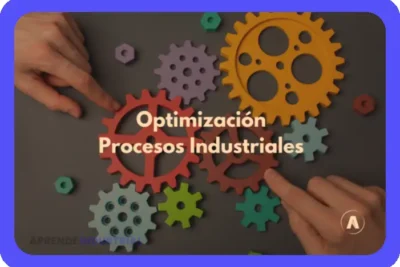
Diseño de planta: Guía para una distribución eficiente
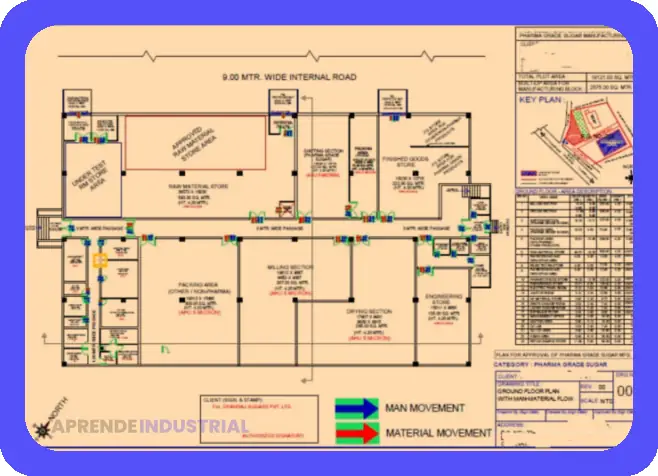
La distribución en planta es un factor crítico para el éxito de cualquier empresa, ya sea una fábrica, un almacén o una oficina. Se refiere a la planificación y disposición física de los recursos dentro de una instalación, incluyendo maquinaria, equipos, espacio de almacenamiento, áreas de trabajo y flujos de materiales. Una buena distribución en planta maximiza la eficiencia, la seguridad y la productividad, minimizando al mismo tiempo los costos y los tiempos de producción. Un diseño deficiente, por el contrario, puede llevar a cuellos de botella, movimientos innecesarios, accidentes y una baja moral de los empleados.
Este artículo explorará en detalle los aspectos clave de la distribución en planta, desde los principios básicos hasta las técnicas avanzadas de diseño y optimización. Aprenderemos cómo realizar un análisis de flujo de materiales, cómo seleccionar el diseño más apropiado para nuestras necesidades y cómo evaluar la eficiencia de una distribución existente. También examinaremos las diferentes metodologías y herramientas que se utilizan para diseñar y mejorar la distribución en planta, incluyendo el software de diseño asistido por computadora (CAD). El objetivo es proporcionar una guía completa y práctica para quienes buscan mejorar la eficiencia y la productividad de sus operaciones a través de una planificación estratégica de la distribución de la planta.
- Tipos de Distribuciones en Planta
- Análisis del Flujo de Materiales en la Distribución en Planta
- Diseño de la Distribución en Planta: Métodos y Herramientas
- Factores Clave a Considerar en el Diseño de Planta
- Implementación y Evaluación de la Distribución en Planta
- Herramientas de Software para el Diseño de Planta
- Consideraciones de Costos en el Diseño de Planta
- Conclusion
- Preguntas Frecuentes
Tipos de Distribuciones en Planta
Tipo de Distribución | Descripción y Características |
---|---|
Distribución por Procesos | Se agrupan las máquinas y equipos según el proceso de fabricación. Ideal para productos con procesos complejos o de alto volumen, pero puede generar cuellos de botella y tiempos de transporte largos. Ejemplo: Una línea de ensamblaje de automóviles. |
Distribución por Producto | Las máquinas y equipos se organizan según el producto final. Eficiente para productos estandarizados de alta producción, minimiza el movimiento de materiales, pero requiere alta inversión inicial y poca flexibilidad para cambios en la producción. Ejemplo: Fabricación de piezas de una sola línea de producto. |
Distribución por Posición Fija | El producto permanece en un lugar fijo y los recursos (materiales, equipos y personal) se desplazan hacia él. Ideal para productos grandes o pesados que no se pueden mover fácilmente, como la construcción de barcos o edificios. |
Distribución Celular (o por Grupo de Celdas) | Los equipos se agrupan en celdas que procesan familias de productos similares. Combina las ventajas de la distribución por producto y por proceso, ofreciendo mayor flexibilidad que la distribución por producto y menos cuellos de botella que la distribución por procesos. Ejemplo: Fabricación de productos con características similares, agrupando las máquinas necesarias para su proceso. |
Distribución Combinada | Combina dos o más tipos de distribución para optimizar la producción según las necesidades específicas. Permite una mayor flexibilidad y eficiencia que los tipos de distribución individuales. Ejemplo: Una fábrica que utiliza distribución por producto para una línea de alta producción y distribución por procesos para otra línea de productos personalizados. |
Existen diversos tipos de distribución en planta, cada uno con sus propias ventajas y desventajas. La selección del tipo de distribución dependerá de factores como el tipo de producto, el volumen de producción, el flujo de materiales y la tecnología utilizada. Por ejemplo, un taller de carpintería artesanal puede optar por una distribución por proceso, mientras que una fábrica de automóviles a gran escala podría preferir una distribución por producto o celular. A continuación, analizaremos algunos de los tipos más comunes:
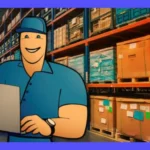
La distribución por producto es ideal para una producción masiva, donde los productos siguen una línea de montaje. La maquinaria y los empleados se organizan secuencialmente, optimizando el flujo de trabajo. En este caso, la distribución de la planta se centra en la eficiencia de la línea de producción. En cambio, la distribución por proceso agrupa maquinaria y equipos similares, independientemente del producto. Esta opción resulta ideal para talleres con baja producción y alta variedad.
La distribución por posición fija implica que el producto permanece estacionario mientras los trabajadores y equipos se desplazan a su alrededor. Este enfoque resulta adecuado para proyectos grandes y complejos, como la construcción de barcos o aviones. Por último, la distribución celular busca optimizar el flujo de trabajo mediante la agrupación de máquinas y equipos en celdas de producción, que procesan familias de productos similares. La distribución en planta celular es muy flexible y adaptable a los cambios en la demanda.
Una buena distribución en planta es crucial para evitar problemas a largo plazo. Un diseño inadecuado puede llevar a cuellos de botella, un desperdicio de recursos y una baja moral en los empleados, lo que afecta significativamente la rentabilidad.
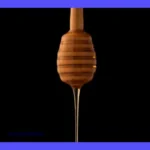
La selección del tipo de distribución es crucial para el éxito a largo plazo. Debe basarse en un análisis cuidadoso de las necesidades de la empresa. Se debe considerar la tecnología utilizada, el tipo de producto fabricado, así como también el volumen de producción.
Análisis del Flujo de Materiales en la Distribución en Planta
Etapa de Distribución | Tiempo de Ciclo (minutos) |
---|---|
Recepción de Materia Prima | 15 |
Almacenamiento de Materia Prima | 5 |
Transporte a Línea de Producción | 10 |
Proceso de Producción | 60 |
Almacenamiento de Producto Terminado | 8 |
Embalaje y Etiquetado | 12 |
Transporte a Zona de Despacho | 7 |
Despacho | 23 |
Antes de comenzar el diseño de la distribución en planta, es esencial realizar un análisis exhaustivo del flujo de materiales. Esto implica identificar todos los movimientos de materiales dentro de la instalación, desde la recepción de materias primas hasta el envío de productos terminados. El análisis debe considerar la secuencia de operaciones, las distancias recorridas y los tiempos de transporte.
Para realizar este análisis, existen diversas herramientas, como diagramas de flujo, diagramas de recorrido de materiales y matrices de relaciones. Los diagramas de flujo muestran la secuencia de operaciones y el flujo de materiales entre las diferentes áreas de la planta. Los diagramas de recorrido de materiales ilustran el movimiento físico de los materiales. Las matrices de relaciones muestran la relación entre las diferentes áreas de la planta, indicando la frecuencia y la importancia de los movimientos de materiales entre ellas.
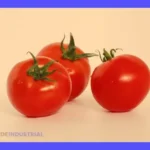
Por ejemplo, imagina una empresa que fabrica muebles. Analizando el flujo de materiales, podemos identificar que la madera entra por la recepción, pasa por el corte, el ensamblaje y luego al acabado antes de ir al almacén de productos terminados. Este análisis nos permite visualizar cuellos de botella potenciales y optimizar el proceso. Una buena distribución en planta busca minimizar las distancias recorridas por los materiales y reducir los tiempos de transporte.
Un diagrama de flujo bien diseñado puede revelar redundancias o procesos innecesarios. La eficiencia es un factor clave en una buena distribución en planta. Recuerda, un análisis cuidadoso del flujo de materiales es fundamental para una planificación exitosa.
Las herramientas de análisis permiten una planificación optimizada en el diseño de la distribución de la planta. La eficiencia se traduce en menores costos y mayor productividad.
Diseño de la Distribución en Planta: Métodos y Herramientas
Método | Herramienta/Software | Descripción |
---|---|---|
Diagrama de flujo de proceso | Software de dibujo (Visio, AutoCAD) | Representación gráfica del flujo de materiales y procesos en la planta. Permite identificar cuellos de botella y áreas de mejora. |
Diseño de celdas de manufactura | Software de simulación (Arena, AnyLogic) | Organización de máquinas y procesos en celdas según la familia de partes a procesar. Reduce tiempos de cambio y mejora el flujo. |
Análisis de relaciones entre departamentos (diagramas de relación) | Software de diseño de planta (Plant Design Suite, AutoCAD Plant 3D) | Identifica la proximidad ideal entre departamentos según su interacción. Utiliza matrices de relaciones para representar la importancia de la cercanía. |
Técnica de programación lineal | Software de optimización (LINGO, AMPL) | Método matemático para optimizar la ubicación de equipos y departamentos minimizando costos de transporte y maximizando la eficiencia. |
Simulación de eventos discretos | Software de simulación (Simio, Witness) | Modela el funcionamiento de la planta para evaluar diferentes diseños y predecir el rendimiento antes de su implementación. Permite probar diferentes escenarios. |
Método de ubicación ponderada | Hoja de cálculo (Excel) | Asigna pesos a diferentes factores de ubicación (proximidad a proveedores, mano de obra, etc.) para determinar la ubicación óptima de un nuevo equipo o departamento. |
El diseño de la distribución en planta es un proceso iterativo que implica la consideración de múltiples factores. Existen diversos métodos y herramientas para ayudar en este proceso. Algunas técnicas populares incluyen el diseño basado en bloques, el diseño basado en algoritmos y el uso de software CAD.
El diseño basado en bloques consiste en dividir la planta en bloques funcionales, asignando cada bloque a un área específica. Este método es especialmente útil para plantas grandes y complejas. El diseño basado en algoritmos utiliza algoritmos matemáticos para optimizar la disposición de las diferentes áreas. Estos algoritmos consideran factores como la distancia entre las áreas, el flujo de materiales y la capacidad de cada área.
El software CAD es una herramienta indispensable para el diseño de distribución en planta. Este software permite crear modelos tridimensionales de la planta, simulando el flujo de materiales y las operaciones. Además, permite realizar análisis de espacio, evaluar diferentes diseños y optimizar la disposición de la maquinaria y los equipos. Utilizar un software CAD permite visualizar rápidamente distintas soluciones antes de su implementación física, ahorrando tiempo y dinero.
Un software CAD facilita la visualización de diferentes escenarios. La correcta selección del software es vital para un análisis adecuado en el diseño de la distribución de la planta.
La experimentación con diferentes diseños es crucial. Las herramientas disponibles facilitan el proceso de diseño.
Factores Clave a Considerar en el Diseño de Planta
El diseño efectivo de la distribución en planta requiere considerar una serie de factores críticos, entre los que se incluyen el flujo de materiales, la ergonomía, la seguridad, la flexibilidad y la expansión futura. Optimizar estos elementos es clave para una distribución en planta exitosa.
El flujo de materiales, como ya se mencionó, es fundamental. Minimizar las distancias de transporte, reducir los movimientos innecesarios y evitar cuellos de botella son objetivos prioritarios. La ergonomía se centra en la comodidad y la seguridad de los empleados, considerando la disposición de los puestos de trabajo, la iluminación, la ventilación y el acceso a los equipos.
La seguridad debe ser una prioridad máxima, incluyendo el diseño de pasillos suficientemente amplios, la señalización adecuada, la ubicación estratégica de equipos de seguridad y el cumplimiento de las normas de seguridad laboral. La flexibilidad del diseño permite adaptarse a cambios en la producción, la introducción de nuevas tecnologías o modificaciones en los procesos.
Por último, la capacidad de expansión futura es esencial para que la distribución en planta pueda crecer y adaptarse a las necesidades cambiantes de la empresa. Un diseño bien planificado anticipa futuras expansiones y permite realizar cambios sin grandes disrupciones.
Estos factores interconectados requieren un análisis exhaustivo para un diseño óptimo de la distribución de la planta.
El objetivo principal es crear un espacio productivo, seguro y eficiente.
Un balance adecuado entre estos factores asegura un diseño flexible y eficiente.
Implementación y Evaluación de la Distribución en Planta
Una vez que se ha diseñado la nueva distribución en planta, la implementación requiere una planificación cuidadosa y una ejecución eficaz. Esto incluye la coordinación de las actividades de traslado, la instalación de nueva maquinaria y equipos, la capacitación de los empleados y la puesta en marcha de los nuevos procesos.
Es crucial contar con un plan detallado que especifique las tareas, los plazos, los recursos y las responsabilidades. La comunicación efectiva entre todos los involucrados es esencial para minimizar las interrupciones y garantizar una transición sin problemas. Durante la implementación, es importante monitorear el progreso y realizar ajustes según sea necesario.
Tras la implementación, es esencial evaluar la eficiencia de la nueva distribución en planta. Esto implica la recopilación de datos sobre el flujo de materiales, los tiempos de ciclo, la productividad de los empleados y los costos de operación. Comparando los resultados con los objetivos iniciales, se puede determinar el éxito de la nueva disposición.
La evaluación permite identificar áreas de mejora y optimizar la distribución en planta aún más. Los datos recolectados guían futuras decisiones.
El monitoreo continuo es necesario para detectar problemas potenciales.
La evaluación post-implementación es un paso crucial para la mejora continua.
Herramientas de Software para el Diseño de Planta
Existen numerosas herramientas de software disponibles para ayudar en el diseño y la optimización de la distribución en planta. Estos programas van desde aplicaciones sencillas hasta complejos sistemas de simulación. La elección del software dependerá del tamaño y la complejidad de la planta, así como del presupuesto y las necesidades específicas de la empresa.
Algunos ejemplos de software populares incluyen AutoDesk AutoCAD, que permite crear dibujos detallados de la planta; Plant Simulation, que simula el flujo de materiales y las operaciones; y Arena, que realiza simulaciones de procesos y optimiza los flujos de trabajo. Estos programas facilitan la visualización tridimensional de la planta, permiten realizar análisis de espacio y ayudan a identificar posibles cuellos de botella.
Además, existen software específicos para la optimización de almacenes, como el software de gestión de almacenes (WMS). Estos sistemas ayudan a gestionar el inventario, optimizar la ubicación de los productos y mejorar la eficiencia de las operaciones de almacenaje. La selección del software adecuado es crucial para obtener los mejores resultados en el diseño y la gestión de la distribución en planta.
La tecnología juega un rol vital en la modernización de las metodologías.
Los softwares ayudan en la planificación y visualización, facilitando la toma de decisiones.
Las nuevas tecnologías permiten simular diferentes escenarios antes de la implementación.
Consideraciones de Costos en el Diseño de Planta
El diseño de la distribución en planta debe considerar cuidadosamente los costos involucrados. Estos costos incluyen los costos de diseño, los costos de construcción, los costos de traslado de equipos, los costos de capacitación de los empleados y los costos de operación.
Es importante realizar un análisis de costo-beneficio para evaluar la rentabilidad de diferentes diseños. Un diseño eficiente puede reducir los costos de operación a largo plazo, compensando los costos iniciales de implementación. Por ejemplo, reducir las distancias de transporte puede disminuir los costos de energía y mano de obra. Optimizar el espacio puede reducir los costos de alquiler o construcción.
Además, es necesario considerar los costos asociados con la interrupción de la producción durante la implementación del nuevo diseño. Minimizar este tiempo de inactividad es crucial para reducir las pérdidas de productividad. Un diseño bien planificado y una implementación eficiente pueden minimizar los costos generales y maximizar el retorno de la inversión.
Un análisis minucioso ayuda a controlar los costos de implementación y operación.
La optimización del diseño puede generar importantes ahorros a largo plazo.
El balance entre costos iniciales y beneficios a largo plazo debe ser considerado cuidadosamente.
Conclusion
La distribución en planta es un aspecto fundamental para el éxito de cualquier operación industrial o de servicios. Un diseño bien planificado maximiza la eficiencia, la seguridad y la productividad, minimizando los costos y los tiempos de producción. Este artículo ha explorado en detalle los aspectos clave de la distribución en planta, desde los diferentes tipos de distribución hasta las herramientas y técnicas de diseño, incluyendo la importancia del análisis del flujo de materiales y la consideración de los costos.
Recuerda que la distribución en planta no es un proceso estático; es una disciplina que requiere un enfoque iterativo y una continua evaluación para asegurar su optimización y adaptación a las necesidades cambiantes de la empresa. Implementar una buena distribución de la planta requiere una planificación cuidadosa, un análisis profundo y la utilización de las herramientas adecuadas. El resultado final es una operación más eficiente, segura y rentable.
Preguntas Frecuentes
¿Qué es lo más importante en el diseño de la distribución en planta?
Minimizar el movimiento y maximizar el flujo de trabajo.
¿Qué tipo de software se utiliza en el diseño de una distribución en planta?
Software CAD, software de simulación y software de gestión de almacenes (WMS).
¿Cómo se evalúa la eficiencia de una distribución en planta?
Mediante la recopilación y análisis de datos sobre el flujo de materiales, los tiempos de ciclo y la productividad.
¿Cuáles son los costos a considerar en el diseño de la distribución en planta?
Costos de diseño, construcción, traslado de equipos, capacitación y operación.
¿Cómo se puede mejorar una distribución en planta existente?
Realizando un análisis del flujo de materiales, identificando cuellos de botella y optimizando el espacio.
Deja una respuesta
Te Puede Interesar: