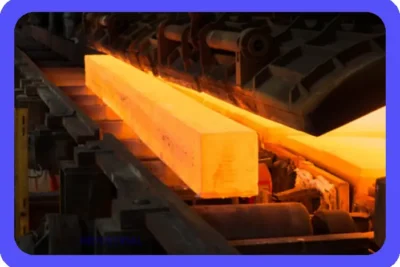
Equilibrio de Línea: Clave para la eficiencia en producción
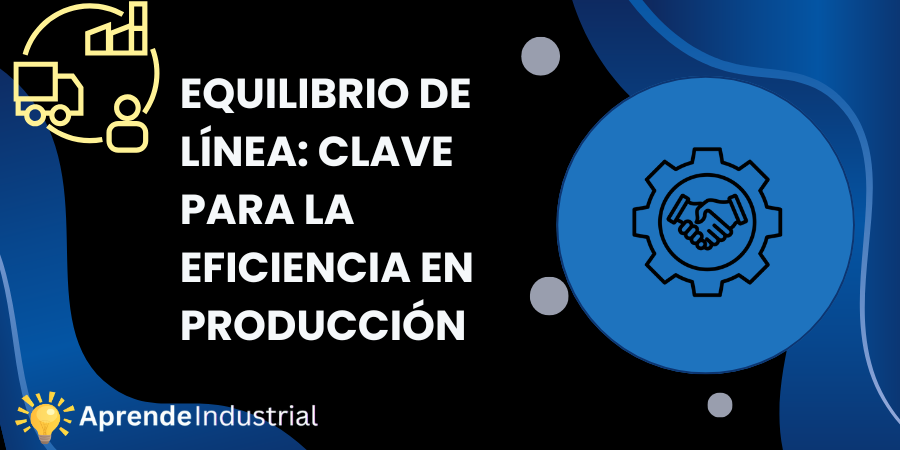
El equilibrio de línea es un concepto fundamental en la ingeniería industrial, especialmente en el contexto de las líneas de ensamblaje. Se refiere a la forma en que se distribuye el trabajo entre los operadores para maximizar la eficiencia y minimizar el tiempo de inactividad. En un entorno de producción, un buen equilibrio de línea puede ser la diferencia entre cumplir con los plazos de entrega y enfrentar retrasos significativos. La correcta distribución de tareas no solo mejora la productividad, sino que también contribuye a un ambiente de trabajo más armonioso y menos estresante para los empleados.
Este artículo tiene como objetivo proporcionar una guía completa sobre la implementación del equilibrio de línea en las líneas de producción. A lo largo del texto, se explorarán las métricas clave que se deben considerar, los pasos necesarios para implementar esta metodología, los beneficios que se pueden obtener y los desafíos que pueden surgir en el proceso. Al final, se espera que los lectores tengan una comprensión clara de cómo el equilibrio de línea puede transformar sus operaciones de producción.
Requisitos Previos
Antes de embarcarse en la implementación del equilibrio de línea, es esencial contar con ciertos conocimientos y herramientas. En primer lugar, es fundamental tener una comprensión básica de los principios de la ingeniería industrial y de la gestión de operaciones. Esto incluye familiarizarse con conceptos como el tiempo de ciclo, el tiempo de tacto y la capacidad de producción. Sin este conocimiento, será difícil aplicar efectivamente las técnicas de equilibrio de línea.
Takt Time: Definición, cálculo y su importancia en producciónAdemás, se recomienda contar con herramientas de software que faciliten el análisis y la simulación de la línea de producción. Programas como Microsoft Excel, AutoCAD o software especializado en simulación de procesos pueden ser de gran ayuda. Estas herramientas permiten modelar la línea de producción, realizar cálculos de tiempos y evaluar diferentes escenarios de distribución de tareas.
Por último, es importante tener acceso a datos históricos de producción. Estos datos son cruciales para entender el rendimiento actual de la línea y para establecer una línea base a partir de la cual se puedan medir las mejoras. Sin datos precisos, cualquier esfuerzo por equilibrar la línea puede ser en vano.
Pasos de Implementación
La implementación del equilibrio de línea puede parecer un proceso complejo, pero se puede desglosar en pasos manejables. A continuación, se presentan los pasos clave para llevar a cabo esta metodología.
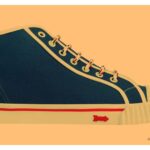
1. Análisis de la Línea de Producción
El primer paso en la implementación del equilibrio de línea es realizar un análisis exhaustivo de la línea de producción actual. Esto implica observar cómo se distribuyen las tareas entre los operadores y cuánto tiempo se tarda en completar cada tarea. Se recomienda utilizar herramientas de mapeo de procesos para visualizar el flujo de trabajo.
Ejemplo Práctico
Supongamos que una línea de ensamblaje de automóviles tiene tres estaciones de trabajo: montaje de motor, instalación de ruedas y pintura. Se debe registrar el tiempo que cada operador tarda en completar su tarea. Por ejemplo, si el tiempo de ciclo para el montaje de motor es de 10 minutos, para la instalación de ruedas es de 5 minutos y para la pintura es de 15 minutos, se debe documentar esta información.
2. Cálculo del Tiempo de Tacto
Una vez que se ha realizado el análisis de la línea de producción, el siguiente paso es calcular el tiempo de tacto. Este tiempo se define como el tiempo disponible para producir un producto dividido por la demanda del cliente. La fórmula es la siguiente:
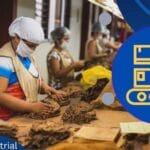
html
Tiempo de Tacto = Tiempo Disponible / Demanda
Ejemplo Matemático
Si una planta tiene 480 minutos disponibles en un turno y la demanda es de 40 unidades, el tiempo de tacto sería:
html
Tiempo de Tacto = 480 minutos / 40 unidades = 12 minutos por unidad
Este cálculo es crucial, ya que establece el ritmo al que deben trabajar los operadores para cumplir con la demanda.
3. Distribución de Tareas
Con el tiempo de tacto calculado, el siguiente paso es distribuir las tareas entre los operadores de manera que se minimicen los tiempos de inactividad y se maximice la eficiencia. Esto implica agrupar tareas que se pueden realizar en un tiempo similar al tiempo de tacto.
Ejemplo de Distribución
Siguiendo el ejemplo anterior, si el tiempo de tacto es de 12 minutos, se debe agrupar las tareas de manera que cada operador tenga un tiempo de trabajo cercano a este valor. Si un operador tarda 10 minutos en montar el motor y otro 5 minutos en instalar las ruedas, se puede ajustar la distribución de tareas para que ambos operadores trabajen en conjunto y se completen las tareas en un tiempo más equilibrado.
Beneficios y Desafíos
Implementar el equilibrio de línea no solo trae consigo una serie de beneficios, sino que también presenta desafíos que deben ser abordados.
Beneficios
Uno de los principales beneficios del equilibrio de línea es la mejora en la productividad. Al distribuir las tareas de manera equitativa, se reduce el tiempo de inactividad y se maximiza el uso de los recursos. Esto se traduce en una mayor producción en menos tiempo.
Otro beneficio es la reducción del estrés laboral. Cuando las tareas están equilibradas, los operadores no se sienten abrumados por una carga de trabajo desigual. Esto puede llevar a un ambiente de trabajo más positivo y a una mayor satisfacción laboral.
Desafíos
Sin embargo, la implementación del equilibrio de línea no está exenta de desafíos. Uno de los principales obstáculos es la resistencia al cambio por parte de los empleados. Es común que los trabajadores se sientan cómodos con sus rutinas actuales y se muestren reacios a adoptar nuevas formas de trabajo.
Otro desafío es la variabilidad en la demanda. Si la demanda de producción fluctúa, puede ser difícil mantener un equilibrio constante en la línea. Es importante tener en cuenta estas variaciones y estar preparado para ajustar la distribución de tareas según sea necesario.
Ejemplos de Implementación Exitosa
A lo largo de la historia, muchas empresas han implementado con éxito el equilibrio de línea y han visto mejoras significativas en su producción. Un ejemplo notable es el caso de Toyota, que ha utilizado principios de equilibrio de línea en su sistema de producción Just-in-Time. Al optimizar la distribución de tareas, Toyota ha logrado reducir los tiempos de espera y mejorar la eficiencia general de su producción.
Otro ejemplo es el de Ford, que ha implementado el equilibrio de línea en sus fábricas de ensamblaje. Al analizar y ajustar la distribución de tareas, Ford ha logrado aumentar su capacidad de producción y reducir los costos operativos.
Herramientas y Técnicas para el Equilibrio de Línea
Existen diversas herramientas y técnicas que pueden facilitar la implementación del equilibrio de línea. Algunas de las más comunes incluyen:
1. Diagramas de Gantt
Los diagramas de Gantt son una herramienta visual que permite planificar y programar tareas. Al utilizar un diagrama de Gantt, los gerentes pueden ver de un vistazo cómo se distribuyen las tareas a lo largo del tiempo y realizar ajustes según sea necesario.
2. Software de Simulación
El uso de software de simulación puede ser extremadamente útil para modelar diferentes escenarios de equilibrio de línea. Herramientas como Arena o Simul8 permiten a los gerentes experimentar con diferentes distribuciones de tareas y evaluar su impacto en la producción.
3. Análisis de Pareto
El análisis de Pareto es una técnica que se utiliza para identificar las tareas que tienen el mayor impacto en la producción. Al enfocarse en estas tareas clave, los gerentes pueden realizar ajustes que generen mejoras significativas en el equilibrio de línea.
Conclusión
El equilibrio de línea es una metodología esencial para mejorar la eficiencia en la producción. A través de un análisis cuidadoso y una distribución equitativa de las tareas, las empresas pueden maximizar su productividad y crear un ambiente de trabajo más positivo. Aunque existen desafíos en la implementación, los beneficios superan con creces las dificultades.
Es fundamental que los ingenieros industriales y los gerentes de producción comprendan la importancia del equilibrio de línea y estén dispuestos a invertir el tiempo y los recursos necesarios para implementarlo. Al hacerlo, no solo mejorarán sus operaciones, sino que también contribuirán a un entorno laboral más saludable y eficiente.
Referencias
- Cómo medir el equilibrio de la línea de producción ... - LinkedIn
- Qué es el equilibrio de líneas y cómo conseguirlo | Tulip
- ¿QUÉ ES BALANCEO DE LÍNEAS?
Deja una respuesta
Te Puede Interesar: