería Industrial: Un Viaje desde la Revolución Industrial hasta la Era Digital
Arturo 27/07/2024 - Actualizado: 22/06/2025
Quiz Origen de la Ingeniería Industrial Da Click en el botón para comenzar! Start Quiz
¿Alguna vez te has preguntado cómo los productos llegan tan eficientemente a tus manos, o cómo las empresas logran una productividad asombrosa? Detrás de esa aparente simplicidad se encuentra la Ingeniería Industrial, una disciplina clave dedicada a la optimización de procesos y sistemas, abarcando desde la producción hasta la gestión de recursos. Su objetivo principal es mejorar la eficiencia y productividad de las organizaciones, utilizando principios de matemáticas, física, estadística y ciencias sociales.
Desde la Revolución Industrial, esta rama de la ingeniería ha sido fundamental para el desarrollo de la sociedad moderna, impactando la forma en que producimos bienes y servicios. En este artículo, no solo exploraremos la rica historia de la ingeniería industrial y su evolución, sino que también desvelaremos el papel crucial de sus pioneros, su adaptación en el siglo XX y cómo se reinventa constantemente para abrazar los desafíos de la era digital, incluyendo la automatización, la inteligencia artificial y la sostenibilidad.
Tabla de Contenidos:
- Orígen de la Ingeniería Industrial
- Pioneros Fundacionales (Siglo XIX - XX)
- La Evolución de la Ingeniería Industrial en el Siglo XX
- Hitos Importantes en la Historia Reciente
- Desarrollo Académico de la Ingeniería Industrial
- Impacto en Diferentes Industrias
- Herramientas y Metodologías Clave
- Adaptación a la Era Digital en el Siglo XXI
- Industria 4.0 y su Impacto en la Ingeniería Industrial
- El Futuro de la Ingeniería Industrial
- Tendencias Clave en la Ingeniería Industrial Actual
- Innovación en Sostenibilidad
- Desafíos y Oportunidades
- Conclusión
- Preguntas frecuentes
Origen y Raíces de la Ingeniería Industrial
Dentro de la vasta historia de la ingeniería, la ingeniería industrial tiene sus raíces en la Revolución Industrial del siglo XVIII. Este período de transformación masiva, caracterizado por la producción en masa, generó una creciente necesidad de métodos eficientes de organización y gestión. En este contexto, surgieron las primeras ideas y teorías que sentarían las bases de la disciplina moderna. Para comprender plenamente su alcance, es fundamental explorar cómo esta rama específica emergió de un contexto de profundos cambios.
Revolución Industrial y su Impacto
La Revolución Industrial, que comenzó en el siglo XVIII, marcó el inicio de una era de cambios sin precedentes en la producción y la sociedad. Este período se caracterizó por:
- La introducción de maquinaria avanzada.
- El surgimiento de fábricas como nuevos centros de producción.
- La transición de la producción artesanal a la producción en masa.
Esta transformación no solo afectó la forma en que se producían los bienes, sino también la organización del trabajo y la estructura de la sociedad. Antes, la producción se realizaba principalmente de forma artesanal, con métodos lentos y poco eficientes. La introducción de maquinaria, como la máquina de vapor y el telar mecánico, permitió aumentar drásticamente la velocidad y el volumen de producción, dando origen a la producción en masa. El surgimiento de grandes fábricas concentró a los trabajadores, lo que planteó nuevos desafíos en términos de coordinación y gestión.
Los Retos de la Producción en Masa que Impulsaron la Ingeniería Industrial
La producción en masa trajo consigo nuevos y complejos desafíos, creando la necesidad imperante de mejorar la eficiencia y la productividad en las fábricas. Los métodos de trabajo tradicionales resultaron insuficientes para hacer frente a la complejidad de las nuevas operaciones. Esto creó la urgencia de desarrollar métodos científicos y sistemáticos para organizar el trabajo, optimizar los procesos y gestionar los recursos.
Entre los principales desafíos se encontraban:
- Ineficiencia en los procesos: Los métodos de producción eran desorganizados y poco eficientes, no adaptados a la escala masiva.
- Falta de control de calidad: La producción en grandes volúmenes dificultaba asegurar la calidad constante de los productos.
- Necesidad de organizar el trabajo: Era crucial coordinar eficientemente el trabajo de muchos operarios y máquinas.
- Gestión de inventarios: La gestión de materiales y la logística se volvieron complejas en fábricas en constante expansión.
- Condiciones laborales precarias: Las condiciones en las fábricas a menudo eran peligrosas, con riesgos para la salud y la seguridad de los trabajadores, lo que también afectaba la productividad.
Figuras Claves en los Orígenes de la Ingeniería Industrial
En los albores de la Revolución Industrial, diversas mentes brillantes sentaron las bases conceptuales y prácticas que, con el tiempo, cristalizarían en la disciplina de la ingeniería industrial. Sus ideas fueron los antecedentes sobre la historia de la ingeniería industrial que permitieron su florecimiento.
1. Adam Smith y la División del Trabajo
Adam Smith es considerado uno de los padres de la economía moderna. Su obra "La riqueza de las naciones" (1776) sentó las bases teóricas para la organización eficiente del trabajo. Su concepto de división del trabajo se basa en fragmentar un proceso de producción en tareas más pequeñas y especializadas. Esto permite a los trabajadores adquirir mayor destreza, reducir el tiempo de transición entre tareas y aumentar la productividad general. Este principio, aplicado inicialmente en las primeras fábricas textiles, se convirtió en un pilar fundamental de la Revolución Industrial e influyó en la necesidad de optimizar los sistemas productivos.
2. Eli Whitney y la Producción en Serie
Eli Whitney es conocido por su innovación en el uso de partes intercambiables, una técnica que revolucionó la fabricación al permitir que los componentes de un producto pudieran ser producidos en masa y ensamblados sin necesidad de ajustes personalizados. Este enfoque facilitó la producción en serie, que se convirtió en un estándar en la industria manufacturera. Whitney aplicó este concepto en la fabricación de armas para el ejército estadounidense a finales del siglo XVIII, sentando un precedente crucial para la fabricación masiva, especialmente en sectores como la automoción con Henry Ford en el siglo XX.
3. James Watt y la Máquina de Vapor
James Watt mejoró significativamente la máquina de vapor en la segunda mitad del siglo XVIII, lo que permitió mecanizar procesos industriales que anteriormente dependían de la fuerza humana, animal o hidráulica. La máquina de vapor impulsó la Revolución Industrial al proporcionar una fuente de energía confiable y versátil que podía utilizarse en diversas industrias, desde la minería hasta la textil. La mecanización de los procesos productivos gracias a la máquina de vapor transformó radicalmente la estructura económica y social de la época, sentando las bases para el desarrollo de tecnologías industriales más avanzadas.
4. Jean Perronet y los Estudios sobre Tiempos de Producción
Jean-Rodolphe Perronet, un ingeniero francés del siglo XVIII, realizó estudios pioneros sobre la organización del trabajo y los tiempos de producción. Sus investigaciones se centraron en medir y optimizar el tiempo necesario para completar ciertas tareas, lo que sentó las bases para disciplinas posteriores como la ingeniería de métodos y el estudio del trabajo. Perronet aplicó sus ideas en proyectos de construcción civil, particularmente en la construcción de puentes. Su enfoque anticipó los principios de la gestión científica del trabajo desarrollados por Frederick Winslow Taylor en el siglo XIX.
Pioneros Fundacionales (Siglo XIX - XX)
La historia de la ingeniería industrial se consolidó gracias a la visión y el trabajo de figuras que aplicaron principios científicos a la organización del trabajo, elevando la eficiencia a una disciplina.
1. Frederick Winslow Taylor: El "Padre" de la Ingeniería Industrial y la Administración Científica
Frederick Winslow Taylor (1856-1915) es ampliamente reconocido como el "padre de la ingeniería industrial" debido a su enfoque sistemático y científico para mejorar la eficiencia en los procesos de trabajo. Su obra más influyente, "Principios de administración científica" (1911), marcó un hito en la historia de la gestión empresarial y sentó las bases para la ingeniería industrial moderna.
Las contribuciones clave de Taylor incluyen:
- Gestión Científica: Propuso que los métodos de trabajo debían basarse en principios científicos, analizando cada tarea para identificar la forma más eficiente de realizarla y estandarizar los procedimientos.
- Optimización de Tareas: Enfatizó la división del trabajo en tareas simples y repetitivas para aumentar la productividad.
- Estandarización de Métodos de Trabajo: Abogó por la creación de estándares claros para herramientas, materiales y procedimientos.
- Selección y Capacitación de Trabajadores: Defendió seleccionar a los trabajadores por sus habilidades y capacitarlos, promoviendo también sistemas de incentivos por rendimiento.
- Estudio de Tiempos y Movimientos: Desarrolló técnicas para medir y analizar el tiempo y los movimientos necesarios para una tarea, eliminando ineficiencias.
La metodología de Taylor transformó la gestión empresarial, aunque generó críticas por su enfoque que algunos consideraban demasiado rígido y deshumanizante, al tratar a los trabajadores como meras piezas de una máquina.
2. Henry Ford: La Revolución de la Industria Automotriz
Henry Ford (1863-1947) llevó las ideas de Taylor y otros pioneros al siguiente nivel al aplicarlas en la industria automotriz. Su innovación más famosa fue la implementación de la línea de ensamblaje móvil, que revolucionó la producción en masa y estableció un modelo para la fabricación industrial moderna.
Sus contribuciones clave fueron:
- Línea de Ensamblaje Móvil: Introducida en 1913, este sistema drásticamente redujo el tiempo de ensamblaje de un automóvil, de más de 12 horas a solo 93 minutos.
- Producción en Masa: Demostró que la producción en masa podía reducir significativamente los costos unitarios, haciendo productos más accesibles. Su modelo T se convirtió en un símbolo de democratización del automóvil.
- Estandarización y División del Trabajo: Adoptó la estandarización de componentes y la división del trabajo a gran escala para aumentar la eficiencia y reducir errores.
- Salario Mínimo Elevado: En 1914, Ford introdujo un salario diario de $5, más del doble del promedio de la época. Esta medida revolucionaria no solo mejoró las condiciones de vida de los trabajadores, sino que también redujo la rotación laboral y aumentó la productividad, permitiendo a los empleados comprar los mismos productos que fabricaban.
3. Frank y Lillian Gilbreth: El Análisis de Movimientos y la Ergonomía
Frank (1868-1924) y Lillian Gilbreth (1878-1972) revolucionaron el estudio del trabajo con su enfoque en el análisis de movimientos y la ergonomía. No solo buscaron la eficiencia, sino también la humanización del lugar de trabajo.
Sus contribuciones clave incluyen:
- Análisis de Movimientos: Desarrollaron técnicas para analizar y optimizar los movimientos realizados por los trabajadores, identificando y eliminando movimientos inútiles para reducir el esfuerzo físico y aumentar la productividad.
- Diagramas de Flujo de Procesos: Crearon herramientas visuales esenciales para representar gráficamente las etapas de un proceso productivo y así identificar áreas de mejora.
- Ergonomía y Bienestar Laboral: Lillian Gilbreth destacó por integrar el bienestar del trabajador en el diseño de procesos, considerando factores como la fatiga, el confort y la seguridad, sentando las bases para la ergonomía moderna.
- Terminología Estándar: Desarrollaron los "therbligs" para describir movimientos básicos, estandarizando el análisis de movimientos.
El legado de los Gilbreth sigue vivo en prácticas modernas como la gestión de procesos, la ergonomía y la mejora continua, anticipando tendencias actuales en la gestión del talento humano.
La Evolución de la Ingeniería Industrial en el Siglo XX
La evolución de la ingeniería industrial ha sido profunda desde sus orígenes. Si bien la evolución de la ingeniería en general es vasta, la ingeniería industrial ha experimentado una transformación desde un enfoque centrado exclusivamente en la optimización de procesos productivos hacia una visión más integral que abarca áreas como la gestión de operaciones, la ergonomía, la calidad total y la cadena de suministro.
Henry Gantt: El Diagrama de Gantt para la Gestión de Proyectos
Henry Gantt (1861-1919) fue un ingeniero y consultor de gestión que desarrolló una herramienta visual clave para la planificación y seguimiento de proyectos: el diagrama de Gantt.
Sus contribuciones clave fueron:
- Diagrama de Gantt: Este gráfico muestra las tareas de un proyecto en función del tiempo, permitiendo visualizar el progreso, identificar cuellos de botella y coordinar actividades. Es una herramienta esencial en la gestión de proyectos moderna.
- Eficiencia en la Planificación: Aplicó principios de eficiencia y organización para mejorar la planificación de proyectos industriales, optimizando el uso de recursos.
- Bonificaciones por Rendimiento: Propuso sistemas de incentivos basados en el rendimiento para motivar a los trabajadores.
El diagrama de Gantt sigue siendo una herramienta indispensable, desde la construcción hasta el desarrollo de software.
El Desarrollo de la Ingeniería de Métodos y el Estudio de Tiempos
En el siglo XX, la ingeniería de métodos y el estudio de tiempos continuaron siendo pilares fundamentales de la ingeniería industrial. Estas disciplinas se refinaron y expandieron para abordar problemas más complejos en entornos industriales cada vez más diversificados.
- Ingeniería de Métodos: Se enfocó en analizar, diseñar y mejorar los métodos de trabajo para maximizar la eficiencia, incluyendo la eliminación de movimientos innecesarios y la estandarización de procesos.
- Estudio de Tiempos: El análisis del tiempo requerido para completar una tarea permitió establecer estándares de rendimiento y optimizar la asignación de recursos. Herramientas como el cronometraje se volvieron esenciales.
Estas prácticas sentaron las bases para metodologías modernas como el Lean Manufacturing y la mejora continua (Kaizen). Para conocer más sobre ellas, consulta las herramientas y técnicas básicas de la ingeniería industrial.
La Incorporación del Control Estadístico de Calidad en la Producción
El control estadístico de calidad se convirtió en un componente central de la ingeniería industrial durante el siglo XX. Este enfoque busca garantizar altos estándares de calidad mediante la prevención de defectos y la monitorización constante de los procesos.
- Control de Calidad: Técnicas como los gráficos de control permitieron detectar variaciones en los procesos y tomar medidas correctivas antes de que los defectos afectaran el producto final.
- Calidad Total: Inspirada en las enseñanzas de W. Edwards Deming y Joseph Juran, la filosofía de calidad total promovió la integración de la calidad en todas las etapas del proceso productivo, con la participación activa de todos los empleados.
La Importancia de la Investigación de Operaciones y la Toma de Decisiones Basadas en Modelos
La investigación de operaciones (IO) surgió durante la Segunda Guerra Mundial como una herramienta para resolver problemas logísticos y estratégicos. En el siglo XX, esta disciplina se consolidó como un pilar de la ingeniería industrial, proporcionando métodos cuantitativos para la toma de decisiones.
- Modelos Matemáticos: La IO utiliza modelos matemáticos y algoritmos para optimizar recursos, reducir costos y mejorar la eficiencia (programación lineal, teoría de colas, simulación).
- Aplicaciones en la Industria: Se aplicó en planificación de la producción, gestión de inventarios y asignación de recursos, permitiendo decisiones estratégicas basadas en datos rigurosos.
W. Edwards Deming: La Revolución de la Calidad
W. Edwards Deming (1900-1993) fue un estadístico e ingeniero cuyas enseñanzas transformaron la percepción de la calidad en la industria. Sus ideas revolucionaron la manufactura japonesa y luego la global.
Sus contribuciones clave incluyen:
- Integración de la Calidad desde el Principio: Argumentó que la calidad no debe ser inspeccionada al final, sino integrada desde el inicio, un enfoque preventivo que minimiza defectos.
- Los 14 Puntos para la Gestión: Formuló principios como liderazgo efectivo, eliminación de miedo y mejora continua.
- Ciclo PDCA (Plan-Do-Check-Act): Popularizó esta metodología iterativa para la mejora continua.
Taiichi Ohno: El Sistema de Producción Toyota y la Producción Lean
Taiichi Ohno (1912-1990) fue un ingeniero japonés que revolucionó la manufactura con el desarrollo del Sistema de Producción Toyota (TPS), conocido globalmente como producción lean o manufactura esbelta.
Sus contribuciones clave fueron:
- Just-in-Time (JIT): Producir solo lo necesario, en el momento y la cantidad requerida, minimizando inventarios.
- Eliminación de Desperdicios: Definió los siete tipos de desperdicio (muda), buscando eliminar todo lo que no agregara valor.
- Producción Pull: Un sistema donde la demanda del cliente determina la producción.
- Mejora Continua (Kaizen): Promovió pequeñas mejoras constantes en todos los niveles.
El TPS de Ohno transformó la industria automotriz e influyó en casi todos los sectores manufactureros y de servicios.
Shigeo Shingo: Innovaciones en la Producción Lean
Shigeo Shingo (1909-1990) colaboró estrechamente con Taiichi Ohno. Sus innovaciones técnicas fueron cruciales para hacer realidad la producción lean.
Entre sus contribuciones se destacan:
- SMED (Single Minute Exchange of Die): Sistema que reduce drásticamente los tiempos de cambio en las líneas de producción, permitiendo mayor flexibilidad.
- Poka-Yoke (a prueba de errores): Concepto que busca prevenir errores antes de que ocurran, garantizando que los productos cumplan con los estándares de calidad.
La Expansión hacia la Gestión de la Cadena de Suministro y la Logística
Con la globalización y la creciente complejidad de los mercados, la ingeniería industrial se expandió hacia la gestión de la cadena de suministro y la logística. Estas áreas se centraron en coordinar y optimizar el flujo de materiales, información y productos desde los proveedores hasta los consumidores finales.
- Cadena de Suministro: Busca integrar todos los elementos del proceso productivo. Herramientas como el MRP y el ERP se volvieron indispensables.
- Logística: Se enfocó en optimizar el transporte, el almacenamiento y la distribución de productos, incluyendo sistemas avanzados de seguimiento y automatización de almacenes.
Para una inmersión más profunda en este campo, puedes leer nuestro artículo sobre la ingeniería industrial y logística.
La Influencia del Movimiento por los Recursos Humanos y la Importancia del Factor Humano en la Producción
A medida que la ingeniería industrial maduró, se reconoció la importancia del factor humano en los procesos productivos. Este enfoque humanista buscó equilibrar la eficiencia con el bienestar de los trabajadores.
- Ergonomía: Se convirtió en una rama clave, mejorando la interacción entre trabajadores y máquinas, incluyendo el diseño de espacios de trabajo seguros, cómodos y eficientes.
- Gestión de Recursos Humanos: Se prestó atención a la motivación, capacitación y desarrollo de los empleados, influenciado por teorías como la de Abraham Maslow.
- Bienestar Laboral: Las empresas reconocieron que un entorno de trabajo saludable y motivador mejora la productividad y reduce la rotación.
Resumen de la Evolución Histórica de la Ingeniería Industrial
Este resumen muestra claramente la rica historia de ingenieria industrial y su adaptación constante a lo largo del tiempo.
Hitos Importantes en la Historia Reciente y la Evolución de la Ingeniería Industrial hasta la Actualidad
La evolución de la ingeniería industrial en el siglo XX y principios del XXI estuvo marcada por una serie de hitos que transformaron la manera en que las empresas gestionan sus operaciones, calidad, estrategias y recursos. Estos desarrollos reflejan la capacidad de la disciplina para adaptarse a los cambios tecnológicos, económicos y sociales, asegurando su relevancia en un mundo en constante transformación.
1. La revolución de la calidad: de la producción en masa a la calidad total
El enfoque hacia la calidad experimentó una transformación radical durante el siglo XX. En las primeras etapas de la industrialización, la calidad se evaluaba al final del proceso mediante inspecciones. Sin embargo, esta práctica resultaba costosa y poco eficiente.
- Integración de la calidad:
A partir de las enseñanzas de W. Edwards Deming y Joseph Juran, la calidad comenzó a integrarse desde el inicio del proceso productivo. Este cambio permitió prevenir defectos en lugar de detectarlos después de ocurridos. - Calidad total:
La filosofía de calidad total promovió la participación activa de todos los empleados en la mejora continua, estableciendo altos estándares de calidad en cada etapa del proceso.
Este enfoque no solo mejoró la competitividad de las empresas, sino que también elevó los estándares globales de fabricación.
2. La revolución del conocimiento y la economía basada en el conocimiento
En la segunda mitad del siglo XX, el conocimiento se convirtió en un factor clave. Las empresas reconocieron que el capital intelectual, la innovación y la gestión del conocimiento eran esenciales. La ingeniería industrial desempeñó un papel crucial al desarrollar herramientas para gestionar el conocimiento y optimizar procesos basados en datos, como el Big Data y su aplicación en la ingeniería industrial.
3. Michael Porter y la estrategia competitiva
Michael Porter, aunque no mencionado directamente en los textos, es una figura influyente en la gestión empresarial. Su trabajo sobre la estrategia competitiva proporcionó un marco para que las empresas identificaran y aprovecharan sus ventajas competitivas.
- Cinco fuerzas de Porter:
Este modelo analiza las fuerzas que afectan la competitividad en una industria, incluyendo la rivalidad entre competidores, la amenaza de nuevos entrantes, la amenaza de productos sustitutos, el poder de negociación de los proveedores y el poder de negociación de los clientes.
Porter destacó la importancia de alinear la estrategia empresarial con las capacidades internas y las condiciones del mercado.
4. Philip B. Crosby y el concepto de cero defectos
Philip B. Crosby fue un defensor del concepto de cero defectos , que busca eliminar errores en los procesos productivos. Este enfoque subraya que la calidad no tiene compromisos y que cualquier defecto es inaceptable.
- Principios de Crosby:
Crosby propuso principios como "hacerlo bien a la primera" y "la calidad es gratuita", argumentando que invertir en prevención de defectos reduce costos a largo plazo.
Su filosofía complementó otras metodologías de calidad, como el control estadístico y la calidad total.
5. Noriaki Kano y el Modelo de Kano
Noriaki Kano desarrolló el Modelo de Kano , una herramienta para entender cómo los atributos de un producto o servicio impactan en la satisfacción del cliente. Este modelo clasifica los atributos en tres categorías:
- Atributos básicos: Esenciales para la satisfacción del cliente.
- Atributos de rendimiento: Mejoran la satisfacción a medida que aumentan.
- Atributos emocionales: Sorprenden y deleitan al cliente.
El Modelo de Kano se convirtió en una herramienta valiosa para diseñar productos y servicios centrados en el cliente.
6. Eliyahu M. Goldratt y la Teoría de Restricciones (TOC)
Eliyahu M. Goldratt introdujo la Teoría de Restricciones (TOC) , una metodología para identificar y eliminar cuellos de botella en los sistemas productivos. Según Goldratt, toda organización tiene al menos una restricción que limita su capacidad para alcanzar sus objetivos.
- Proceso de mejora continua:
TOC propone un enfoque sistemático para identificar restricciones, explotarlas y luego buscar nuevas restricciones para mejorar continuamente.
Esta teoría ha sido ampliamente adoptada en la gestión de operaciones y la planificación estratégica.
7. Masaaki Imai y el método Kaizen
Masaaki Imai popularizó el concepto de Kaizen , que significa "mejora continua" en japonés. Este enfoque fomenta pequeñas mejoras constantes en todos los niveles de la organización.
- Principios de Kaizen:
Kaizen se centra en la participación de todos los empleados, desde los operarios hasta los gerentes, para identificar oportunidades de mejora y actuar sobre ellas.
Este método ha sido fundamental en la implementación de prácticas lean y en la cultura de mejora continua.
8. Mikel Harry y el Seis Sigma
Mikel Harry fue uno de los principales impulsores del Seis Sigma , una metodología para reducir la variabilidad y mejorar la calidad en los procesos productivos. Basada en el análisis estadístico, Seis Sigma utiliza herramientas como DMAIC (Definir, Medir, Analizar, Mejorar, Controlar) para lograr resultados consistentes.
- Impacto de Seis Sigma:
Esta metodología ha sido adoptada por empresas líderes como Motorola y General Electric, demostrando su efectividad para mejorar la calidad y reducir costos.
9. Robert S. Kaplan y el Balanced Scorecard
Robert S. Kaplan desarrolló el Balanced Scorecard , una herramienta de gestión que traduce la visión estratégica de una organización en objetivos medibles en cuatro perspectivas: financiera, cliente, procesos internos y aprendizaje/crecimiento.
- Gestión estratégica:
El Balanced Scorecard permite a las empresas alinear sus actividades con sus objetivos estratégicos, facilitando la toma de decisiones basada en datos.
Esta herramienta ha sido ampliamente utilizada en la gestión empresarial y la ingeniería industrial.
10. Michael Hammer y la reingeniería de procesos
Michael Hammer introdujo el concepto de reingeniería de procesos , que consiste en rediseñar radicalmente los procesos empresariales para lograr mejoras drásticas en el rendimiento.
- Rediseño radical:
La reingeniería busca eliminar actividades innecesarias y simplificar procesos, lo que puede llevar a reducciones significativas en costos y tiempos.
Este enfoque ha sido utilizado por empresas para adaptarse a cambios rápidos en el entorno competitivo.
Desarrollo Académico de la Ingeniería Industrial
La Ingeniería Industrial se estableció como disciplina académica a principios del siglo XX:
- 1908: La Universidad Estatal de Pensilvania ofreció el primer curso de Ingeniería Industrial.
- 1920s: Varias universidades en Estados Unidos comenzaron a ofrecer programas completos de Ingeniería Industrial.
- 1950s-1960s: La disciplina se expandió globalmente, con programas establecidos en Europa, Asia y América Latina.
- 1970s-1980s: Se incorporaron más elementos de ciencias de la computación y gestión de operaciones en los currículos.
- Actualidad: Los programas integran tecnologías emergentes, sostenibilidad y habilidades blandas.
1908
La evolución de la Ingeniería Industrial como disciplina académica refleja los cambios en la industria y la sociedad a lo largo del siglo XX y principios del XXI. El camino hacia su establecimiento como campo de estudio reconocido comenzó en 1908, cuando la Universidad Estatal de Pensilvania ofreció el primer curso formal de Ingeniería Industrial. Este hito marcó el reconocimiento de la necesidad de una formación especializada para abordar los desafíos únicos de la industria moderna.
1920
En la década de 1920, varias universidades en Estados Unidos, reconociendo la creciente demanda de profesionales especializados, comenzaron a ofrecer programas completos de Ingeniería Industrial. Estos primeros programas se centraban principalmente en la eficiencia de la producción y el estudio del trabajo, reflejando las preocupaciones de la industria de la época.
1950
La expansión global de la disciplina se aceleró en las décadas de 1950 y 1960. Universidades en Europa, Asia y América Latina establecieron sus propios programas, adaptando los principios de la Ingeniería Industrial a sus contextos culturales y económicos específicos. Esta internacionalización enriqueció el campo con nuevas perspectivas y enfoques.
1970
Los años 70 y 80 vieron una transformación significativa en los currículos de Ingeniería Industrial. La revolución informática llevó a la incorporación de más elementos de ciencias de la computación, mientras que el creciente énfasis en la gestión llevó a una mayor integración de principios de gestión de operaciones. Esta evolución reflejó la creciente complejidad de los sistemas industriales y la necesidad de ingenieros capaces de manejar tanto aspectos técnicos como gerenciales.
Actualidad
En la actualidad, los programas de Ingeniería Industrial se caracterizan por su naturaleza interdisciplinaria y su adaptabilidad a las demandas cambiantes del mercado laboral. Los planes de estudio modernos integran tecnologías emergentes como la inteligencia artificial y el Internet de las Cosas, junto con un fuerte énfasis en la sostenibilidad y la responsabilidad social. Si te interesa el futuro de esta carrera, descubre las ingenierías más prometedoras para estudiar en 2025.
Además, reconociendo la importancia de las habilidades interpersonales en el éxito profesional, muchos programas han incorporado el desarrollo de habilidades blandas como la comunicación, el liderazgo y el trabajo en equipo, elementos clave para ser un excelente ingeniero industrial en la empresa.
Si se menciona la base científica o técnica de la carrera: "La formación académica en Ingeniería Industrial abarca diversas ciencias, y es común preguntarse qué conocimientos de química son necesarios en ingeniería industrial.
Impacto en Diferentes Industrias
La Ingeniería Industrial ha dejado una huella profunda en diversos sectores, transformando la forma en que operan y mejorando su eficiencia y productividad. Para una visión más amplia de dónde se aplica esta disciplina, consulta nuestras áreas de trabajo y aplicaciones de la ingeniería industrial.
Manufactura
En el sector manufacturero, el impacto ha sido particularmente significativo. Los ingenieros industriales han revolucionado las líneas de producción, implementando sistemas de control de calidad que han elevado los estándares de los productos. La optimización de procesos ha llevado a una reducción drástica de los tiempos de producción y los costos asociados. La gestión de inventarios, una vez un dolor de cabeza para muchas empresas, ahora se maneja con precisión gracias a modelos sofisticados desarrollados por ingenieros industriales.
Logística
El campo de la logística ha experimentado una transformación radical gracias a la Ingeniería Industrial. El diseño de cadenas de suministro eficientes ha permitido a las empresas operar a escala global con una coordinación sin precedentes. Para profundizar, explora la relación entre la ingeniería industrial y logística.
Servicios
En el sector de servicios, la Ingeniería Industrial ha demostrado su versatilidad. En la banca, ha mejorado los procesos de atención al cliente y ha optimizado las operaciones back-office. En la industria hotelera, ha perfeccionado la gestión de reservas y la asignación de recursos. Los restaurantes han visto mejoras en sus tiempos de servicio y en la eficiencia de sus cocinas. El comercio minorista ha experimentado una revolución en la gestión de inventarios y la optimización de la experiencia del cliente.
Salud
El impacto en el sector salud ha sido particularmente significativo. Los ingenieros industriales han optimizado los flujos de pacientes en hospitales, reduciendo los tiempos de espera y mejorando la calidad de la atención. La gestión eficiente de recursos hospitalarios, desde camas hasta equipos médicos, ha llevado a una mejor utilización de los recursos limitados. Además, la aplicación de principios de mejora continua ha contribuido a elevar los estándares de calidad y seguridad en la atención médica.
Tecnología
En el sector tecnológico, la Ingeniería Industrial ha encontrado nuevas aplicaciones. La gestión de proyectos de software se ha beneficiado de las metodologías de optimización y control de procesos. Un área en crecimiento es la aplicación del Big Data y su aplicación en la ingeniería industrial para optimizar operaciones.
Impacto de la Ingeniería Industrial en diferentes sectores:
Sector | Aplicaciones Principales | Impacto |
---|---|---|
Manufactura | Optimización de líneas, control de calidad | Aumento de productividad, reducción de costos |
Logística | Diseño de cadenas de suministro, optimización de rutas | Eficiencia en distribución, reducción de tiempos |
Servicios | Mejora de procesos, gestión de colas | Aumento de satisfacción del cliente |
Salud | Flujo de pacientes, gestión de recursos | Mejora en calidad de atención, reducción de esperas |
Tecnología | Gestión de proyectos, optimización de centros de datos | Eficiencia en desarrollo, ahorro energético |
Este impacto multifacético también se traduce en diversas oportunidades profesionales, incluyendo las áreas más rentables en ingeniería industrial y aplicaciones innovadoras como el liderazgo deportivo y su aplicación en la ingeniería industrial
Herramientas y Metodologías Clave
La Ingeniería Industrial se ha enriquecido con una serie de metodologías y herramientas que han transformado la forma en que se abordan los problemas en diversos sectores. Para una visión más detallada de los fundamentos, explora las herramientas y técnicas básicas en ingeniería industrial.
- Six Sigma, desarrollada por Motorola en los años 80, se ha convertido en una de las metodologías más influyentes... Estas metodologías requieren el uso de diversos programas más utilizados en ingeniería industrial para su implementación efectiva.
- Lean Manufacturing, inspirada en el Sistema de Producción Toyota, se ha convertido en un pilar de la eficiencia en la producción. Esta metodología se enfoca en eliminar desperdicios, definidos como cualquier actividad que no agrega valor desde la perspectiva del cliente. Lean promueve un flujo continuo de producción, el uso de sistemas pull y la mejora continua. Su implementación ha llevado a reducciones dramáticas en los tiempos de producción, inventarios y costos, mientras mejora la calidad y la satisfacción del cliente.
- La Teoría de Restricciones, desarrollada por Eliyahu Goldratt, ofrece un enfoque sistemático para identificar y gestionar los cuellos de botella... La aplicación de estas metodologías modernas a menudo se potencia con el análisis de Big Data y su aplicación en la ingeniería industrial.
- Kaizen, que significa "mejora continua" en japonés, es una filosofía que ha transformado la cultura organizacional en muchas empresas. Kaizen promueve la idea de que pequeñas mejoras incrementales, realizadas constantemente, pueden llevar a grandes cambios positivos con el tiempo. Esta filosofía involucra a todos los empleados en el proceso de mejora, desde los trabajadores de línea hasta la alta gerencia, fomentando un sentido de propiedad y compromiso con la calidad y la eficiencia.
- La metodología 5S, también originaria de Japón, se enfoca en la organización y mantenimiento de espacios de trabajo eficientes y productivos. Las 5S representan cinco palabras japonesas que comienzan con S: Seiri (clasificar), Seiton (ordenar), Seiso (limpiar), Seiketsu (estandarizar) y Shitsuke (mantener). Esta metodología no solo mejora la eficiencia y la productividad, sino que también contribuye a crear un ambiente de trabajo más seguro y agradable.
Comparación de metodologías clave:
Metodología | Enfoque Principal | Beneficios Clave |
---|---|---|
Six Sigma | Reducción de defectos | Mejora de calidad, reducción de costos |
Lean Manufacturing | Eliminación de desperdicios | Eficiencia, reducción de tiempos |
Teoría de Restricciones | Gestión de cuellos de botella | Aumento de throughput |
Kaizen | Mejora continua | Cultura de mejora, participación de empleados |
5S | Organización del espacio de trabajo | Eficiencia, seguridad |
Adaptación a la Era Digital en el Siglo XXI
El siglo XXI ha traído consigo una nueva era digital en la que la Ingeniería Industrial ha tenido que adaptarse. La automatización y la inteligencia artificial se han convertido en elementos clave en la disciplina.
La automatización ha permitido la implementación de sistemas y maquinaria que realizan tareas repetitivas y predefinidas de manera eficiente y precisa. Esto ha mejorado la eficiencia y la velocidad en las tareas de producción, reduciendo los errores humanos y los costos laborales.
Por otro lado, la inteligencia artificial ha permitido a la Ingeniería Industrial realizar análisis predictivos y optimización de recursos más complejos. La toma de decisiones basada en datos y el aprendizaje automático han mejorado la capacidad de la disciplina para adaptarse a los cambios y tomar decisiones más informadas.
El análisis de datos también se ha vuelto fundamental en la Ingeniería Industrial en la era digital. La recolección y el análisis de grandes cantidades de datos permiten identificar patrones, tendencias y oportunidades de mejora en los procesos de producción.
Además de estos avances tecnológicos, la Ingeniería Industrial en el siglo XXI también ha puesto un fuerte enfoque en la sostenibilidad y la responsabilidad social. La disciplina busca implementar prácticas ecoeficientes y reducir el impacto ambiental en los procesos industriales.
Industria 4.0 y su Impacto en la Ingeniería Industrial
La Industria 4.0 está revolucionando la Ingeniería Industrial, impulsando la automatización, la conectividad y la optimización de procesos en las fábricas inteligentes. Esta nueva era se caracteriza por la fusión de tecnologías avanzadas, como la inteligencia artificial (IA), el Internet de las Cosas (IoT) y los gemelos digitales, transformando la manera en que se diseñan, producen y gestionan los sistemas industriales.
Transformación Digital en la Ingeniería Industrial
Los ingenieros industriales están adoptando tecnologías ciberfísicas para mejorar la productividad y la eficiencia en la manufactura. La integración de sensores inteligentes y algoritmos de control en tiempo real permite una monitorización precisa de los procesos, reduciendo tiempos de inactividad y optimizando el uso de recursos.
Automatización y Robótica en la Producción
La automatización y la robótica avanzada están redefiniendo las líneas de producción. Robots colaborativos (cobots) trabajan junto a operarios humanos para mejorar la seguridad y la eficiencia, mientras que los sistemas de automatización industrial permiten fabricar productos con mayor precisión y menor costo.
Inteligencia Artificial para la Optimización de Procesos
La IA y el aprendizaje automático analizan grandes volúmenes de datos para identificar patrones y mejorar la gestión de la producción, la planificación logística y el control de calidad. Estas tecnologías permiten tomar decisiones basadas en datos en tiempo real, optimizando la cadena de suministro y reduciendo desperdicios.
IoT y Conectividad en la Industria
El Internet de las Cosas (IoT) facilita la interconexión de dispositivos y sistemas industriales, proporcionando información en tiempo real sobre mantenimiento predictivo, calidad del producto y eficiencia operativa. Los ingenieros industriales pueden anticiparse a fallos, mejorar la trazabilidad y optimizar el rendimiento de las máquinas.
Gemelos Digitales y Simulación de Procesos
Los gemelos digitales están revolucionando la ingeniería industrial al permitir simulaciones avanzadas de productos y procesos antes de su implementación real. Esto facilita la detección de fallos, el ahorro de costos y la optimización del diseño de sistemas industriales.
Fabricación Aditiva e Innovación en la Producción
La impresión 3D está impulsando la personalización masiva y la producción bajo demanda. Los ingenieros industriales están integrando la fabricación aditiva en procesos tradicionales para desarrollar prototipos rápidos y piezas personalizadas, reduciendo costos y tiempos de producción.
Sostenibilidad y Eficiencia Energética
La Industria 4.0 también está promoviendo la sostenibilidad en la manufactura, optimizando el uso de materiales y energía. Los sistemas inteligentes ayudan a reducir el impacto ambiental, alineando la producción con estrategias ecológicas y eficientes.
Tecnologías de la Industria 4.0 en Ingeniería Industrial:
Tecnología | Aplicación en Ingeniería Industrial | Beneficio |
---|---|---|
IoT | Monitoreo en tiempo real | Toma de decisiones informada |
IA y Machine Learning | Análisis predictivo, optimización | Mejora en eficiencia y calidad |
Fabricación Aditiva | Prototipado rápido, personalización | Flexibilidad en producción |
Realidad Aumentada | Capacitación, mantenimiento | Reducción de errores, mejora en seguridad |
Gemelos Digitales | Simulación, optimización | Reducción de riesgos, mejora en diseño |
El Futuro de la Ingeniería Industrial
Impacto en Diferentes Industrias
Sector | Aplicación | Resultado |
---|---|---|
Manufactura | Robots en líneas de ensamblaje | +30% productividad (ej.: Foxconn) |
Salud | Modelos predictivos para camas hospitalarias | Reducción de tiempos de espera en 50% |
Logística | Ruteo inteligente con IA | -20% costos de transporte (Amazon) |
A medida que nos adentramos en la tercera década del siglo XXI, el futuro de la Ingeniería Industrial se perfila como un campo lleno de desafíos emocionantes y oportunidades transformadoras. Las tendencias emergentes y los cambios en el panorama global están configurando una nueva era para la disciplina.
Mayor énfasis en la sostenibilidad y la economía circular.
Uno de los aspectos más prominentes en el futuro de la Ingeniería Industrial es el creciente énfasis en la sostenibilidad y la economía circular. Los ingenieros industriales están llamados a desempeñar un papel crucial en la transición hacia procesos de producción más sostenibles y respetuosos con el medio ambiente. Esto implica no solo la optimización de recursos y la reducción de residuos, sino también el rediseño fundamental de productos y procesos para minimizar su impacto ambiental a lo largo de todo su ciclo de vida. La implementación de principios de economía circular, donde los productos se diseñan para ser reutilizados o reciclados al final de su vida útil, se está convirtiendo en una competencia esencial para los ingenieros industriales.
Integración de la realidad aumentada y virtual en el diseño y la capacitación.
La integración de tecnologías de realidad aumentada (RA) y realidad virtual (RV) está transformando tanto el diseño como la capacitación en la Ingeniería Industrial. Estas tecnologías permiten a los ingenieros visualizar y manipular modelos 3D complejos de productos y procesos antes de su implementación física. En el ámbito de la capacitación, la RA y RV ofrecen entornos de aprendizaje inmersivos y seguros, permitiendo a los trabajadores practicar tareas complejas o peligrosas sin riesgos reales.
Adaptación a modelos de trabajo remotos y colaborativos.
La adaptación a modelos de trabajo remotos y colaborativos se ha acelerado significativamente en los últimos años y se espera que continúe siendo una tendencia importante. Los ingenieros industriales deben desarrollar habilidades para gestionar equipos distribuidos geográficamente y coordinar proyectos a través de plataformas digitales. Esto implica no solo el dominio de herramientas de colaboración en línea, sino también la capacidad de fomentar la innovación y mantener la productividad en entornos de trabajo híbridos.
Gestión de la ciberseguridad en sistemas industriales conectados.
La ciberseguridad se está convirtiendo en una preocupación crítica a medida que los sistemas industriales se vuelven más interconectados y dependientes de la tecnología digital. Los ingenieros industriales del futuro deberán integrar consideraciones de seguridad cibernética en cada etapa del diseño y la operación de sistemas industriales. Esto implica no solo proteger contra amenazas externas, sino también asegurar la integridad y confiabilidad de los datos utilizados en la toma de decisiones y el control de procesos. La colaboración con especialistas en ciberseguridad será cada vez más crucial para desarrollar sistemas robustos y resistentes a ataques.
Desarrollo de habilidades para trabajar junto a sistemas autónomos y robots
El desarrollo de habilidades para trabajar junto a sistemas autónomos y robots es otra área clave para el futuro de la Ingeniería Industrial. A medida que la automatización avanza, los ingenieros industriales deberán adaptarse a un entorno de trabajo donde los robots y los humanos colaboran estrechamente. Esto implica no solo comprender las capacidades y limitaciones de los sistemas autónomos, sino también diseñar procesos y espacios de trabajo que faciliten una interacción segura y eficiente entre humanos y máquinas. Además, los ingenieros industriales tendrán que abordar los desafíos éticos y sociales que surgen con la creciente automatización, como el desplazamiento laboral y la necesidad de recapacitación de la fuerza laboral.
Habilidades futuras para Ingenieros Industriales:
Categoría | Habilidades |
---|---|
Técnicas | Análisis de datos, IA, Ciberseguridad |
Blandas | Adaptabilidad, Pensamiento crítico, Comunicación |
Gestión | Liderazgo ágil, Gestión de cambios, Colaboración virtual |
Sostenibilidad | Diseño para economía circular, Gestión de recursos |
Interdisciplinarias | Conocimientos en biología, psicología, informática |
Tendencias Clave en la Ingeniería Industrial Actual
La Ingeniería Industrial sigue evolucionando y adaptándose a las nuevas tendencias y desafíos de la industria.
Una de las tendencias clave es la automatización, que continúa transformando los procesos industriales al permitir la realización de tareas de manera rápida, precisa y eficiente.
Otra tendencia importante es la aplicación de inteligencia artificial en la Ingeniería Industrial. La inteligencia artificial permite la toma de decisiones más complejas, el aprendizaje automático y la adaptabilidad en los procesos de producción.
El análisis de datos también es fundamental en la Ingeniería Industrial actual. El uso de datos y análisis predictivos permite identificar patrones, tomar decisiones más informadas y optimizar los procesos de producción y gestión empresarial.
Por último, la Ingeniería Industrial actual se centra cada vez más en la sostenibilidad y la responsabilidad social. Se busca implementar prácticas ecoeficientes, reducir el desperdicio de recursos y minimizar el impacto ambiental en los procesos industriales.
Tabla: Comparación de Automatización e Inteligencia Artificial
La siguiente tabla compara los aspectos clave de la automatización y la inteligencia artificial en la Ingeniería Industrial:
Característica | Automatización | Inteligencia Artificial |
---|---|---|
Capacidad | Tareas repetitivas y predefinidas | Aprendizaje y toma de decisiones complejas |
Aplicaciones | Producción en masa, control de procesos | Análisis predictivo, optimización de recursos |
Impacto | Eficiencia y velocidad en las tareas | Adaptabilidad y autonomía en la toma de decisiones |
Innovación en Sostenibilidad
La Ingeniería Industrial también se ha centrado en promover prácticas responsables en la industria. Se busca implementar procesos ecoeficientes, reducir el consumo de recursos y minimizar el impacto ambiental.
La implementación de procesos ecoeficientes y la utilización de tecnologías más limpias y sostenibles son fundamentales para garantizar un desarrollo industrial responsable y respetuoso con el medio ambiente.
Desafíos y Oportunidades
La Ingeniería Industrial enfrenta desafíos y oportunidades en la era digital. Una de las principales oportunidades es la incorporación de tecnologías emergentes en los procesos industriales, lo que permite mejorar la eficiencia y la productividad.
Sin embargo, también existen desafíos, como el equilibrio entre eficiencia y ética en la automatización. Es importante asegurarse de que los avances tecnológicos no tengan un impacto negativo en los trabajadores o en el medio ambiente.
Conclusión
La Ingeniería Industrial ha experimentado una evolución significativa a lo largo de los años, desde la Revolución Industrial hasta la era digital. La disciplina ha jugado un papel fundamental en la mejora de la eficiencia operativa, la gestión empresarial y la innovación tecnológica.
En la actualidad, la Ingeniería Industrial sigue siendo clave en el desarrollo de procesos industriales eficientes y responsables, adaptándose a las nuevas tendencias y desafíos de la industria. La automatización, la inteligencia artificial y el análisis de datos son tendencias clave en la disciplina, al igual que el enfoque en la sostenibilidad y la responsabilidad social.
Preguntas frecuentes
1. ¿Qué diferencia a la ingeniería industrial de otras ingenierías?
Se enfoca en sistemas integrales (humanos, máquinas, procesos), mientras que otras se especializan en áreas técnicas específicas.
2. ¿Cómo contribuye a la sostenibilidad?
Optimiza el uso de energía, reduce residuos y promueve la economía circular.
3. ¿Qué habilidades necesita un ingeniero industrial hoy?
-Analítica de datos, manejo de IA, pensamiento sistémico y adaptabilidad.
4. ¿Qué empresas lideran la aplicación de Industria 4.0?
Siemens, General Electric y Bosch son referentes en fábricas inteligentes.
5. ¿Qué software usan los ingenieros industriales hoy?
- AutoCAD (diseño), Simio (simulación), Minitab (análisis estadístico).
Deja una respuesta
Te Puede Interesar: