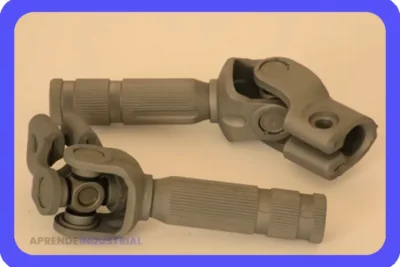
Capacidad de Producción: Tipos, mediciones y optimización
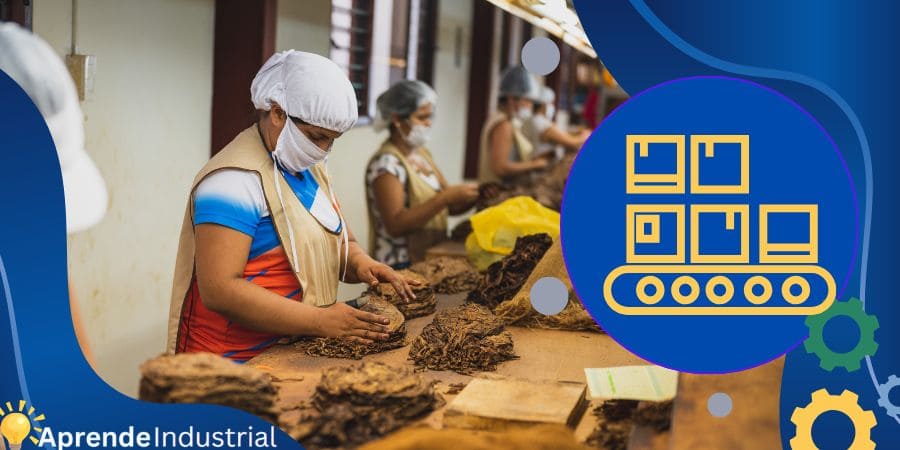
La capacidad de producción es un concepto fundamental en el ámbito industrial que se refiere a la cantidad máxima de productos que una empresa puede generar en un período determinado, bajo condiciones específicas. Este concepto no solo es crucial para la planificación y gestión de la producción, sino que también impacta directamente en la rentabilidad y competitividad de una organización. En un entorno donde la demanda del mercado puede fluctuar, entender y optimizar la capacidad de producción se convierte en una necesidad estratégica.
El objetivo de este artículo es ofrecer una visión integral sobre la capacidad de producción, explorando sus diferentes tipos, métodos de medición y estrategias de optimización. A lo largo del texto, se presentarán ejemplos prácticos y se discutirán indicadores clave como la utilización y la eficiencia. Además, se analizarán escenarios de producción para determinar si la capacidad instalada es suficiente para satisfacer la demanda del mercado. Finalmente, se concluirá con recomendaciones sobre cómo mejorar la capacidad de producción y cuándo es necesario considerar la expansión de las líneas de producción.
Tipos de Capacidad de Producción
La capacidad de producción se puede clasificar en tres tipos principales: capacidad de diseño, capacidad efectiva y capacidad real. Cada uno de estos tipos tiene características y aplicaciones específicas que son importantes para la gestión de la producción.
Capacidad de Diseño
La capacidad de diseño se refiere a la cantidad máxima de producción que una instalación puede alcanzar bajo condiciones óptimas. Este tipo de capacidad se basa en el diseño de la planta, el número de máquinas y el tiempo de operación. Es un concepto teórico que no toma en cuenta factores como el mantenimiento, las paradas no programadas o la variabilidad en la demanda.
La capacidad de diseño es fundamental para la planificación a largo plazo. Permite a las empresas establecer metas de producción y evaluar si sus instalaciones actuales son adecuadas para cumplir con las proyecciones de demanda. Sin embargo, es importante recordar que la capacidad de diseño no siempre se traduce en la producción real, ya que las condiciones del mundo real pueden afectar significativamente el rendimiento.
Capacidad Efectiva
La capacidad efectiva es un paso más realista que la capacidad de diseño. Se refiere a la cantidad de producción que una instalación puede lograr en condiciones normales de operación, teniendo en cuenta factores como el mantenimiento programado, las paradas por fallos y la variabilidad en la demanda. Este tipo de capacidad es más útil para la planificación a corto plazo y la programación de la producción.
La capacidad efectiva se calcula restando el tiempo perdido por mantenimiento y otros factores de la capacidad de diseño. Por ejemplo, si una máquina tiene una capacidad de diseño de 100 unidades por hora, pero se pierde un 10% del tiempo por mantenimiento, la capacidad efectiva sería de 90 unidades por hora. Este cálculo permite a las empresas tener una visión más clara de lo que realmente pueden producir.
Capacidad Real
La capacidad real es la cantidad de producción que una instalación logra en la práctica, considerando todos los factores que pueden afectar la producción, como la eficiencia de los trabajadores, la calidad de los insumos y las interrupciones inesperadas. Este tipo de capacidad es el más difícil de medir, ya que puede variar significativamente de un día a otro.
La capacidad real es crucial para la toma de decisiones operativas. Permite a las empresas identificar cuellos de botella en el proceso de producción y áreas donde se puede mejorar la eficiencia. Además, al comparar la capacidad real con la capacidad efectiva y de diseño, las empresas pueden obtener información valiosa sobre su rendimiento y áreas de mejora.
Indicadores de Capacidad de Producción
Para medir la capacidad de producción, se utilizan varios indicadores clave, entre los que destacan la utilización y la eficiencia. Estos indicadores permiten a las empresas evaluar su rendimiento y tomar decisiones informadas sobre la optimización de sus procesos.
Utilización
La utilización es un indicador que mide el porcentaje de la capacidad efectiva que se está utilizando en un período determinado. Se calcula dividiendo la producción real entre la capacidad efectiva y multiplicando el resultado por 100. Este indicador es fundamental para entender si una empresa está aprovechando al máximo sus recursos.
Por ejemplo, si una planta tiene una capacidad efectiva de 200 unidades por día y produce 150 unidades, la utilización sería del 75%. Una utilización baja puede indicar que hay oportunidades para mejorar la producción, ya sea aumentando la eficiencia de los procesos o ajustando la programación de la producción.
Eficiencia
La eficiencia es otro indicador clave que mide la relación entre la producción real y la producción que se podría haber logrado en condiciones ideales. Se calcula dividiendo la producción real entre la capacidad de diseño y multiplicando el resultado por 100. Este indicador permite a las empresas evaluar cuán bien están utilizando sus recursos en comparación con su potencial máximo.
Por ejemplo, si una planta tiene una capacidad de diseño de 300 unidades por día y produce 240 unidades, la eficiencia sería del 80%. Una eficiencia baja puede señalar problemas en el proceso de producción, como tiempos de inactividad excesivos o problemas de calidad que afectan la producción.
Comparación de Indicadores de Capacidad de Producción
La capacidad de producción es un factor crítico para cualquier empresa. Comprender y gestionar los diferentes tipos de capacidad es esencial para optimizar la producción, cumplir con la demanda y maximizar la eficiencia. A continuación, se presenta una tabla que resume la comparación entre los diferentes tipos de capacidad y sus indicadores asociados:
Tipo de Capacidad | Descripción | Indicador Clave |
---|---|---|
Capacidad de Diseño (CD) | Máxima producción teórica bajo condiciones óptimas, sin considerar paradas ni problemas. | Capacidad de Diseño (CD) |
Capacidad Efectiva (CE) | Producción máxima esperada en condiciones normales, considerando paradas planificadas (mantenimiento, etc.). | Utilización (U) = (Capacidad Real / Capacidad de Diseño) * 100% |
Capacidad Real (CR) | Producción real obtenida, considerando todos los factores (paradas no planificadas, eficiencia, calidad, etc.). | Eficiencia (E) = (Capacidad Real / Capacidad Efectiva) * 100% |
Cálculo de la Capacidad de Producción
1. Cálculo de la Capacidad de Diseño (CD)
Capacidad de Diseño = Número de Máquinas × Tasa de Producción por Máquina × Horas de Operación
Ejemplo 1:
Una fábrica tiene 10 máquinas que producen 50 unidades por hora cada una. Operan 24 horas al día, 7 días a la semana.
Ejemplo 2:
Una panadería tiene 3 hornos que pueden hornear 100 barras de pan por hora cada uno. Funcionan 12 horas al día, de lunes a sábado.
Una planta tiene 5 máquinas que producen 20 unidades por hora y opera 8 horas al día.
Capacidad de Diseño = 5 × 20 × 8 = 800 unidades por día
Ejemplo 4:
Una fábrica cuenta con 10 máquinas que producen 15 unidades por hora y opera 10 horas al día.
Capacidad de Diseño = 10 × 15 × 10 = 1500 unidades por día
Ejemplo 5: Producción de Botellas
Una fábrica tiene 10 máquinas que producen 50 botellas por hora cada una y opera 16 horas al día.
Capacidad de Diseño = 10 × 50 × 16 = 8,000 botellas por día
Ejemplo 6: Producción de Piezas Metálicas
Un taller cuenta con 4 tornos que producen 30 piezas por hora cada uno y trabajan 10 horas diarias.
Capacidad de Diseño = 4 × 30 × 10 = 1,200 piezas por día
2. Cálculo de la Capacidad Efectiva (CE)
Para calcular la capacidad efectiva, se deben considerar las paradas programadas y no programadas. La fórmula es:
Capacidad Efectiva = Capacidad de Diseño - (Capacidad de Diseño × Porcentaje de Tiempo Perdido)
Ejemplo 1:
La capacidad de diseño es de 800 unidades por día y se pierde un 10% del tiempo por mantenimiento.
Capacidad Efectiva = 800 - (800 × 0.10) = 800 - 80 = 720 unidades por día
Ejemplo 2:
La capacidad de diseño es de 1500 unidades por día y se pierde un 15% del tiempo por fallos de maquinaria.
Capacidad Efectiva = 1500 - (1500 × 0.15) = 1500 - 225 = 1275 unidades por día
Ejemplo 3:
La fábrica del ejemplo anterior tiene un mantenimiento programado de 2 horas por día.
CE = 12,000 unidades/día - (10 máquinas * 50 unidades/hora/máquina * 2 horas/día) = 11,000 unidades/día
Ejemplo 4:
La panadería del ejemplo anterior cierra los domingos y tiene un mantenimiento de 4 horas por semana.
CE = 21,600 barras/semana - (3 hornos * 100 barras/hora/horno * 4 horas/semana) = 20,400 barras/semana
Ejemplo 5: Producción de Botellas con Paradas por Mantenimiento
Si la capacidad de diseño es de 8,000 botellas por día, pero hay un 15% de tiempo perdido por mantenimiento y ajustes:
Capacidad Efectiva = 8,000 - (8,000 × 0.15)
Capacidad Efectiva = 8,000 - 1,200 = 6,800 botellas por día
Ejemplo 6: Producción de Piezas con Fallos de Maquinaria
Si la capacidad de diseño es de 1,200 piezas por día, pero hay un 10% de tiempo perdido debido a fallos de maquinaria:
Capacidad Efectiva = 1,200 - (1,200 × 0.10)
Capacidad Efectiva = 1,200 - 120 = 1,080 piezas por día
3. Cálculo de la Capacidad Real (CR)
El cálculo de la capacidad real es más complejo, ya que implica considerar la eficiencia de los trabajadores y la calidad de los insumos. La fórmula básica es:
Capacidad Real = Capacidad Efectiva × Eficiencia
Ejemplo 1:
La capacidad efectiva es de 720 unidades por día y la eficiencia es del 85%.
Capacidad Real = 720 × 0.85 = 612 unidades por día
Ejemplo 2:
La capacidad efectiva es de 1275 unidades por día y la eficiencia es del 90%.
Capacidad Real = 1275 × 0.90 = 1147.5 unidades por día
Ejemplo 3:
Supongamos que una fábrica tiene una capacidad efectiva de 1000 unidades por día, pero debido a problemas de calidad en los materiales, la eficiencia baja al 70%.
Capacidad Real = 1000 × 0.70 = 700 unidades por día
Ejemplo 4:
La fábrica del ejemplo anterior tiene una eficiencia del 90% debido a paradas no planificadas, problemas de calidad, etc.
Ejemplo 5:
La panadería del ejemplo anterior tiene una eficiencia del 85% debido a problemas con los ingredientes, retrasos, etc.
Ejemplo 6: Producción de Botellas con Eficiencia del 90%
Si la capacidad efectiva es de 6,800 botellas por día, pero la eficiencia del sistema es del 90%:
Capacidad Real = 6,800 × 0.90
Capacidad Real = 6,120 botellas por día
Ejemplo 7: Producción de Piezas con Eficiencia del 85%
Si la capacidad efectiva es de 1,080 piezas por día, pero la eficiencia del proceso es del 85%:
Capacidad Real = 1,080 × 0.85
Capacidad Real = 918 piezas por día
Escenarios de Producción
Analizar diferentes escenarios de producción es crucial para determinar si la capacidad instalada es suficiente para cumplir con la demanda. A continuación, se presentan algunos escenarios comunes y cómo abordarlos.
Escenario de Alta Demanda
En un escenario de alta demanda, las empresas pueden enfrentar desafíos significativos si su capacidad instalada no es suficiente. En este caso, es fundamental evaluar la capacidad de producción actual y compararla con las proyecciones de demanda. Si la capacidad real es inferior a la demanda, se deben considerar opciones como la expansión de la planta, la adquisición de nuevas máquinas o la implementación de turnos adicionales.
Además, es importante analizar la cadena de suministro para asegurarse de que los insumos necesarios estén disponibles para satisfacer la demanda. La colaboración con proveedores y la optimización de los procesos logísticos pueden ayudar a mitigar los riesgos asociados con la alta demanda.
Escenario de Baja Demanda
En un escenario de baja demanda, las empresas pueden encontrarse con una capacidad de producción subutilizada. En este caso, es esencial evaluar la utilización de los recursos y considerar ajustes en la programación de la producción. La reducción de turnos o la reprogramación de la producción pueden ser estrategias efectivas para optimizar la capacidad.
Además, las empresas deben estar atentas a las tendencias del mercado y a las señales de un posible aumento en la demanda. Mantener la flexibilidad en la producción y la capacidad de adaptarse rápidamente a los cambios en el mercado es clave para el éxito a largo plazo.
Escenario de Demanda Estable
En un escenario de demanda estable, las empresas pueden operar de manera más predecible. En este caso, es importante mantener un equilibrio entre la capacidad de producción y la demanda. La planificación a largo plazo y la inversión en mejoras de eficiencia pueden ayudar a garantizar que la capacidad instalada sea suficiente para cumplir con la demanda sin incurrir en costos innecesarios.
Además, las empresas deben seguir monitoreando su rendimiento y ajustando sus procesos según sea necesario. La implementación de tecnologías avanzadas y la capacitación continua de los empleados pueden contribuir a mejorar la eficiencia y la capacidad de producción.
Estrategias de Optimización de la Capacidad de Producción
Optimizar la capacidad de producción es un objetivo clave para muchas empresas. A continuación, se presentan algunas estrategias efectivas para lograrlo.
Mejora de Procesos
La mejora de procesos es una estrategia fundamental para optimizar la capacidad de producción. Esto implica analizar cada etapa del proceso de producción y buscar oportunidades para eliminar desperdicios, reducir tiempos de inactividad y mejorar la eficiencia. La implementación de metodologías como Lean Manufacturing o Six Sigma puede ser muy efectiva en este sentido.
Por ejemplo, al identificar cuellos de botella en el proceso de producción, las empresas pueden implementar cambios que aumenten la velocidad y la eficiencia. Esto puede incluir la reconfiguración de la línea de producción, la capacitación de los empleados o la inversión en nuevas tecnologías.
Inversión en Tecnología
La inversión en tecnología es otra estrategia clave para optimizar la capacidad de producción. La automatización de procesos, la implementación de sistemas de gestión de la producción y el uso de tecnologías avanzadas como la inteligencia artificial pueden ayudar a mejorar la eficiencia y la capacidad de producción.
Por ejemplo, la automatización de tareas repetitivas puede liberar a los empleados para que se concentren en actividades de mayor valor. Además, el uso de sistemas de gestión de la producción puede proporcionar información en tiempo real sobre el rendimiento, lo que permite a las empresas tomar decisiones informadas y rápidas.
Capacitación y Desarrollo del Personal
La capacitación y desarrollo del personal es esencial para optimizar la capacidad de producción. Invertir en la formación de los empleados no solo mejora sus habilidades, sino que también aumenta la moral y la satisfacción laboral. Un personal bien capacitado es más eficiente y productivo, lo que se traduce en una mayor capacidad de producción.
Las empresas deben ofrecer programas de capacitación continua y oportunidades de desarrollo profesional. Esto no solo beneficia a los empleados, sino que también contribuye al éxito a largo plazo de la organización.
Conclusión
La capacidad de producción es un aspecto crítico de la gestión industrial que impacta directamente en la rentabilidad y competitividad de una empresa. Comprender los diferentes tipos de capacidad, así como los indicadores clave como la utilización y la eficiencia, es fundamental para la planificación y optimización de la producción. A través de cálculos precisos y el análisis de escenarios de producción, las empresas pueden tomar decisiones informadas sobre cómo mejorar su capacidad de producción.
Además, la implementación de estrategias de optimización, como la mejora de procesos, la inversión en tecnología y la capacitación del personal, puede ayudar a las empresas a alcanzar sus objetivos de producción y adaptarse a las fluctuaciones del mercado. En un entorno empresarial en constante cambio, la capacidad de producción se convierte en un factor determinante para el éxito a largo plazo.
Preguntas Frecuentes
¿Qué es la capacidad de producción?
La capacidad de producción es la cantidad máxima de productos que una empresa puede generar en un período determinado, considerando factores como el número de máquinas y el tiempo de operación.
¿Cuáles son los tipos de capacidad de producción?
Los tipos de capacidad de producción son: capacidad de diseño, capacidad efectiva y capacidad real.
¿Cómo se mide la eficiencia en la producción?
La eficiencia se mide comparando la producción real con la capacidad de diseño, expresada como un porcentaje.
¿Por qué es importante optimizar la capacidad de producción?
Optimizar la capacidad de producción es crucial para mejorar la rentabilidad, reducir costos y adaptarse a las fluctuaciones del mercado.
Referencias
Deja una respuesta
Te Puede Interesar: