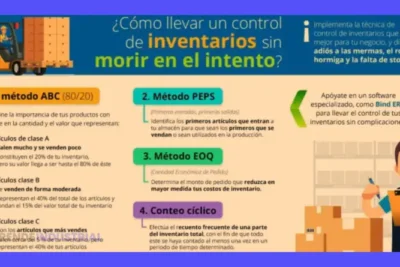
Cómo calcular la capacidad de almacenes
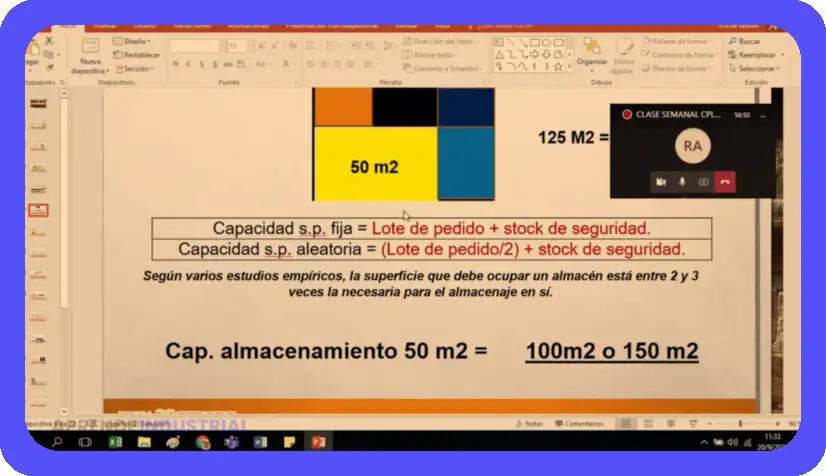
La gestión eficiente de la capacidad de almacenes es crucial para el éxito de cualquier negocio que maneje inventario físico. Un almacén bien organizado y optimizado no solo permite almacenar productos de forma segura, sino que también facilita la rápida localización y despacho de los mismos, minimizando costos y maximizando la productividad. La capacidad de almacenes se refiere al volumen total de espacio disponible para almacenar mercancías, y su correcta evaluación y gestión son fundamentales para evitar problemas como la sobreocupación, la desorganización y las pérdidas de inventario.
Este artículo explorará en detalle los aspectos clave de la capacidad de almacenes, desde cómo calcularla con precisión hasta las estrategias para aumentarla y optimizarla. Abordaremos temas como los diferentes tipos de almacenaje, la importancia de un diseño eficiente, el uso de tecnología para la gestión de inventario y las mejores prácticas para maximizar el espacio disponible. Nuestro objetivo es brindarte una guía completa que te permita comprender y gestionar la capacidad de tu almacén de manera efectiva, independientemente del tamaño o tipo de tu negocio.
- Calculando la Capacidad de Almacenes
- Optimizando el Diseño para Maximizar la Capacidad de Almacenes
- Tipos de Almacenaje y su Impacto en la Capacidad
- La Tecnología en la Gestión de la Capacidad de Almacenes
- Aumentando la Capacidad de Almacenes: Estrategias y Consideraciones
- Indicadores Clave para Monitorear la Capacidad de Almacenes
- Mejores Prácticas para la Gestión de la Capacidad de Almacenes
- El Futuro de la Capacidad de Almacenes: Automatización e Inteligencia Artificial
- Conclusión
- Preguntas Frecuentes
Calculando la Capacidad de Almacenes
Ubicación del Almacén | Capacidad de Almacenamiento (m³) |
---|---|
Almacén Central - Madrid | 15000 |
Almacén Regional - Barcelona | 8500 |
Almacén Distribución - Sevilla | 5000 |
Almacén Logística - Valencia | 12000 |
Almacén Auxiliar - Zaragoza | 3000 |
Para determinar la capacidad de almacenes, es necesario realizar un cálculo preciso del espacio disponible. El primer paso consiste en medir el área total del almacén en metros cuadrados. Luego, debemos restar el área ocupada por zonas no destinadas al almacenaje, como oficinas, baños, áreas de carga y descarga, y pasillos principales. A este resultado, lo multiplicamos por la altura máxima utilizable para el almacenaje, considerando la altura de los sistemas de ventilación, iluminación y cualquier otra obstrucción. Este cálculo nos dará la capacidad del almacén en metros cúbicos.
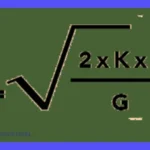
Por ejemplo, si un almacén tiene un área total de 1000 m², y 200 m² están destinados a oficinas y otras áreas no utilizables para almacenaje, el área disponible para almacenamiento es de 800 m². Si la altura máxima utilizable es de 5 metros, la capacidad del almacén es de 800 m² * 5 m = 4000 m³.
Es importante considerar que este cálculo proporciona la capacidad total teórica. La capacidad real disponible puede ser menor debido a factores como el tipo de estanterías utilizadas, la naturaleza de los productos almacenados (tamaño, forma, fragilidad) y las necesidades de acceso para la manipulación de los mismos. Un diseño eficiente del almacén maximiza el uso del espacio disponible.
Un ejercicio práctico para calcular la capacidad de almacenes sería: Un almacén tiene dimensiones de 50m x 20m y una altura utilizable de 6m. Se destinan 100m² a oficinas. ¿Cuál es la capacidad de almacenamiento? Solución: Área total: 50m * 20m = 1000m². Área de almacenaje: 1000m² - 100m² = 900m². Capacidad: 900m² * 6m = 5400m³.
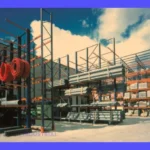
Optimizando el Diseño para Maximizar la Capacidad de Almacenes
Estrategia de Optimización | Impacto en la Capacidad (Incremento porcentual) |
---|---|
Implementación de un Sistema de Gestión de Almacenes (WMS) | 25% |
Optimización del diseño de estanterías (altura, tipo, etc.) | 15% |
Utilización de tecnología de radiofrecuencia (RFID) para el inventario | 10% |
Implementación de un sistema de picking eficiente (ej. Pick-to-light) | 8% |
Mejor gestión del espacio aéreo (utilización de racks de alta densidad) | 12% |
Formación del personal en técnicas de almacenamiento optimizado | 5% |
El diseño del almacén juega un papel crucial en la optimización de la capacidad de almacenes. Un diseño eficiente permite aprovechar al máximo el espacio disponible y facilita las operaciones de almacenamiento y recuperación de mercancías. Existen diferentes tipos de diseño, como el diseño en U, en L, en I o en T, cada uno con sus ventajas y desventajas. La elección del diseño adecuado depende de factores como la forma del edificio, el flujo de mercancías y las necesidades específicas del negocio.
Además del diseño general, la disposición de las estanterías y la asignación de ubicaciones para los diferentes productos también influyen en la capacidad de almacenes. Utilizar estanterías de alta densidad, sistemas de almacenamiento vertical y otras soluciones de almacenamiento optimizado puede aumentar significativamente la capacidad de almacenamiento.
Considerar el flujo de mercancías es fundamental para un diseño eficiente. Se debe planificar la ubicación de las zonas de recepción, almacenamiento y despacho de manera que se minimicen los desplazamientos y se optimice el tiempo de las operaciones. Un buen diseño también debe considerar la seguridad del personal y la prevención de accidentes. Por ejemplo, pasillos suficientemente amplios y una buena iluminación son esenciales para un entorno de trabajo seguro.
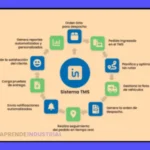
Tipos de Almacenaje y su Impacto en la Capacidad
Tipo de Almacenaje | Impacto en la Capacidad |
---|---|
Almacenamiento en disco duro (HDD) | Alta capacidad a bajo costo por GB, pero velocidades de lectura/escritura más lentas que SSD. Capacidad típica: de 1 TB a 18 TB por unidad. |
Almacenamiento en estado sólido (SSD) | Menor capacidad por costo que HDD, pero velocidades de lectura/escritura significativamente más rápidas. Capacidad típica: de 256 GB a 8 TB por unidad. |
Almacenamiento en la nube (Cloud Storage) | Capacidad prácticamente ilimitada, dependiendo del plan de suscripción. Costo variable según el uso y el proveedor. Velocidades de acceso dependientes de la conexión a internet y la ubicación del servidor. |
Almacenamiento en cinta magnética | Muy alta capacidad a bajo costo por GB, pero velocidades de acceso extremadamente lentas. Principalmente usado para copias de seguridad a largo plazo. Capacidad típica: de 1 TB a 30 TB por cinta. |
Almacenamiento de objetos (Object Storage) | Escalable y diseñado para almacenar grandes cantidades de datos no estructurados. Ideal para archivos multimedia y Big Data. Capacidad prácticamente ilimitada. |
La elección del sistema de almacenaje adecuado es fundamental para maximizar la capacidad de almacenes. Existen diversos tipos de sistemas, cada uno con sus propias características y ventajas. Las estanterías convencionales son una opción versátil y económica, mientras que las estanterías de alta densidad, como las estanterías compactas o las estanterías móviles, permiten almacenar una mayor cantidad de productos en el mismo espacio.
Para productos de gran tamaño o peso, se pueden utilizar estanterías cantilever o sistemas de almacenamiento en bloque. La elección del sistema de almacenaje debe basarse en las características de los productos almacenados, la frecuencia de acceso a los mismos y las necesidades específicas del negocio. Por ejemplo, para productos con alta rotación, es recomendable utilizar sistemas que faciliten el acceso rápido, mientras que para productos con baja rotación, se pueden utilizar sistemas de almacenamiento más compactos.
| Tipo de Almacenaje | Descripción | Impacto en la Capacidad |
|---|---|---|
| Estanterías Convencionales | Versátiles y económicas | Moderado |
| Estanterías de Alta Densidad | Maximiza el espacio vertical | Alto |
| Estanterías Cantilever | Para productos largos y voluminosos | Depende del producto |
| Almacenamiento en Bloque | Para productos paletizados | Alto |
La Tecnología en la Gestión de la Capacidad de Almacenes
La tecnología juega un papel cada vez más importante en la gestión eficiente de la capacidad de almacenes. Los sistemas de gestión de almacenes (WMS) permiten controlar y optimizar todas las operaciones del almacén, desde la recepción de mercancías hasta el despacho de pedidos. Estos sistemas proporcionan información en tiempo real sobre la ubicación de los productos, el nivel de inventario y la disponibilidad de espacio.
El uso de la tecnología también facilita la automatización de procesos, como la gestión de ubicaciones, la preparación de pedidos y el control de inventario. La automatización reduce los errores humanos, mejora la eficiencia y libera al personal para tareas de mayor valor añadido. Además, la tecnología permite analizar datos históricos para identificar tendencias y patrones de demanda, lo que ayuda a prever las necesidades futuras de capacidad de almacenes.
Aumentando la Capacidad de Almacenes: Estrategias y Consideraciones
Cuando la capacidad de almacenes actual se vuelve insuficiente, es necesario considerar estrategias para aumentarla. Una opción es ampliar físicamente el almacén, construyendo nuevas áreas de almacenamiento. Sin embargo, esta opción puede ser costosa y requerir tiempo. Otras estrategias incluyen la optimización del diseño del almacén, la implementación de sistemas de almacenaje más eficientes y la externalización de parte del almacenaje a un proveedor logístico externo (3PL).
La decisión de aumentar la capacidad de almacenes debe basarse en un análisis cuidadoso de las necesidades del negocio, los costos asociados y las proyecciones de crecimiento futuro. Es importante considerar factores como la demanda prevista, la estacionalidad del negocio y la posibilidad de fluctuaciones en el volumen de inventario.
Indicadores Clave para Monitorear la Capacidad de Almacenes
Monitorear la capacidad de almacenes es esencial para asegurar la eficiencia de las operaciones y anticipar posibles problemas. Existen varios indicadores clave que permiten evaluar el rendimiento del almacén y identificar áreas de mejora. El porcentaje de utilización del espacio es un indicador fundamental que mide la proporción del espacio total del almacén que se está utilizando efectivamente para almacenar mercancías.
Otro indicador importante es el tiempo de ciclo de pedido, que mide el tiempo que transcurre desde que se recibe un pedido hasta que se despacha. Un tiempo de ciclo de pedido corto indica una alta eficiencia en las operaciones del almacén. También es importante monitorear el número de errores en la preparación de pedidos y el costo de almacenamiento por unidad. Estos indicadores proporcionan información valiosa para la toma de decisiones y la optimización de la capacidad de almacenes.
Mejores Prácticas para la Gestión de la Capacidad de Almacenes
Implementar mejores prácticas en la gestión de la capacidad de almacenes es fundamental para maximizar el espacio disponible, mejorar la eficiencia y reducir costos. Una práctica clave es la organización y la limpieza del almacén. Mantener un almacén ordenado y limpio facilita la localización de los productos, reduce el riesgo de accidentes y optimiza el uso del espacio.
Otra práctica importante es la gestión eficiente del inventario. Implementar un sistema de control de inventario que permita conocer en tiempo real la cantidad y la ubicación de los productos es esencial para evitar la sobreocupación del almacén y minimizar las pérdidas por obsolescencia o deterioro. Además, es recomendable realizar auditorías periódicas del inventario para verificar la exactitud de los registros y detectar posibles discrepancias.
El Futuro de la Capacidad de Almacenes: Automatización e Inteligencia Artificial
La automatización y la inteligencia artificial (IA) están transformando la gestión de la capacidad de almacenes. Los robots autónomos, los sistemas de almacenamiento automatizados y los algoritmos de IA permiten optimizar la utilización del espacio, aumentar la velocidad de las operaciones y reducir los costos. La IA también permite predecir la demanda con mayor precisión, lo que ayuda a planificar la capacidad de almacenes de manera más eficiente.
El uso de drones para la gestión de inventario es otra innovación que está ganando terreno. Los drones pueden realizar inventarios de forma rápida y precisa, reduciendo el tiempo y el esfuerzo requeridos para esta tarea. A medida que la tecnología continúa avanzando, podemos esperar ver nuevas y emocionantes innovaciones en la gestión de la capacidad de almacenes.
Conclusión
La gestión eficiente de la capacidad de almacenes es un factor crítico para el éxito de cualquier negocio que maneje inventario físico. Desde el cálculo preciso del espacio disponible hasta la implementación de estrategias de optimización y el uso de tecnología, cada aspecto juega un papel importante en la maximización del rendimiento del almacén. Un almacén bien organizado y optimizado no solo permite almacenar productos de forma segura, sino que también facilita las operaciones, reduce costos y mejora la satisfacción del cliente. Al comprender y aplicar los conceptos y estrategias discutidos en este artículo, las empresas pueden mejorar significativamente la gestión de su capacidad de almacenes y, en consecuencia, su rentabilidad y competitividad. Recuerda que una planificación estratégica y una gestión proactiva son esenciales para asegurar que la capacidad de tu almacén se adapte a las necesidades cambiantes de tu negocio.
Preguntas Frecuentes
¿Cómo calcular la capacidad de un almacén con diferentes alturas?
Divide el almacén en secciones con alturas uniformes, calcula la capacidad de cada sección y suma los resultados.
¿Qué es un WMS y cómo impacta en la capacidad?
Un WMS (Sistema de Gestión de Almacenes) optimiza las operaciones y la utilización del espacio, maximizando la capacidad.
¿Cuál es la mejor estrategia para aumentar la capacidad de un almacén pequeño?
Implementar estanterías de alta densidad y optimizar el diseño del almacén suele ser la opción más efectiva.
¿Cómo la automatización mejora la capacidad de almacenes?
Automatizando tareas como la gestión de ubicaciones y la preparación de pedidos, se libera espacio y se mejora la eficiencia.
¿Qué indicadores debo monitorear para gestionar la capacidad de mi almacén?
Porcentaje de utilización del espacio, tiempo de ciclo de pedido, errores en la preparación de pedidos y costo de almacenamiento por unidad.
Deja una respuesta
Te Puede Interesar: