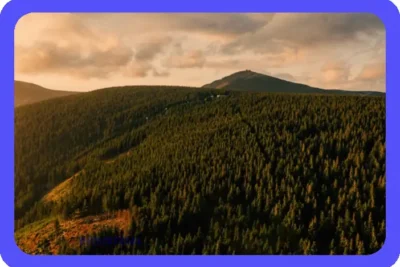
Tipos de Ensayos No Destructivos: Guía Completa
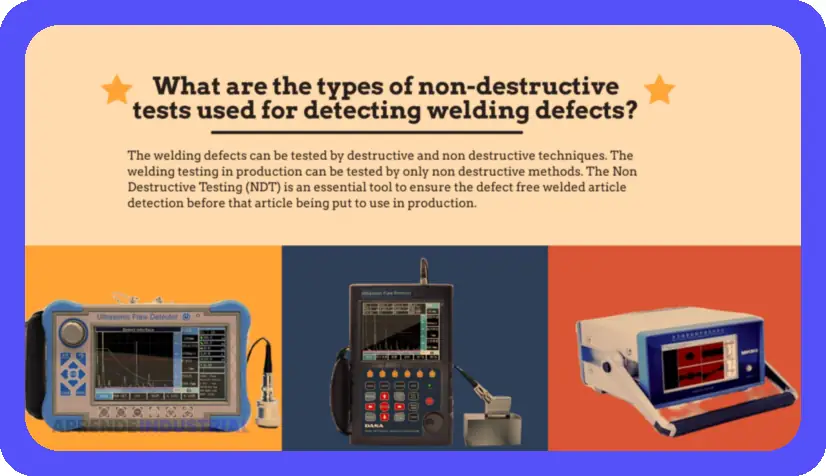
Los ensayos no destructivos (END) son un conjunto de técnicas esenciales en la industria moderna. Permiten evaluar la integridad y calidad de materiales, componentes y estructuras sin causarles daño. Esto es crucial, ya que los métodos tradicionales de prueba, a menudo destructivos, pueden resultar costosos y, en algunos casos, imposibles. Los ensayos no destructivos son, por tanto, herramientas indispensables para garantizar la seguridad y la fiabilidad de los productos. Imaginen tener que romper cada pieza de un avión para comprobar su resistencia: ¡sería impensable! Los END nos permiten verificar la calidad sin este sacrificio.
Este artículo explorará en detalle los diferentes métodos de ensayos no destructivos, sus principios físicos, sus aplicaciones en diversas industrias y sus limitaciones. Aprenderemos sobre los beneficios que ofrecen estos métodos y cómo contribuyen a la eficiencia y seguridad en diferentes sectores. Abarcaremos una amplia gama de técnicas, desde las más sencillas hasta las más complejas, ofreciendo una visión completa de esta disciplina fundamental en la ingeniería y el control de calidad.
- Métodos de Ensayos No Destructivos: Inspección Visual
- Líquidos Penetrantes: Un método visual mejorado
- Ensayos No Destructivos por Ultrasonido
- Ensayos No Destructivos por Partículas Magnéticas
- Ensayos No Destructivos con Corrientes Inducidas
- Ensayos No Destructivos con Radiaciones Ionizantes (Radiografía y Tomografía Computarizada)
- Comparación de los Métodos de Ensayos No Destructivos
- Conclusión
- Preguntas Frecuentes
Métodos de Ensayos No Destructivos: Inspección Visual
Método | Ventajas | Desventajas |
---|---|---|
Inspección Visual Directa | Simple, rápida y económica; no requiere equipo especializado; permite detectar defectos superficiales grandes. | Limitada a la superficie accesible; subjetiva y dependiente del inspector; puede ser inexacta para defectos pequeños o ocultos. |
Inspección Visual con Instrumentos de Aumento (lupas, microscopios) | Permite la detección de defectos más pequeños que la inspección visual directa; mayor precisión. | Requiere equipo especializado; más costosa que la inspección visual directa; accesibilidad limitada a áreas visibles. |
Endoscopia | Permite la inspección de áreas inaccesibles; proporciona imágenes detalladas. | Equipo especializado costoso; requiere entrenamiento específico para su operación e interpretación de imágenes; puede ser lenta. |
Boroscopios | Inspección de cavidades y espacios confinados; imágenes en tiempo real. | Limitaciones en la resolución dependiendo del equipo; requiere entrenamiento; puede ser afectado por la iluminación. |
Fotografía y Videografía | Registro permanente de la inspección; permite análisis posterior detallado; facilita la comunicación y colaboración. | Requiere equipo especializado; el análisis de las imágenes puede requerir personal especializado; el costo del equipo puede ser elevado. |
La inspección visual es el método de ensayos no destructivos más simple y común. Se basa en la observación directa del componente o estructura para detectar defectos superficiales, como grietas, corrosión, abolladuras o deformaciones. Aunque aparentemente simple, requiere una buena iluminación, un enfoque detallado y, en ocasiones, el uso de herramientas como lupas, endoscopios o boroscopios para acceder a zonas de difícil visibilidad. Por ejemplo, en la construcción, la inspección visual de las soldaduras es fundamental para detectar posibles fisuras antes de que se conviertan en un problema mayor. Además, un buen inspector visual debe tener un conocimiento profundo de los materiales y los posibles defectos que pueden presentarse.
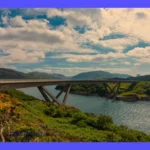
Una inspección visual efectiva también incluye la documentación fotográfica o videográfica para un registro preciso y una posterior comparación. Este método es especialmente útil en las etapas iniciales de una inspección, ya que puede descartar la necesidad de pruebas más complejas y costosas si no se detectan anomalías significativas. A menudo sirve como punto de partida para decidir qué otro tipo de ensayos no destructivos se deben realizar. Además, el uso de herramientas de aumento como lupas o microscopios puede mejorar considerablemente la capacidad de detección de defectos superficiales pequeños.
La formación del personal para realizar inspecciones visuales eficaces es crucial. Un inspector capacitado puede identificar una gran variedad de anomalías superficiales que podrían pasar desapercibidas a simple vista. Además, un buen plan de inspección visual debe incluir criterios específicos y listas de verificación para garantizar la consistencia y la cobertura completa de la superficie inspeccionada. La documentación del proceso es también esencial para asegurar la trazabilidad.
Líquidos Penetrantes: Un método visual mejorado
Tipo de Líquido Penetrante | Ventajas | Desventajas |
---|---|---|
Fluorescente | Alta sensibilidad, fácil detección bajo luz UV, ampliamente disponible. | Requiere una cámara oscura para la inspección, puede ser afectado por la contaminación fluorescente. |
Visible (Colorante) | No requiere equipo especial para la inspección (luz UV), inspección más rápida. | Menor sensibilidad que los fluorescentes, mayor dificultad en la detección de pequeñas grietas. |
Solventes Limpiadores | Remueve el exceso de penetrante de manera eficiente. | Puede remover parte del penetrante atrapado en las grietas si se utiliza incorrectamente. |
Revelador | Ayuda a sacar el penetrante de las grietas a la superficie para facilitar la visualización. | Puede enmascarar grietas pequeñas si se aplica en exceso o incorrectamente. |
Los líquidos penetrantes son otro método ampliamente usado de ensayos no destructivos. Este método es ideal para detectar pequeñas grietas superficiales en materiales no porosos. El procedimiento implica aplicar un líquido penetrante a la superficie, permitiendo que penetre en cualquier grieta presente, retirar el exceso y aplicar un revelador que absorbe el líquido de las grietas, haciéndolas visibles. Es un proceso sencillo pero efectivo para descubrir fallas ocultas a simple vista.
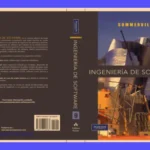
Por ejemplo, este método se utiliza en la industria aeronáutica para detectar grietas en las alas de los aviones. Las grietas, aunque pequeñas, pueden ser un factor de riesgo significativo si no se detectan a tiempo. La elección del líquido penetrante y el revelador dependerá del material que se esté inspeccionando. También es importante un proceso de limpieza meticulosa antes de la aplicación del líquido penetrante para asegurar una buena penetración y evitar falsos resultados. Después de la aplicación del revelador, la superficie se inspecciona visualmente en busca de indicios del líquido penetrante que ha salido de las grietas.
La sensibilidad del método depende de varios factores, incluyendo la viscosidad del líquido penetrante, el tiempo de penetración y la calidad del revelador. Los líquidos penetrantes fluorescentes son especialmente útiles bajo luz ultravioleta, aumentando considerablemente la visibilidad de las grietas. A pesar de su simplicidad, los líquidos penetrantes requieren un entrenamiento adecuado para su aplicación e interpretación de los resultados. Un mal procedimiento puede llevar a conclusiones erróneas sobre la existencia de defectos.
Ensayos No Destructivos por Ultrasonido
Técnica | Descripción y Aplicación |
---|---|
Método de transmisión | Mide la atenuación de la onda ultrasónica al atravesar el material. Se utiliza para detectar discontinuidades internas como grietas, porosidades o inclusiones. Es eficaz en la detección de defectos en materiales relativamente homogéneos y delgados. |
Método de reflexión | Detecta las reflexiones de la onda ultrasónica en las interfaces o discontinuidades. Es ampliamente utilizado para detectar defectos superficiales y subsuperficiales en una gran variedad de materiales, incluyendo metales, plásticos y compuestos. Permite una mayor precisión en la localización de defectos que el método de transmisión. |
Método de eco | Un tipo específico del método de reflexión que utiliza un solo transductor para emitir y recibir las ondas ultrasónicas. Es común en inspecciones portátiles y de campo. Proporciona una imagen sencilla del material y la ubicación de los defectos. |
Método de onda de cizallamiento | Utiliza ondas de cizallamiento (ondas S) para inspeccionar materiales, especialmente aquellos sensibles a las tensiones residuales. Es útil en la detección de grietas finas y defectos orientados en planos específicos. |
Técnicas de haz focalizado | Emplean transductores especiales para concentrar la energía ultrasónica en un punto específico, mejorando la resolución y la penetración en áreas de interés. Útil para inspecciones de precisión en componentes complejos. |
Los ensayos no destructivos por ultrasonido utilizan ondas sonoras de alta frecuencia para detectar defectos internos en materiales. Un transductor emite ondas que se propagan a través del material; si encuentran una discontinuidad, como una grieta o una inclusión, parte de la energía se refleja. Mediante la recepción de estas ondas reflejadas, se puede determinar la ubicación, el tamaño y la naturaleza del defecto. Este método es particularmente útil para la inspección de materiales gruesos, como las piezas fundidas de motores de automóviles o las estructuras de puentes.
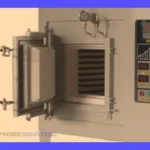
Imagine que una grieta se encuentra en el interior de una pieza metálica. La inspección visual no sería suficiente para detectar este defecto, pero las ondas ultrasónicas pueden penetrar y revelar la presencia de la discontinuidad, proporcionando una imagen interna del material. La técnica del ultrasonido permite realizar inspecciones en varias geometrías y materiales, pero la interpretación de los resultados requiere de experiencia y formación especializada. Diversas técnicas, como la reflexión, la transmisión y la atenuación, se utilizan dependiendo de la naturaleza del material y el tipo de defecto que se busca.
Además de la detección de defectos, el ultrasonido se puede utilizar para medir el espesor de los materiales, especialmente en aquellos con recubrimientos o capas. Este es un uso importante en las inspecciones de tuberías o tanques, donde la corrosión interna puede reducir el espesor de las paredes. La precisión del método se ve afectada por factores como la rugosidad superficial, la temperatura y la homogeneidad del material. Es crucial una correcta calibración del equipo para asegurar resultados confiables. La preparación de la superficie también es importante para obtener resultados precisos.
Ensayos No Destructivos por Partículas Magnéticas
El método de partículas magnéticas es un ensayo no destructivo utilizado para detectar defectos superficiales y subsuperficiales en materiales ferromagnéticos, es decir, aquellos que pueden ser magnetizados, como el acero. Consiste en magnetizar la pieza a inspeccionar y luego esparcir partículas magnéticas finas sobre la superficie. Estas partículas se acumularán en zonas donde existe una fuga de flujo magnético causada por un defecto, lo que hace visible la anomalía. Esta técnica es muy usada en la industria automotriz para detectar grietas en los ejes o los componentes metálicos.
Este método es relativamente simple y rápido, por lo que es económicamente viable para muchas aplicaciones. Sin embargo, sólo funciona en materiales ferromagnéticos. Para detectar defectos en otros materiales, es necesario emplear otros métodos de ensayos no destructivos. La calidad del resultado depende de la correcta magnetización de la pieza, la correcta distribución de las partículas magnéticas y la sensibilidad del observador.
La magnetización puede lograrse utilizando diferentes métodos, incluyendo la magnetización longitudinal, circular o con campos magnéticos pulsados. La elección del método depende de la geometría de la pieza y el tipo de defecto que se busca. Las partículas magnéticas pueden ser visibles o fluorescentes, mejorando la visibilidad de los defectos. Después de la inspección, la pieza debe ser desmagnetizada para evitar interferencias con otros equipos o procesos. Este paso es crucial en la prevención de daños en equipos sensibles.
Ensayos No Destructivos con Corrientes Inducidas
Los ensayos no destructivos con corrientes inducidas, también conocidos como ensayos por corrientes de Foucault, se basan en la generación de corrientes eléctricas en el material a inspeccionar mediante un campo magnético variable. Estas corrientes inducidas son sensibles a la presencia de defectos, variaciones en la conductividad eléctrica o cambios en las propiedades magnéticas del material. Se utiliza ampliamente en la industria aeronáutica para detectar grietas en componentes de las aeronaves.
Este método es especialmente útil para la detección de defectos superficiales y subsuperficiales en materiales conductores. Una bobina generadora crea un campo magnético alterno que induce corrientes en el material. Si hay un defecto, las corrientes inducidas se alteran, lo que se detecta mediante una bobina receptora. Este cambio en la señal se interpreta para indicar la presencia, tamaño y localización del defecto. La profundidad de penetración de las corrientes inducidas es un factor importante en este proceso y depende de la frecuencia del campo magnético y las propiedades del material.
Además de la detección de defectos, los ensayos no destructivos con corrientes inducidas se pueden usar para medir el espesor de los revestimientos, la dureza superficial y las propiedades de la conductividad eléctrica. La interpretación de los resultados requiere un análisis detallado de las señales obtenidas. Al igual que con otros métodos END, la preparación de la superficie puede ser crucial para obtener resultados precisos. El método es adaptable a diferentes formas geométricas y no requiere necesariamente contacto directo con el material, lo que lo convierte en una opción versátil.
Ensayos No Destructivos con Radiaciones Ionizantes (Radiografía y Tomografía Computarizada)
Las radiaciones ionizantes, como los rayos X o los rayos gamma, son muy usadas en los ensayos no destructivos para detectar defectos internos en materiales. La radiografía es un método clásico donde se pasa un haz de radiación a través de una muestra, y la atenuación de la radiación a su paso es captada en una película radiográfica. En una radiografía, se observan zonas más oscuras donde la radiación ha pasado con mayor facilidad (menor densidad del material) y zonas más claras donde la atenuación ha sido mayor (mayor densidad).
La tomografía computarizada (TC) es una técnica más sofisticada que crea una imagen tridimensional del interior del material. En la TC, el haz de radiación gira alrededor del material y un ordenador reconstruye una imagen de diferentes secciones transversales.
Las radiografías y la TC son ampliamente utilizadas en la industria para examinar materiales complejos, como piezas fundidas, soldaduras o materiales compuestos. En la industria aeronáutica, se usan para inspeccionar las uniones soldadas, garantizando la seguridad de las aeronaves. La radiografía también puede ser utilizada para detectar el grado de corrosión interna en tuberías o tanques, así como para la inspección de piezas de arte.
La seguridad es un factor esencial en el uso de estos métodos. Se debe contar con personal capacitado en manejo de fuentes radioactivas, así como equipo de protección personal adecuado para evitar la exposición a las radiaciones ionizantes.
Comparación de los Métodos de Ensayos No Destructivos
La selección del método de ensayos no destructivos adecuado depende de diversos factores, incluyendo el tipo de material, la geometría de la pieza, el tipo de defecto que se busca y la sensibilidad requerida. No existe un método universal que sea óptimo para todas las situaciones. La inspección visual, por ejemplo, es sencilla y económica, pero solo detecta defectos superficiales. En cambio, el ultrasonido es más costoso pero permite detectar defectos internos. Otros métodos tienen sus propias ventajas y desventajas.
A continuación, se presenta una tabla que compara brevemente algunos de los métodos más comunes:
| Método | Tipo de defecto detectado | Material | Ventajas | Desventajas |
|---------------------------------------|------------------------------------|-------------------------------------------|-------------------------------------------------------------------------|--------------------------------------------------------------------------|
| Inspección visual | Superficiales | Todos | Simple, económico, rápido | Limitado a defectos superficiales y visibles |
| Líquidos penetrantes | Superficiales, discontinuidades | No porosos | Sensible a pequeñas grietas | No detecta defectos internos |
| Ultrasonido | Internos y superficiales | Diversos | Alta sensibilidad, buena penetración en materiales gruesos | Requiere personal cualificado, preparación superficial puede ser compleja |
| Partículas magnéticas | Superficiales y subsuperficiales | Ferromagnéticos | Sencillo, rápido | Limitado a materiales ferromagnéticos |
| Corrientes inducidas (Foucault) | Superficiales y subsuperficiales | Conductores | Alta sensibilidad, rápido, sin contacto directo (a veces) | Limitado a materiales conductores |
| Radiografía y Tomografía Computarizada | Internos | Diversos | Detección de defectos internos complejos, imágenes detalladas | Costoso, requiere personal especializado, seguridad es fundamental |
Conclusión
Los ensayos no destructivos son herramientas esenciales en la industria para garantizar la seguridad y la calidad de los productos. La variedad de técnicas disponibles permite seleccionar la más adecuada para cada aplicación. Desde la simple inspección visual hasta las sofisticadas técnicas de radiografía industrial o ultrasonido, los ensayos no destructivos proporcionan información crucial sobre la integridad de los materiales sin causarles daño. La correcta aplicación de estos métodos y la interpretación de los resultados requieren de personal cualificado, lo que subraya la importancia de la formación y la experiencia en este campo. La comprensión de los principios físicos que rigen cada técnica, así como sus limitaciones, es fundamental para una aplicación exitosa de los ensayos no destructivos.
Entender las capacidades y las limitaciones de cada método de ensayos no destructivos es clave para tomar decisiones informadas y asegurar la calidad y la fiabilidad de las estructuras y componentes de diversos sectores industriales. A medida que las industrias continúan su evolución y demandan cada vez mayor precisión y seguridad, la importancia de los ensayos no destructivos solo continuará creciendo.
Preguntas Frecuentes
¿Qué es un ensayo no destructivo?
Es una técnica que permite evaluar la calidad y la integridad de un material sin dañarlo. Se usan para detectar defectos internos y superficiales.
¿Cuáles son las ventajas principales de los ensayos no destructivos?
Reducen costos al evitar la destrucción de muestras y permiten inspecciones periódicas sin dañar los materiales, maximizando la seguridad.
¿Qué tipo de industrias utilizan ensayos no destructivos?
Industrias automotriz, aeronáutica, construcción, energía y muchas otras que requieren altos estándares de calidad y seguridad.
¿Qué capacitación se necesita para realizar ensayos no destructivos?
La capacitación varía según la técnica específica, pero generalmente se requiere una formación específica para la operación y la interpretación de los resultados.
¿Son los ensayos no destructivos siempre perfectos?
No, la eficacia depende de varios factores como la preparación de la muestra, la experiencia del operador y las limitaciones propias de cada técnica.
Deja una respuesta
Te Puede Interesar: