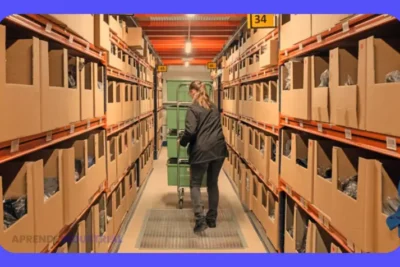
👉 Análisis de riesgos en entornos industriales: Métodos, ejemplos y cómo aplicarlos eficazmente
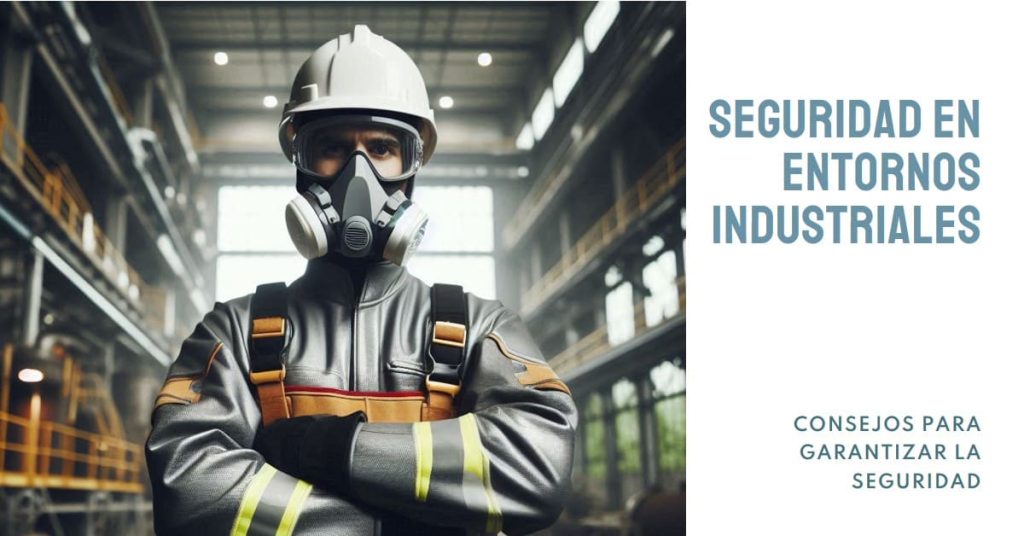
¿Sabías que el 80% de los accidentes laborales en la industria se podrían evitar con un análisis de riesgos adecuado? En este artículo te explico cómo aplicar esta poderosa herramienta paso a paso.
El análisis de riesgos es una práctica fundamental para identificar, evaluar y controlar los peligros y amenazas que pueden afectar la seguridad y salud de los trabajadores, así como la integridad de las instalaciones y los procesos industriales. Acompáñame en este recorrido para conocer más sobre esta importante disciplina.
- ¿Qué es el análisis de riesgos en entornos industriales?
- La importancia de identificar y evaluar los riesgos en el entorno laboral para garantizar la seguridad y salud de los trabajadores
- Identificar y evaluar los riesgos en el entorno laboral es el primer paso para prevenir accidentes y lesiones.
- Métodos y herramientas utilizadas en el análisis de riesgos en entornos industriales
- Etapas clave del análisis de riesgos: identificación, evaluación y control
- Ejemplos de la aplicación del análisis de riesgos en entornos industriales
- Conclusión
- Preguntas frecuentes
¿Qué es el análisis de riesgos en entornos industriales?
Antes de entrar en detalle acerca del análisis de riesgos en entornos industriales, es importante entender qué se entiende por "riesgo". En términos generales, el riesgo se refiere a la posibilidad de que ocurra un evento no deseado, acompañado de las consecuencias negativas que este evento pueda acarrear.
En el ámbito industrial, estos eventos no deseados pueden ser accidentes laborales, incidentes con maquinaria o procesos de producción defectuosos, entre otros.
El análisis de riesgos en entornos industriales es una herramienta que busca identificar, evaluar y controlar los posibles peligros y amenazas presentes en un lugar de trabajo.
Esto se hace con el objetivo de prevenir accidentes, proteger la salud de los trabajadores y preservar la integridad de las instalaciones y los procesos industriales.
La importancia de identificar y evaluar los riesgos en el entorno laboral para garantizar la seguridad y salud de los trabajadores
El análisis de riesgos es una parte fundamental de la gestión de la seguridad en el entorno industrial. Garantizar la seguridad y salud de los trabajadores es una responsabilidad legal y ética de las empresas, y el análisis de riesgos es una herramienta clave para lograr este objetivo.
Identificar y evaluar los riesgos en el entorno laboral es el primer paso para prevenir accidentes y lesiones.
Sin un análisis de riesgos adecuado, las empresas están expuestas a situaciones peligrosas que pueden resultar en incidentes graves e incluso fatales. Al realizar un análisis de riesgos, se pueden identificar las actividades y los procesos que presentan mayores riesgos, lo que permite implementar medidas preventivas y de control adecuadas.
Métodos y herramientas utilizadas en el análisis de riesgos en entornos industriales
Existen diversos métodos y herramientas que se pueden utilizar en el análisis de riesgos en entornos industriales. A continuación, describiré algunos de los más comunes:
1. Matriz de riesgos: Una matriz de riesgos es una herramienta que permite evaluar y clasificar los riesgos según su probabilidad de ocurrencia y su severidad.
Esta matriz proporciona una visualización clara de los riesgos y ayuda a establecer prioridades en cuanto a las medidas de control que se deben implementar.
2. Análisis de causa raíz: El análisis de causa raíz es un método que busca identificar las causas subyacentes de un accidente o incidente.
Se basa en la premisa de que los incidentes no ocurren de forma aislada, sino que son el resultado de una cadena de eventos interconectados. Al identificar las causas raíz, se pueden implementar medidas correctivas efectivas y prevenir eventos similares en el futuro.
3. HAZOP (Hazard and Operability Study): El HAZOP es una técnica de análisis utilizada principalmente en la industria química y de procesos. Consiste en examinar de forma sistemática un proceso o una planta en busca de posibles desviaciones o desviaciones inseguras.
El objetivo es identificar los peligros potenciales y proponer medidas para eliminar o controlar estos riesgos.
Estas son solo algunas de las herramientas más utilizadas en el análisis de riesgos en entornos industriales. La selección de la herramienta adecuada depende del contexto y de los objetivos específicos de cada análisis.
Etapas clave del análisis de riesgos: identificación, evaluación y control
El análisis de riesgos en entornos industriales consta de varias etapas clave que se deben llevar a cabo de manera sistemática. A continuación, describiré cada una de estas etapas:
1. Identificación de riesgos: En esta etapa, se realiza una revisión exhaustiva del entorno laboral para identificar los posibles peligros y amenazas presentes.
Esto se puede hacer mediante inspecciones de seguridad, análisis de documentos, entrevistas con el personal y revisión de registros de incidentes previos.
2. Evaluación de riesgos: Una vez identificados los riesgos, es necesario evaluar su probabilidad de ocurrencia y su impacto potencial.
Esto se puede hacer de forma cualitativa, asignando valores subjetivos a los riesgos según su gravedad y probabilidad, o de forma cuantitativa, utilizando datos y medidas objetivas. La evaluación de riesgos permite establecer prioridades y tomar decisiones fundamentadas en cuanto a las medidas de control que se deben implementar.
3. Control de riesgos: Una vez evaluados los riesgos, es necesario implementar medidas de control adecuadas para reducir o eliminar los posibles peligros. Estas medidas pueden incluir el uso de equipos de protección personal, la modificación de procesos o instalaciones, o la implementación de prácticas de trabajo seguras.
Es importante recordar que el control de riesgos no se trata solo de implementar medidas de protección, sino también de vigilar su efectividad y realizar ajustes si es necesario.
Ejemplos de la aplicación del análisis de riesgos en entornos industriales
El análisis de riesgos se aplica en una amplia variedad de entornos industriales. A continuación, compartiré dos ejemplos para ilustrar cómo se puede utilizar esta herramienta para prevenir accidentes y garantizar la seguridad de los trabajadores:
1. Prevención de accidentes en la construcción de torres de alta tensión: En la construcción de torres de alta tensión, existen numerosos riesgos asociados, como caídas desde alturas, electrocuciones y el uso de maquinaria pesada.
Mediante un análisis de riesgos exhaustivo, se pueden identificar los puntos críticos del proceso de construcción y se pueden implementar medidas de seguridad adecuadas, como el uso de equipos de protección personal, la capacitación del personal en prácticas seguras de trabajo en alturas y la implementación de barreras de seguridad.
2. Manipulación segura de químicos corrosivos en empresas químicas: Las empresas químicas manejan una amplia variedad de sustancias tóxicas, inflamables y corrosivas, lo que conlleva importantes riesgos para los trabajadores y las instalaciones.
Un análisis de riesgos en este entorno ayudaría a identificar las sustancias más peligrosas y las áreas de manejo que requieren medidas de control adicionales, como el uso de equipos de protección personal adecuados, rutinas de trabajo seguras y la implementación de controles de ingeniería para minimizar la exposición a productos químicos peligrosos.
Estos ejemplos demuestran cómo el análisis de riesgos puede ser aplicado en diferentes entornos industriales para prevenir accidentes y promover la seguridad de los trabajadores.
Conclusión
El análisis de riesgos en entornos industriales es una práctica esencial para garantizar la seguridad y salud de los trabajadores, así como la integridad de las instalaciones y los procesos industriales.
Mediante la identificación, evaluación y control de los riesgos presentes en el entorno laboral, se pueden prevenir accidentes, minimizar lesiones y proteger los activos de una empresa.
Es fundamental seguir las normativas y leyes de seguridad dentro del entorno industrial, como la norma ISO 45001, para asegurar el cumplimiento de los estándares mínimos en materia de seguridad y salud ocupacional.
Además, es importante promover una cultura de seguridad en la empresa, involucrando a todos los trabajadores en la identificación y comunicación de posibles riesgos.
El análisis de riesgos requiere de un enfoque sistemático y multidisciplinario, donde diversas herramientas y métodos pueden ser aplicados para garantizar resultados efectivos.
La experiencia personal y el conocimiento de cada industria son elementos clave para llevar a cabo un análisis de riesgos exitoso.
En definitiva, el análisis de riesgos en entornos industriales es una herramienta poderosa y necesaria para prevenir accidentes, proteger a los trabajadores y salvaguardar las instalaciones y los procesos industriales.
Siempre vale la pena invertir tiempo y recursos en esta práctica, ya que contribuirá a crear un entorno laboral más seguro y saludable para todos.
Preguntas frecuentes
1. ¿Cuál es la diferencia entre riesgos físicos y riesgos químicos en la industria?
Los riesgos físicos en la industria se refieren a condiciones o situaciones que pueden causar daño físico a los trabajadores. Algunos ejemplos de riesgos físicos son el ruido, las vibraciones, la radiación, las altas temperaturas y las caídas.
Por otro lado, los riesgos químicos en la industria están relacionados con la exposición a sustancias químicas peligrosas, como productos tóxicos, inflamables o corrosivos. Estos pueden representar una amenaza para la salud y seguridad de los trabajadores si no se manejan adecuadamente.
2. ¿Por qué es importante realizar una evaluación de riesgos cualitativa y cuantitativa?
La evaluación de riesgos cualitativa y cuantitativa son enfoques complementarios y se utilizan para evaluar diferentes aspectos de los riesgos en un entorno industrial. La evaluación cualitativa se basa en la experiencia y el juicio subjetivo de los expertos para asignar valores de probabilidad y gravedad a los riesgos.
Permite una evaluación rápida y ofrece una visión general de los riesgos más importantes. En cambio, la evaluación cuantitativa se basa en datos numéricos y estadísticas para calcular el nivel de riesgo de manera más precisa. Consta de una recopilación y análisis detallado de datos y puede dar una idea más precisa de la magnitud de los riesgos.
Ambos enfoques tienen ventajas y desventajas, y se pueden utilizar de manera complementaria para obtener una evaluación completa del riesgo.
3. ¿Qué significa el término HAZOP y en qué consiste su aplicación?
El término HAZOP significa "Hazard and Operability Study" o Estudio de Peligros y Operabilidad. El HAZOP es una técnica utilizada en la industria para identificar y evaluar los peligros y desviaciones potenciales en los procesos industriales.
Se lleva a cabo mediante un proceso sistemático de revisión y análisis de todos los componentes de un sistema, identificando posibles desviaciones o desviaciones inseguras que puedan causar daños a las personas, el equipo o el medio ambiente.
El objetivo del HAZOP es identificar las medidas de control necesarias para prevenir o mitigar los riesgos identificados y garantizar la seguridad y eficiencia de los procesos industriales.
4. ¿Cómo puede una empresa cumplir con las normativas de seguridad como la ISO 45001?
Cumplir con las normativas de seguridad, como la norma ISO 45001, requiere de un enfoque sistemático y un compromiso constante por parte de la dirección y el personal de la empresa. Estos son algunos pasos clave para implementar y cumplir con la norma ISO 45001:
1. Realizar una evaluación inicial de conformidad: Es importante realizar un análisis inicial para determinar el nivel de cumplimiento actual de la empresa con los requisitos de la norma ISO 45001. Esto permitirá identificar las áreas de mejora necesarias.
2. Establecer políticas y objetivos de seguridad: La empresa debe establecer políticas y objetivos de seguridad claros y medibles, que estén alineados con los requisitos de la norma ISO 45001.
3. Implementar un sistema de gestión de seguridad: Se debe establecer un sistema de gestión de seguridad basado en los requisitos de la norma ISO 45001.
Esto incluye la documentación de procedimientos y políticas, la asignación de responsabilidades y la implementación de controles adecuados.
4. Capacitación y concientización del personal: Es importante capacitar y concienciar a todo el personal sobre los requisitos de seguridad y la importancia de cumplir con las políticas y procedimientos establecidos.
5. Realizar auditorías internas: La empresa debe llevar a cabo auditorías internas periódicas para evaluar el cumplimiento de los requisitos de la norma ISO 45001. Esto ayudará a identificar áreas de mejora y corregir posibles desviaciones.
6. Obtener la certificación: Finalmente, una vez que la empresa esté cumpliendo con los requisitos de la norma ISO 45001, puede someterse a una auditoría de certificación realizada por una entidad de certificación acreditada.
Si se cumplen los requisitos, se otorgará la certificación ISO 45001.
Es importante recordar que el cumplimiento de la norma ISO 45001 no es un objetivo final, sino un proceso continuo de mejora y adaptación a los cambios en el entorno laboral. La empresa debe asegurarse de mantener y mejorar su sistema de gestión de seguridad a lo largo del tiempo.
Deja una respuesta
Te Puede Interesar: